May 2009 Vol. 64 No. 5
Features
Laclede Gas Discovers Alternative Method For Cathodic Protection
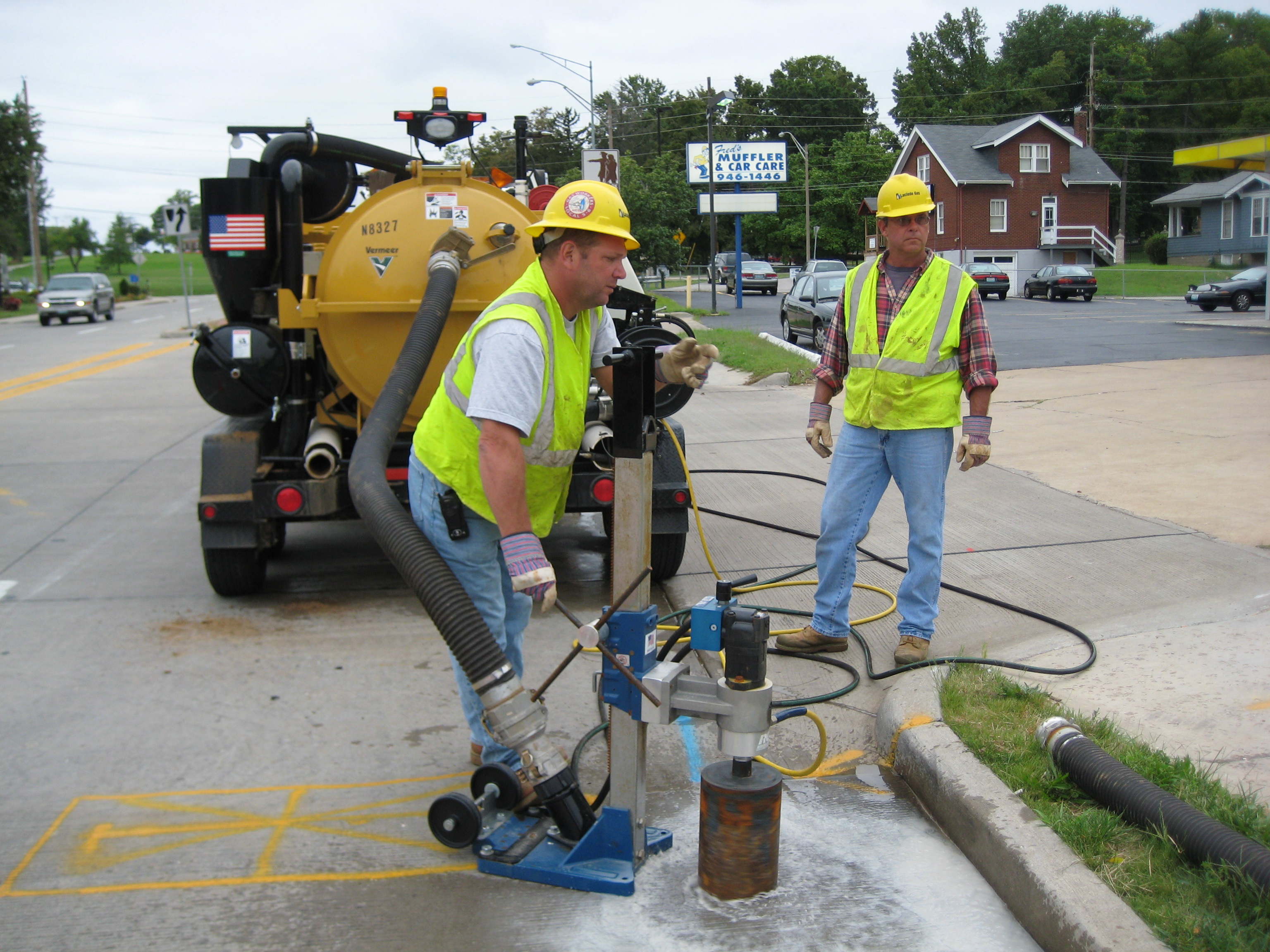
Dean Pieper, Ron Adler and Dave Biggs collectively have been involved in the natural gas utility business for 63 years and have seen a number of changes in the industry. They are part of the construction and maintenance department responsible for the installation and maintenance of more than 1,800 miles of steel gas lines for Laclede Gas in the North District of St. Louis.
