March 2010 Vol. 65 No. 3
Features
Culvert Replacement On the Ice Road Truckers Highway
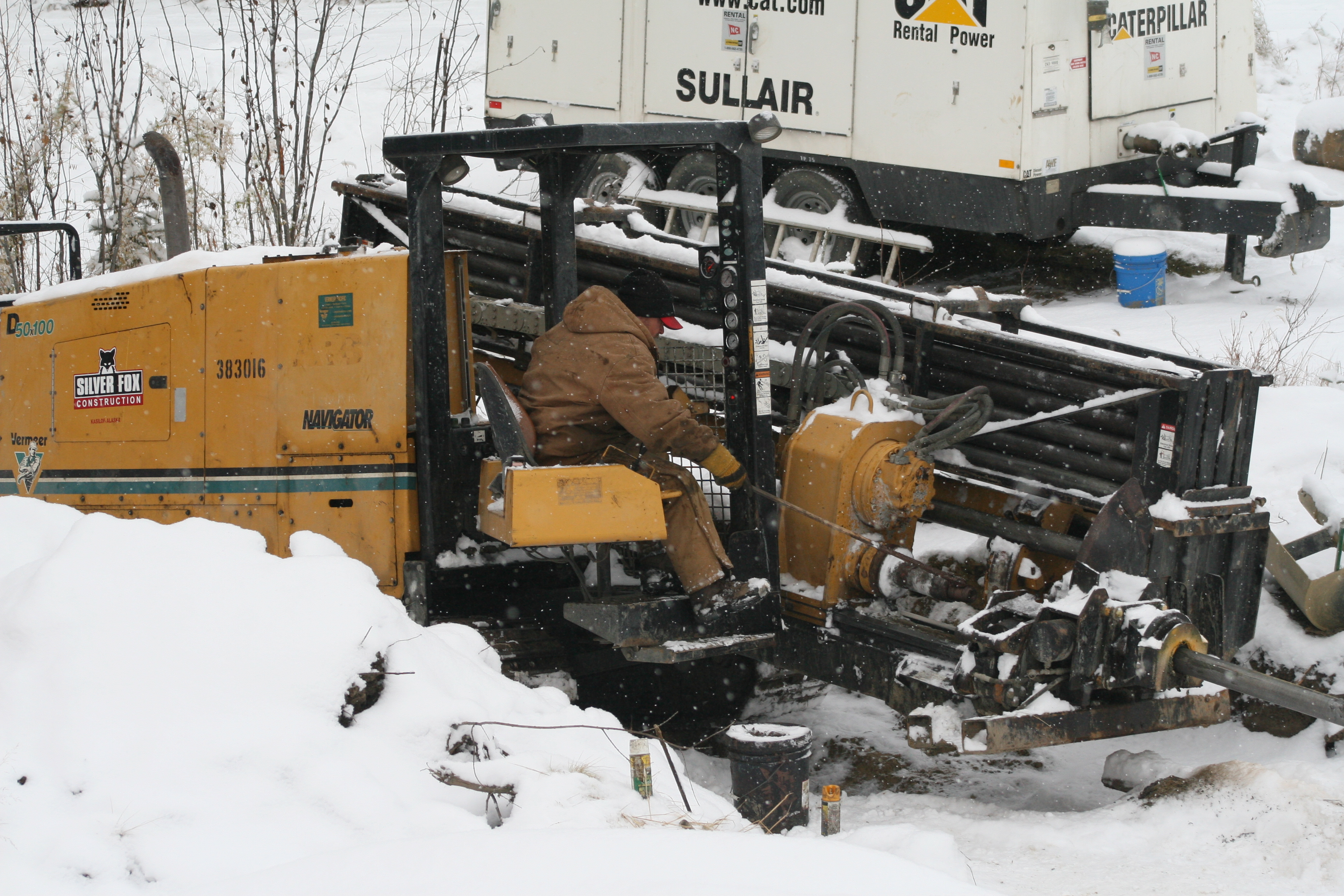
Harr Technologies’ trenchless method of cleaning culverts and its successful use on projects in Alaska resulted in company owner Bob Harr being asked to help solve a critical problem threatening to close the James Dalton Highway, well known to American television audiences from the History Channel’s series, Ice Road Truckers.
The problem facing Alaska highway officials was a collapsed seven foot diameter multi plate culvert beneath a remote stretch of highway three hours north of Fairbanks. Keeping the highway open is critical – it is the only land connection to the Prudhoe Bay oil fields on the North Slope.
The 164 foot long culvert was buried 79 feet deep in mixed, frozen soils. The condition of the collapsed culvert made it impossible to clean and return to service making replacement of the failed culvert the only option. Silver Fox Construction, also owned by Harr, was selected to perform this critical part of the project.
“The condition of the culvert threatened collapse of the road which had to be prevented at any cost,” said Harr. “Closing the road for the time required to dig up and replace the failed culvert was out of the question, and limited right of way and other factors ruled out building a temporary detour.”
To accomplish the job, a trenchless solution appeared to be the only option.
Alaska officials were familiar with Harr Technologies’ trenchless culvert cleaning process, and Harr was brought into discussions about the problem. Ultimately it was agreed to try a combination of the Harr cleaning process and pipe ramming to install a new 96 inch diameter pipe that would be rammed through the cleared space.
