June 2009 Vol. 64 No. 6
Features
Frozen Sand Provides Directional Drilling Challenge
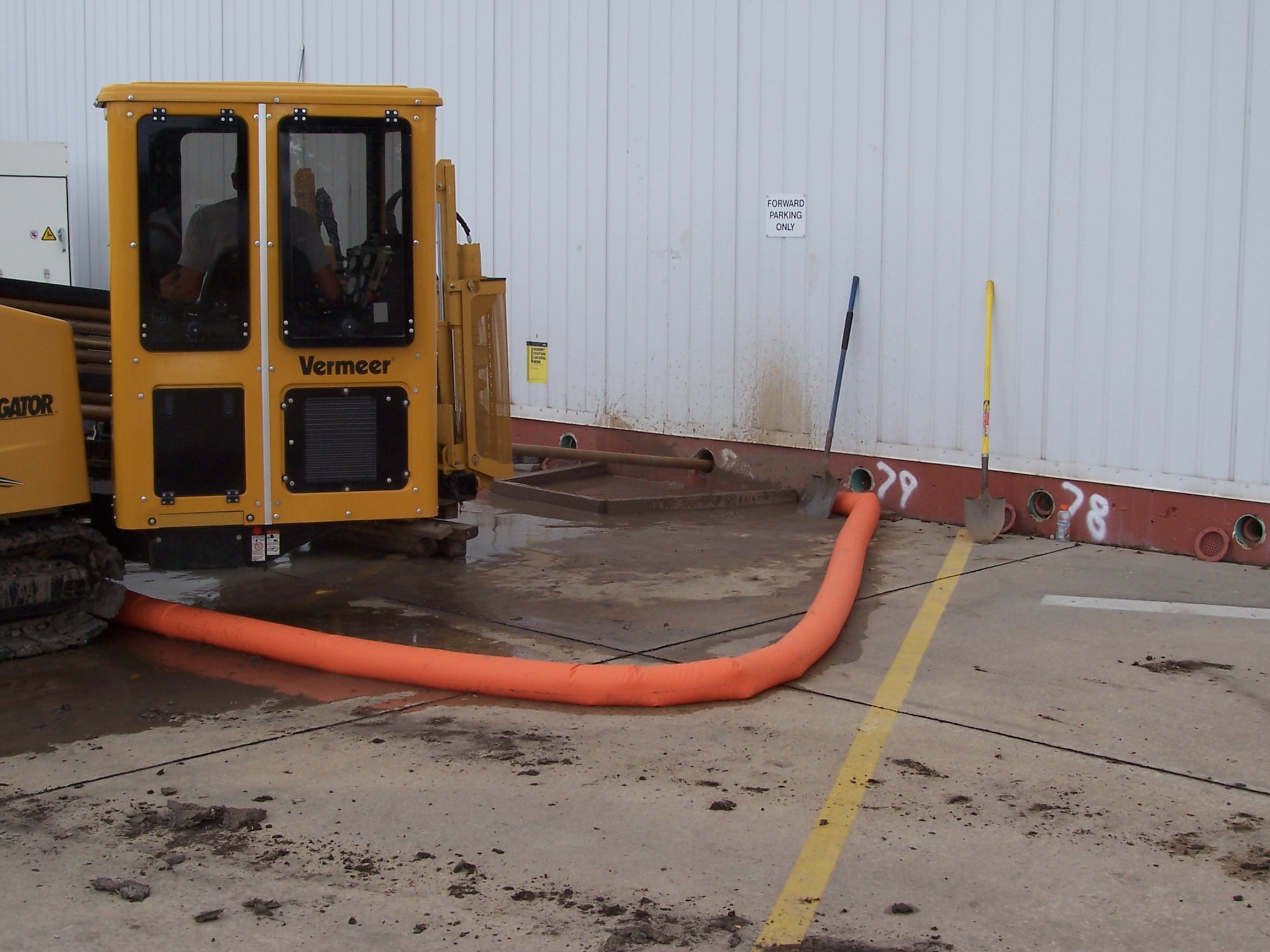
What acts like solid rock, but really isn’t rock and is located in the heart of the Midwest? That’s a good question, and Tim Huttmann with TH Construction Company, based in Omaha, NE, knows the answer.
Huttmann recently installed a radiant heat system under a 512 foot by 1,100 foot cold storage facility in Kansas City, MO. While the obvious question is why would a cold storage facility want to install a radiant heat floor, the answer proved quite simple.
