October 2009 Vol. 64 No. 10
Features
Slide Rail System Speeds UV Waterline Construction
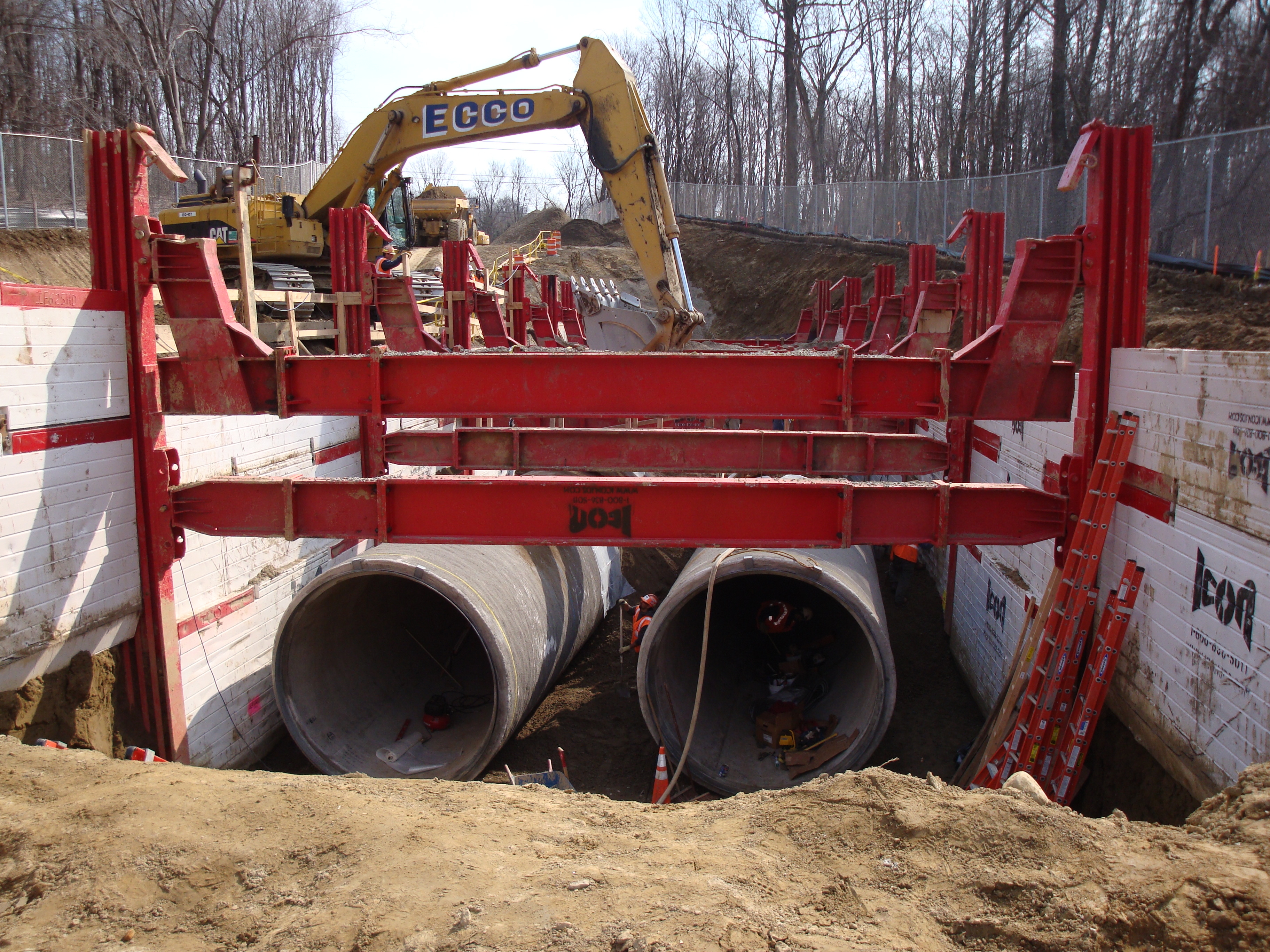
One of the world’s largest ultraviolet (UV) water treatment facilities is under construction in Westchester County, NY.
When the $1.4 billion plant becomes operational in late 2012, it will have the capability of treating 2 million gallons of water per day supplied by the Catskill and Delaware aquifers, which provide more than 90 percent of the drinking water for New York City.
