February 2010 Vol. 65 No. 2
Rehabilitation
Relief Sewer Project Wins Award
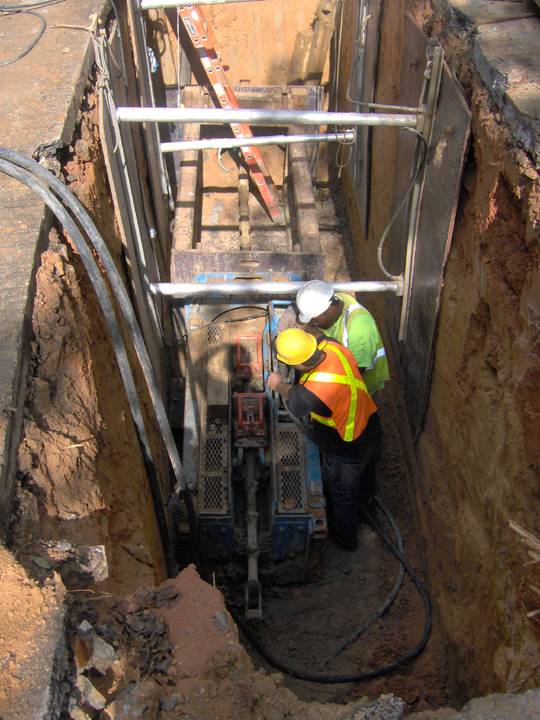
Project Engineering Consultants (PEC), Phoenix, AZ, won an Engineering Excellence Award for the city of Phoenix Water Services Department 2005 Relief Sewer Project, constructed at 35th Avenue and Peoria Avenue.
The firm was recognized for its use of trenchless technology to install upsized relief sewers at the 29th Annual Engineering Excellence Awards Gala held by the American Council of Engineering Companies (ACEC) of Arizona, Oct. 24, 2009.
PEC chose static pipe bursting to install No-Dig vitrified clay pipe (VCP), an inert product with a life expectancy of more than 100 years. The pipe bursting benefits included a shortened construction schedule, reduced social-economic impact, less disruption to traffic and reduced carbon emissions. The static pipe bursting installation was the first in the United States to accomplish a maximum drive of 448 feet using VCP and the first to perform a double upsize pipe burst with VCP. Kiewitt Construction was the contractor for this project and the Grundoburst 2500G manufactured by TT Technologies, was used on site.
The final plans and specification using static pipe bursting resulted in a GMP of $5.3 million and decreased the construction schedule from 12 months to nine months. The initial cost saving to the city was more than $2 million over traditional open-cut construction.
Population growth that taxed Phoenix’s collection system prompted the city to develop the Sanitary Sewer Relief and Replacement Program to tackle these issues. Full pipe replacement and upsizing, diversions and other techniques were considered as solutions to this potential capacity deficiency. The use of trenchless technologies was determined to be a suitable alternative approach to minimize the impact created by all of these construction projects. Pipe bursting was chosen to fulfill the need for upsizing these capacity deficient pipes without open trenching their streets.
Project details
The total project consisted of upsizing of nearly 6,400 linear feet of 12- and 15-inch pipe with a 10- to 20-foot depth within major streets with the usual multitude of utilities. Trenchless equipment manufacturer TT Technologies, Aurora, IL, provided the Grundoburst static pipe bursting equipment and technical instruction during the design and construction phases. Mission Clay Products, Corona, CA, supplied the 15- and 18-inch No-Dig VCP, which the city preferred.
One of the first sections replaced included bursting and replacing 3,938 feet of existing 12-inch VCP with 18-inch VCP. Soil conditions in the area proved to be one of the biggest challenges. The original pipe to be burst was bedded in a soft, dry, silty sand material and installed in a trench width ranging from 3 to 5 feet depending on depth. Existing trench depths range from 10 to 20 feet deep. Dry, dense soil conditions adjacent to the existing trench and the existing sewer pipe alignments, among other minor obstacles, caused some production issues. However, pipe bursting has proven to be a cost effective process for upsizing capacity deficient sewers with VCP.
Static bursting with VCP
Static bursting equipment has evolved from a cable-pulled bursting head to a more sophisticated system that uses a system of interlocked rods to pull the bursting head. The rigid rods do not stretch under heavy pulling as a cable would. This becomes particularly crucial when bursting with sectional pipes such as No-Dig VCP. Mission Clay Products first introduced No-Dig vitrified clay jacking pipe in 1992. Manufactured from 100 percent natural materials, VCP is a blend of clays, shale and slate. For this particular project in Phoenix, the bursting equipment was designed and assembled for the specific purpose of bursting the existing VCP and towing in the new, non-restrained joint VCP.
PEC worked closely with utility contractor Kiewit Western, Omaha, NE, to develop an innovative approach to increase the capacity deficiencies with minimal socio-economic impact. The pipe handling, assembly and bursting plan worked very well when put into operation. Launch and receiving pits were located in areas where existing manholes were to be replaced. The manholes were located at approximately 400-foot intervals. The pits were adequately shored with trench boxes to stabilize the walls of the pit. This provided a safe environment for workers and ample room for equipment and pipe.
The Grundoburst 2500G would prove necessary to use all of its 315 tons of pulling capacity in the difficult soil conditions encountered on the project. The machine could be easily rotated 180 degrees in the launching pit and begin bursting pipe from the opposite direction. The machine utilizes Quicklock rods. The rods were connected to a special expander for 18-inch VCP (22.14-inch O.D.). The expander O.D. was 24 inches. The expander had a special internal socket arrangement for the lead piece of VCP to butt against. As sections of pipe were installed, additional Quicklock rods were added to the trail end of the expander and then the new pipe section was slipped over the rods.
The cylinder pack with pressure plate that was pinned to the rods provided 40 tons of force to keep the assembled pipe segments in compression as the bursting head was pulled toward the static pipe bursting machine. Cycle times for each section of pipe to be assembled and pulled forward during bursting began at an average rate of 1 foot per minute. As the project progressed, the crew became much more efficient resulting in average rate of 2 feet per minute. Thus, a typical 350 linear foot reach was completed in 2 to 3 hours.
Comments