The old radiant heating system was installed when the cold storage facility was constructed in 1990. Heat from the compressors dispersed through clay tiles that ran under the building. As compressor technology improved, so did refrigerants that didn’t produce as much heat. Eventually, the clay tiles didn’t have enough warm air flowing through them and many froze shut or broke. The lack of radiant heat resulted in excessive heaving and buckling of the cold storage facility floor during the freeze and thaw periods common in the Midwest.
The soil under the facility consists mainly of sand. When factoring in the frost line that runs close to 28 feet deep directly under the cold storage facility year round, the result is a ground structure that resembles some of the toughest rock formations.
This isn’t the first time Huttmann has taken on this type of a project, but it is the largest he’s ever tackled.
“We’ve completed a number of projects like this under buildings, but this was by far the largest and most difficult,” says Huttmann. “In fact, we’ve never dealt with ground conditions like this before, so it was a lot of trial and error.”
128 bores to go
The project involved installing the radiant heating system under one half of the cold storage facility. This required Huttmann to bore 128 holes each measuring 550-feet long with four feet of spacing between each hole.
Huttmann – not knowing exactly what it would take to bore through the frozen sand – decided to conduct test bores in advance of the project starting date. He arrived on site with his Vermeer D100x120 Navigator horizontal directional drill and a Vermeer MX240 drilling fluid system. Huttmann soon discovered the ground was going to be more difficult than anticipated.
“As we moved toward the center of the building the ground conditions became much harder,” says Huttmann. “In fact, we tested five different drill heads before we found the right combination that gave us consistent production. We also found out the D100x120 provided a higher water flow than was needed and decided to use our new Vermeer D36x50 Series II Navigator drill instead.”
The D36x50 Series II was also chosen because the rig carried the right amount (total length) of drill stem and eliminated the need to offload additional rod baskets. In addition, the unit featured a climate controlled cab to protect the operator from the extreme summer heat and humidity common in the Kansas City area during August and cold Midwestern temperatures during December and January.
Huttmann started out using a four inch carbide blade drill head, but soon discovered the drill head was no match for the frozen sand. He ended up using a four inch mud motor, which handled the frozen sand, but in the last third of each bore tore up the roller carbide nubs and thus had to be replaced after every borehole was completed.
Changes while drilling
The drill was set up on the east side of the building with a setback of 10 feet. The operator bored through the frozen sand to a 4 foot by 4 foot concrete tunnel located dead center under the building. Once the bore was completed the crew pulled back a 1.5-inch PVC duct from the tunnel to the outside of the facility. During the pullback a bentonite mixture, similar to grout, was pumped into the borehole.
“On the first few bores we bored through the concrete wall of the tunnel,” says Huttmann. “But we soon discovered a power line ran along the tunnel wall and ended up boring just to the footings. Then we used a concrete saw to cut open the tunnel wall and reach the borehole.”
Once the PVC duct was in place, a ¾ inch rigid steel pipe was inserted into the conduit from the outside of the building towards the tunnel. The pipe was secured to the inside of the tunnel and then the PVC duct was removed. “The bentonite mixture helps hold the steel pipe in place and will enhance the heat dispersion process,” Huttmann explained.
Production varied from day to day depending on the ground conditions.
“When we started, we’d get two to three bores completed in a day,” says Huttmann. “But there were days when we only completed one bore. The frozen sand was so unpredictable.”
That wasn’t the only challenge. While the lines had to be installed at a depth of 24 to 30 inches, the team also had to avoid steel support piers. Each pier was 18 inches in diameter and set 36 inches deep into the ground. The pier was then set on a concrete pad. The team had to know where they were at all times.
To overcome this challenge Huttmann, used an Eclipse locator from Digital Control to monitor each bore. The only problem was that the locator operator had to be inside the facility which operates at a temperature of -20 F and then factoring in the wind chill it felt like 40 F below zero.
“We purchased arctic gear for the locator operator and two other crew members who were responsible for moving pallets,” says Huttmann. “The freezers also threw off the locator signal, so it was a slow process.”
While this was a pretty challenging project for Huttmann, he would take it on again.
“We get into pretty much all aspects of boring, from water, sewer, gas, power, some communications, geothermal and special projects like this,” says Huttmann. “The whole project involved a lot of unknowns, but our planning paid off and the drill performed beyond my expectations.”
FOR MORE INFORMATION:
TH Construction Company, (402) 616-3809
Digital Control Inc., (800) 288-3610, www.digital-control.com
Vermeer Corp., (888) 837-6337, www.vermeer.com
Comments