UV light purifies water by altering the DNA of water based microbes to prevent them from replicating. Many experts consider UV water treatment to be more ecologically friendly than conventional methods using chlorine.
The project owner is the New York City Department of Environmental Protection. Construction is being performed by a joint venture named SEW. The construction consortium is comprised of: Skanska USA Civil Northeast Inc, Whitetstone, NY; ECCO III Enterprises Inc., Yonkers, NY, and J.F. White Contracting, Framingham, MA. Construction management is a joint venture between consulting engineering firms Malcolm Pirnie, White Plains, NY, and CH2M HILL, Englewood, CO.
Much of the project involves underground work. The facility’s design uses gravity to move water within the facility. From there, valves and sluice gates control water flow to 56 UV treatment units, each of which can process 40 million/gpd of water. Stainless steel chambers contain multiple UV lamps below the level of the flowing water. The treated water flows to a down-take shaft and enters into the distribution pipelines. Gravity will convey water throughout the system.
When complete, the facility will have approximately 10,000 linear feet of encased pipe in diameters that range from 48 to 144 inches. Shoring excavations in often challenging conditions required a variety of methods. Slide rail shoring systems are the preferred shoring method with contractors and owners of projects requiring installation of long runs of large diameter pipelines versus conventional steel sheeting methods, which generally require more time and labor.
Extensive excavation
A slide rail system is a component shoring system comprised of steel panels similar to trench shield side walls and vertical steel posts. It is installed simultaneously as the trench or pit is excavated by sliding the panels into integrated rails on the posts – either double or triple rails depending on needed depth – then pushing the panels and posts incrementally down to grade as the pit is dug. Slide rail systems can be used in a variety of configurations.
One portion of the project called for a segment of nine foot diameter prestressed concrete cylinder pipe (PCCP) in tight, deep areas. ICON, East Brunswick, NJ, designed and provided a triple slide rail system that met the needs and criteria of the project to install this pipe to a maximum depth of 25 feet.
“Installation requires a smaller crew with components put in place and removed by an excavator,” says David Crandall, ICON vice president. “Modular design provides flexibility and maximum use on a variety of jobs. There is no need for interior walers or beams, which allows for more working room and ease while digging. Slide rail systems allow multiple operations to be performed simultaneously to expedite work. We find slide rail systems can lower shoring costs from 30 to 60 percent compared to conventional systems.”
ICON also provided the site specific engineered drawings, calculations and New York Professional Engineered stamps for submittal and approval through D.H. Charles Engineering, Santa Rosa, CA. The system was provided on a rental basis to SEW and was delivered on February 2009 along with a qualified field technician who was on site for the installation and kept a continuing presence on the project afterwards, working with the crew and to ensure effective operation of the system.
“Because the contractor would install 20 foot sections of concrete pipe,” says Crandall. “We had to design the system accordingly by using 20, 1/2 foot long lining plates for the required horizontal clearance and strong triple rail with large bracing for the 15 foot cantilever required under the bottom brace of the system. This would provide proper clearance for the pipe crew.”
Crane adds weight
ICON also took into consideration the 275-ton crane that would be lowering the massive concrete pipes into the trench. The crane was also located in close proximity to the trench. This amount of weight added additional load and deflection on the side walls of the system. ICON was able to overcome this issue due to their slide rail design that offers large rails made out of high grade steel and solid wall panels designed to withstand additional loads.
“ICON is no stranger to large concrete pipe jobs,” says Richard Odierna, New York Shoring Consultant for ICON. “The section of the slide rail system itself was a six-bay, triple-slide rail trench, that was 130-feet long, 32-feet wide and 20-feet deep, and was designed in combination with benching and sloping to handle the overburden that would be encountered in certain areas. Also, ICON supplied the contractor with extra rail pairs for handling curves and turns in the pipe run.”
Odierna was responsible for the collaborative effort and coordination between the two agencies to carry out this challenging underground operation.
Installation of the 10 foot OD concrete segments was completed in the late summer of 2009.
“Compared with other systems considered for this project, ICON’s slide rail system proved to be the best not only from an engineering standpoint but field technical support as well. If the need arises, given the choice, I wouldn’t think twice about using this system again,” says Mark Giordano, superintendent. for SEW construction.
Icon provides slide rail systems on a turnkey basis for projects, from start to finish, including pre bid consultation, design, rental, sale or lease with field training.
FOR MORE INFORMATION:
ICON Equipment, (800) 836-5011, www.iconjds.com
Comments