Laclede Gas Company, based in St. Louis, MO, is the largest natural gas distribution utility in Missouri, serving 630,000 residential, commercial and industrial customers in the city of St. Louis and 10 other counties in eastern Missouri. The company operates more than 16,000 miles of gas lines, an underground natural gas storage field, a propane storage cavern and propane vaporization facilities.
Part of the ongoing maintenance of the system is the installation of sacrificial galvanic anodes for cathodic protection of the steel gas distribution lines to control corrosion. This is achieved by burying a more active, easily corroded metal (typically a magnesium anode) and electrically connecting it to the steel gas line to be protected. The anode provides a negative charge to the steel line, which enables the line to resist electrochemical corrosion.
“We’ve been installing anodes along our lines for decades as a routine maintenance program,” says Dave Biggs, a Laclede Gas construction and maintenance department employee. “The anode will cathodically protect the gas lines in case there’s a problem with the coating. The anode is designed to corrode to protect the gas line. Therefore the anode must be replaced periodically.”
Checking the lines requires a crew of inspectors who take potential readings of the gas lines at designated test point locations. Should the potential reading for a section of pipe drop below a negative 850mV and it is determined that additional cathodic protection is required, an inspector will issue a ticket for the installation of an anode in that designated area.
Past procedure
In the past, installing an anode required excavation by hand or equipment over the steel lines. A majority of the lines are located under streets layered with eight inches of concrete, which would require the crews to use a jack hammer or concrete saw to open the street. A dry vacuum would then be used to extract the soil and replace the anode. The process took hours and in some cases required the replacement of an entire concrete pad costing almost $5,000.
That all changed when Greg Borgschulte with Vermeer Midwest contacted Laclede Gas in the fall of 2008.
“Greg showed us how a vacuum excavator equipped with a core saw could speed up our process,” says Dean Pieper, equipment general foreman for Laclede Gas. “Now we can install an anode in under two hours with minimal rehabilitation to the street. It has saved us precious time and money.”
The procedure is relatively simple and fast. The crew arrives on site and begins their set up process. An 8 inch round diamond tip core saw is placed at the desired spot where the anode will be installed near the main. The core saw is powered by hydraulic pump installed on a McLaughlin V500LTHD vacuum excavator. To stabilize the core saw, the vacuum suction hose is connected to the saw and the suction from the vacuum securely holds the saw down to the concrete. A water hose is attached to the core saw to help keep the blade cool during the core process.
“With the core process it only takes five to 10 minutes to complete the bore,” says Biggs. “The coupon typically measures eight inches in diameter and 8.5 inches thick. We even use the suction from the vacuum to extract the coupon out of the street.”
Once the coupon has been removed, the vacuum is used to extract the soil. The anode must be installed below the gas main, so the depth can range from four to 8 feet depending on the depth of the main.
“In the past we used air to break up and extract the soil,” says Biggs. “Now we use water and it’s much faster. The McLaughlin unit generates 3,000 psi of water pressure through the wand and turns the soil into slurry within minutes, resulting in a nice clean hole to install the anode.”
Finishing touches
The crew will lower the anode into the hole, remove the coating on the main and attach the wires using a Cadwell Welder. When the connection has been made, the coating is repaired and the hole is backfilled with crushed rock to within an inch of the bottom of the concrete pad. An epoxy is then placed on top of the crushed rock to within 2 inches of the top of the hole. The coupon is inserted back into the hole and the excess epoxy is removed.
“Sometimes we get into areas where the main or carrier pipe can be deep,” says Pieper. “In these cases, the crews use a special tool to weld the anode wires onto the pipe. It can be a difficult task when you’re only working with an eight inch diameter hole.”
Laclede’s North District currently has two crews working on this project and each can average six installations daily and has doubled their daily output.
Ron Adler explains that some installations are more difficult than others.
“A lot of times we’ll have to put the anodes maybe six or 8 feet away from the main especially if the line is in the street,” he says. “In these cases we will dig a hole away from the main, then use the water wand to bore a hole horizontally over to the main and pull the wire through. It helps save us a lot of time and rehabilitation costs.”
Pieper reveals the new process is helping Laclede Gas in other ways as well.
“We are finding all kinds of uses for the vacuum excavator from cleaning valve boxes to digging post holes – the unit is very versatile and is used on a daily basis,” he says.
FOR MORE INFORMATION:
McLaughlin, (800) 435 9340, www.mightymole.com
Laclede Gas, (314) 621-6960, www.lacledegas.com
Comments