November 2010, Vol. 65 No. 11
Features
Sensor System Records CIPP Temperature Readings During Installation
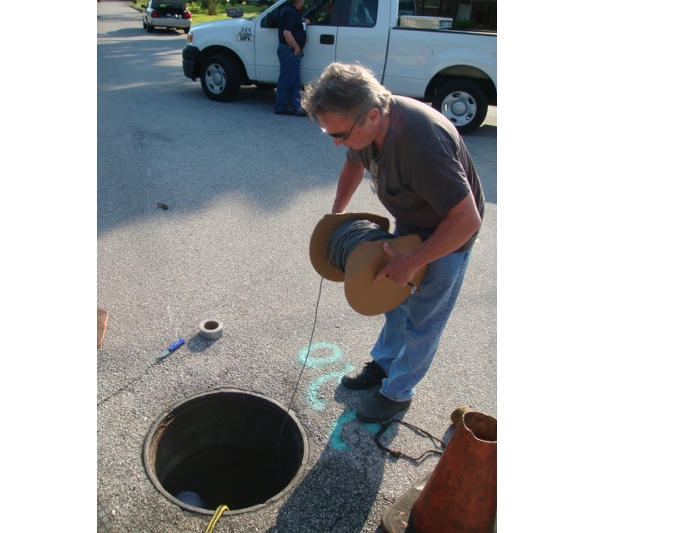
A small, high-tech Ohio business has developed technology that monitors temperature readings along a full segment of pipe during the curing of the CIPP (cured-in-place-pipe) lining process.
The procedure uses sensors strung by cable inside the pipe to be relined before the liner is inserted into the pipe, explains Jack Conte, president and chief executive officer of Zia Systems LLC.
After the liner is in place and the curing process initiated by steam, water or ultra violate light, the sensors read and transmit exothermic conditions to an on-site computer.
Conte says the Zia process is the first monitoring method that can provide accurate temperature measurements of the full length of pipe throughout the CIPP curing process.
The Zia system has been extensively tested and was introduced to the market at the WEFTEC show in October. Zia will exhibit and conduct a session during the educational program at the 2011 UCT show next January in Houston.
Zia CIPP sensor technology is available now through its United States distributor, MSE Technologies LLC. The system consists of software and wired sensors that can be either hooked up directly to a monitoring computer or wirelessly connected. The sensors come spooled and can be easily shipped and stored by the contractor.
Conte believes the sensing system is a significant advancement for the CIPP industry. Currently, he says, during a CIPP installation, cure temperature is controlled at the A (entry) and B (exit) stations.
“During curing, temperature readings are taken and logged at the A and B station every three minutes,” Conte says. “A crew member at the B station communicates recordings back to the A station. However, during curing, temperatures fluctuate between cold to hot from steam/hot water, followed by cooling. Temperatures inside the pipe can only be estimated.”
However, says Conte, to ensure proper and complete curing, it is best to know the temperature between the liner and host pipe for the complete length of the pipe.
Sensors
Zia’s solution for obtaining that information is to install sensors every 10 to 20 feet along the host pipe as the resin-based liner is cured. The distance between sensors varies with diameters of host pipes.
“Temperature readings are taken every three seconds in real-time and can be sent wirelessly by miniature radio transmitters to an on-site computer with proprietary Zia CIPP Intelligence System (CIPPI) software,” Conte explains. “The temperature readings can also be sent to on-site smart-phones such as an iPhone. For operators, sensor data helps improve process control and quality assurance. Knowing the temperature every 20 feet or less will help reduce the risk of curing failure. Software also allows the addition of other pertinent project information. The data also can be uploaded to a web-server for aggregation and customer reporting.”
Based in Galloway, OH, Zia Systems specializes in integrating wireless technologies that enable customers to remotely monitor and control assets. Zia’s founders and management team have a successful history of using global positioning satellite (GPS) and cellular technologies to track assets in the transportation, construction, energy and homeland security market sectors.
Conte says the CIPP temperature sensing system is Phase 1 of Zia’s entry into the utility market. Phase 2 will have enhancements to further insure the quality of CIPP installation process.
Comments