The decision helped the primary contractor, Hamilton Construction, Skagway, AK, keep the road open without developing a detour, preventing the need to transport and remove fill and avoiding other complications.
Short time, brutal conditions
Work had to be completed in a short period of time. “The work season is very short,” Harr said. “Even with sun shining, it is brutally cold. We started this project in September and within weeks, temperatures were falling and daylight was shrinking by nine minutes a day. By October, temperatures had fallen to more than 30 degrees below zero Fahrenheit. Pipe and other materials were shipped to Seattle, barged to Alaska, then hauled from Anchorage to the project site, an 11 hour journey. Federal Bureau of Land Management permits had to be obtained for the storage of materials at the site because the state right of way was too small.”
An access road was built to the bottom of the ravine where a 50 by 50 foot pad was constructed. Water collecting in the low areas was diverted by pumping.
A 24 inch diameter Hammerhead pipe rammer was used to ram new 20 foot sections of pipe through the frozen soil. The machine develops up to 1,010 tons of force and can strike 150 blows per minute.
Steps in making the installation were to push in a section of new pipe, then remove soil and pieces of broken culvert with a horizontal directional drill using Harr Technologies patented culvert cleaning process. New pipe supported the weight of the earth above the culvert as earth and debris were removed.
To begin installation of the new pipe, an engaging tool was built to lock the hammer into the colletts that would fit the 96 inch pipe. “We set line and grade and started pounding,” Harr said.
A Vermeer D50x100 horizontal directional drill with 50,000 pounds of pullback then used Harr Technologies culvert cleaning system to remove earth and pieces of the collapsed culvert.
“We removed 20 feet of material every time we welded on a new section of casing,” Harr explained. “This helped eliminate weight to aid the forward movement of the hammer pushing the casing.
“Perma frost is tough to work in. When the road was built 50 years ago, the fill used contained all kinds of debris which contributed to make the soil very unstable. We used a contoured pull bucket blade to remove the material with the directional drill providing a controlled pull, rather than an uncontrolled pull with a cable.”
New spiral wound steel pipe was provided by Trinity Products, St. Louis, MO. The pipe is one inch thick and a 20 foot section weighs 14,000 pounds, making the logistics of moving and positioning the pipe with a large excavator in the extreme cold a challenge.
Multi-plate
About 70-feet in, the hammer encountered a collapsed area where the casing began hitting multi plates of the existing culvert. “We then had to provide roof support and start precutting the multi plate,” Harr said. “Pounding distances were shortened to two feet at a time to protect workers who were 80 feet below the road’s surface.”
The size of the 96 inch pipe was reduced by cutting out a section, using cables and lugs and making downsized pipe to telescope inside the pipe. After rebuilding engaging tools, pipe could be moved forward again. Another difficult area had to be mined by hand.
“The collapsed area was on unstable soil and we had to build a swinging trench box door for worker safety to precut the multi plate ahead of the casing,” Harr continued. “Progress was slowed by severe cold as temperatures dropped to 34 degrees below zero. The hammer was moved inside the 8 foot casing and warmed nightly by heaters with the eight foot pipe covered by a tarp.” After the Silver Fox crew pushed the pipe past the edge of the roadway and beyond, the primary contractor decided to complete the remaining distance by open cut.
“Providing heat to the equipment and to the casing so it would not freeze to the soil meant running generators 24 hours a day, seven days a week,” said Harr. “We had 200,000 BTU heaters blowing hot air into the casing to keep the hammer and the soil from getting too cold to move and operate. The darkness and the cold took a toll on us and the hours of work were shortened. The fifth wheels we stayed in soon also froze up and going to the bathroom became an issue. We used large plastic bags in the toilets, sealed them and let the bags freeze and disposed of them later.”
Silver Fox’s part of the project was completed in November.
Impressive accomplishment
Harr’s trenchless culvert cleaning and pipe installation methods have drawn praise from the Alaska Department of Transportation.
“Bob Harr has proven to the State of Alaska that culverts of varying diameters and length may be placed under an active roadway, giving the state a valuable alternative option for the replacement of failing culverts, and the ability to add new culverts as need arises using trenchless methods,” said Shawn Crites, project engineer, Alaska Department of Transportation and Public Facilities, Northern Region.
Crites said that if a culvert fails and is not able to be replaced, the roadway can be jeopardized. Using traditional trenched methods the roadway may have to be closed, or in cases where it is feasible to do half width construction, safety concerns come into play, and must be addressed with traffic control solutions.
“With the ever increasing environmental regulations,” he continued, “trenched methods produce another set of issues because of the amount of material that must be disturbed to replace a culvert. Culvert locations by nature are often near bodies of water. Much effort is required when using trenched methods to prevent the introduction of pollutants or sediment into these water bodies.
“The method that Mr. Harr has demonstrated generates minimal sediment,” Crites pointed out. “Waste materials are also minimized reducing the need for disposal sites and the costs associated with them. In summary we see advantages in using trenchless methods over the traditional trenched methods in many situations, especially on roadways with high traffic volume, tall embankments or singular access. Areas of enhancement include traffic safety; environmental concerns; cost saving in time, materials, personnel, and waste management; roadway integrity; seasonal flexibility; and greatly reduced inconvenience to the traveling public.”
FOR MORE INFORMATION:
Harr Technologies, (907) 262-6710, www.harrtech.com
Comments