December 2010 Vol. 65 No. 12
Features
Technology Report Released For Force Main Rehab
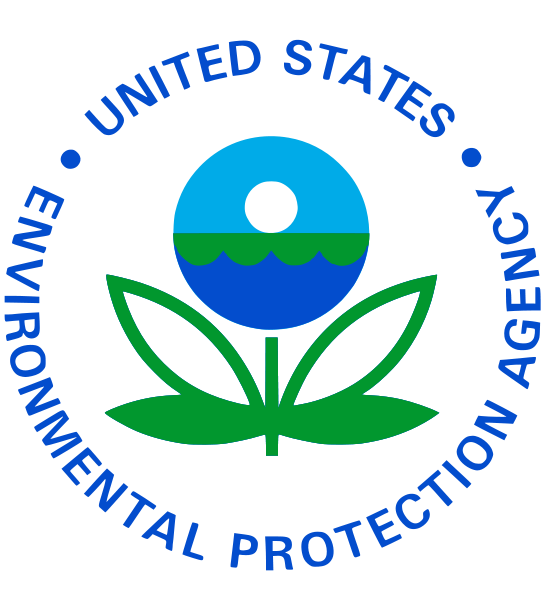
Editor’s Note: A U.S. Environmental Protection Agency (EPA) report published earlier this year contains a wealth of information about rehabilitation technologies available for sewer force mains. The report, “State of Technology Report for Force Main Rehabilitation,” was prepared as part of the EPA’s Sustainable Water Infrastructure Initiative. Under this program, research is being conducted to improve and evaluate innovative technologies that can reduce costs and increase the effectiveness of the operation, maintenance and renewal of aging drinking water distribution and wastewater conveyance systems (EPA, 2007). Robert S. Morrison, P.E., Jason Consultants LLC, was a principal author of the report, and below is his summary of its contents.
The main portion of the report is a review of all known technologies that could be utilized in the rehabilitation of sewer force mains. It includes discussions of currently used technologies, as well as potential cross-over technologies previously used to rehabilitate water mains and gravity sewers, with technology-specific data sheets included in the appendices.
The sewer force main system in the United States is comprised of approximately 60,000 miles of pipe. Only two percent of the force mains have been in service for over 50 years, making the force main network relatively young compared to the water network where nearly half are over 50 years old. However, force mains, especially large-diameter ones, tend to be more critical as the consequence of failure can be significant. Given the aggressive nature of the effluent, and that over 30 percent of force mains are at least 25 years of age, failures are starting to increase in frequency.
For ferrous pipes, which represents over 63 percent of all force mains, internal corrosion is the leading cause of failure at 26 percent, followed by third-party damage at 19.4 percent and external corrosion at 19.2 percent. Corrosion and structural failure together account for 54 percent of failures.
The report discusses the various renewal practices and technologies available, focusing on rehabilitation and replacement, and briefly touching on repair options (which are not the focus of the report).
Rehabilitation of sewer force mains
In rehabilitation, the existing pipe becomes part of the renewal work. Methods include spray-on linings, close-fit linings, CIPP and woven hose lining systems. Technologies for each of these categories are discussed in this report, including cleaning requirements prior to rehabilitation. Because only limited rehabilitation work has been undertaken to date on sewer force mains, many of these systems were originally developed for water main rehabilitation, but are adaptable to sewer force mains.
Spray-on linings are one of the easiest rehabilitation methods when the objective is to provide corrosion protection to the interior surface. They include cementitious and polymer materials. A new family of polymer spray-on linings, base on the use of polyurea, is finding rapid acceptance for lining manholes, wet wells and other structures including pipes, exposed to corrosive environments. The benefits of polyurea are its fast cure and that it can be sprayed to a thickness of up to two inches, potentially functioning as a structural or semi-structural liner, as well as providing corrosion protection.
Close-fit liners, also called modified sliplining, are another method of rehabilitation. This process involves use of a thin walled liner with an outside diameter similar to the inside diameter of the pipe being rehabilitated, in which the diameter of the liner pipe is reduced for easy insertion. Polyethylene (PE) pipe is used for the diameter reduction process known as symmetrical reduction, and PE and polyvinyl chloride (PVC) pipe are used in the fold-and-form diameter reduction process.
CIPP is the leading method for rehabilitation of gravity sewers. Many new variants have recently been introduced. The variations are primarily in tube construction, method of installation, curing method, and type of resin.
Woven hose linings are made from either polyester, glass or aramid fibers woven into a hose-like configuration. The three types of systems include adhesive backed linings, non-adhesive backed linings, and glass-reinforced thermoplastic linings.
Replacement technologies
Several technologies are available for offline and online replacement. The most common offline method is open cut, which involves the installation of new pipe without regard to the line and grade of the existing pipe.
The second most utilized method is sliplining, an online method in which a new pipe with a smaller diameter than the old one is inserted and either pushed into or pulled through the old pipe. Pipe sections can be pre-assembled by butt fusion or joined together one at a time as needed. PVC, DI and fiberglass reinforced plastic/glass reinforced plastic (FRP/GRP) are typically sliplined in this fashion, while HDPE is butt welded. Fusible PVC is also finding use in this application.
Another online method, pipebursting, involves using a bursting or splitting device to break up and disperse the old pipe while pulling a replacement pipe behind the device. This process can be used for diameters from four to 60 inches, utilizing high density polyethylene (HDPE), PVC or DI as replacement pipe. Sometimes upsizing the existing diameter can be accomplished by this process if needed.
Gaps
The report also identifies gaps between what is needed and what is available, e.g.: the biggest need is for a fully structural liner which can be installed in a live sewer – unlikely for at least a decade; but, there are vendors currently testing and developing liners with the purpose of achieving a minimum 50 year design life.
Findings, recommendations
One method of assisting owners in their efforts to apply some of these emerging technologies will be in the publication of demonstration projects and case studies. Also, setting up a decision support system to help a utility ask the right questions, so that a viable rehabilitation solution emerges, is paramount.
The decision-making process relies on data from inspection to assess risk levels and to decide on necessary actions. One of the key data elements needed is verification of the long-term performance of pressure rehabilitation systems. This should be a major objective of the retrospective and demonstration projects which are currently under way as part of another phase of this overall EPA project.
Complete report available free
The report may be downloaded at no cost from the U.S. EPA website, Risk Management Research/Publications. Click the 2010-2008 tab at http://www.epa.gov/ORD/NRMRL/publications.html, or go to http://www.epa.gov/nrmrl/pubs/600r10078/600r10078.pdf to go directly to the publication.
Comments