January 2011 Vol. 66 No. 1
Features
CIPP, Insituform Celebrate 40th Anniversary
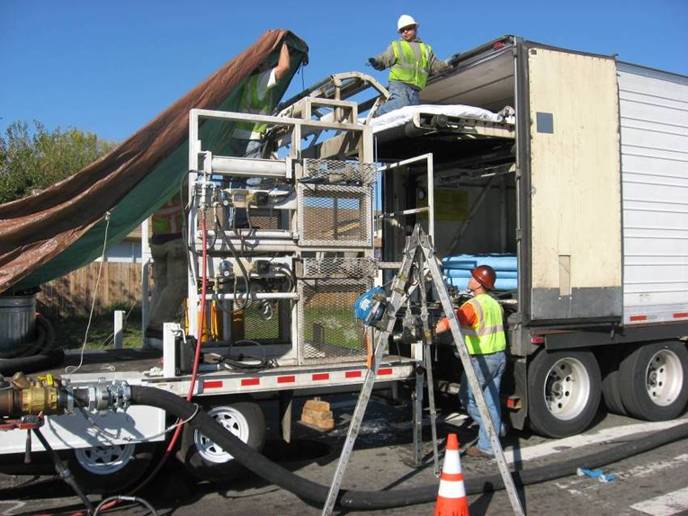
This year the cured-in-place pipe rehabilitation process and Insituform Technologies, the company that created it, celebrate a significant milestone: Insituform’s 40th birthday and the anniversary of the completion of the first commercial CIPP project, a 12-inch sewer.
Likely no one on that job recognized the significance of the project, but with the development of CIPP technology, Insituform started an industry that was to change the way pipes are rehabilitated.
The CIPP process involves inserting a resin-saturated, coated felt tube into a section of damaged pipe; using hot water or steam to cure the resin to form a tight-fitting, jointless, corrosion-resistant pipe within the old pipe; curing the resin-coated tube; and when curing is complete, using remotely-controlled robotic cutting devices to restore lateral connections.
The primary impact of CIPP has been on gravity-flow sewer infrastructure, but the benefits of the technology are expanding into other markets.
Insituform controlled use of the CIPP process until basic patents expired in 1994, allowing other companies to enter the market. Even so, Insituform has retained its leadership in the market, while making significant advances in the CIPP process and expanding into other markets.
“There are many unique facets to the Insituform story,” said Joe Burgess, president and chief executive officer. “We invented the technology and intellectual property rights allowed Insituform to lead the market we created, and we retain our position of leadership today.
“Look at any industry today, and I believe it is unusual that the company that created a new industry 40 years ago still leads that industry. It is very rare to retain the leadership position over that period of time, especially in a technical market.”
The Insituform CIPP process has reconstructed more than 19,000 miles of underground pipe infrastructure throughout the world. Today Insituform’s products and services are utilized in more than 36 countries worldwide, with pipeline operations on six continents.
Beginnings
Insituform CIPP was developed in the United Kingdom. Eric Wood applied for the first CIPP patent in 1970, and the first test installation — in an egg-shaped Victorian sewer — was completed later that year in London.
In 1971, Insituform Pipes & Structures Ltd. was founded and proceeded to use the new process to rehabilitate aging pipes in the UK, licensing the process to construction companies elsewhere. Early licensees included firms in Denmark, Austria, Germany, Finland and Sweden.
“The only trenchless pipe rehabilitation methods available before Insituform introduced CIPP were sliplining and grouting,” said Lynn Osborn, P.E., Insituform senior applications manager. “CIPP offers a much wider technical envelope.”
The introduction of CIPP gave engineers another option to dig and replace pipes, Osborn said.
“The new CIPP process,” he continued, “provided an innovative, structurally sound solution that was corrosion resistant, reduced infiltration, in most cases increased flow capacity of the sewer, took less time to implement and was less disruptive because it generally could be installed without excavation. CIPP was appealing to city officials because they didn’t receive as many customer complaints as a dig-and-replace project, and in most urban situations, it cost less.”
Osborn said there is no doubt that CIPP was the catalyst that launched the pipe rehabilitation industry, including rehab materials and processes and robots for installing lateral rehab products and camera systems for evaluating sewers and water lines.
“I attended a huge trade show in Germany last September,” said Osborn, “and the available products, processes and equipment were unbelievable. Eric Wood would be proud.”
Evolution
In the mid and late ‘70s, Eric Wood was busy improving the CIPP process.
In 1976, the United States Patent and Trademark Office issued two seminal patents, 4,009,063 and 4,064,211 that covered significant changes Wood developed for the CIPP process that included a change to the water temperature needed to cure the tube and the addition of water pressure as an installation method of CIPP. These changes led to increased installation production, greater resin stability and increased shelf life of a resin-impregnated tube. Ultimately, Wood developed 38 Insituform patents in the U.S.
The process obviously held great potential, but many system owners and consulting engineers in the conservative sewer industry were reluctant to try CIPP. Not only was it new, it was different, and radically different at that.
In the early years, each crew transported and used scaffolding for most CIPP installations. The scaffolding was erected over the installation manhole with a working platform at the top. For small diameter CIPP, a downtube was suspended from the top of the scaffolding. The wet out tube was fed through the downtube and cuffed back and banded to a steel boot at the bottom of the downtube. Water was then added to the downtube to provide the hydraulic head necessary to invert the wet out tube as it traveled through the sewer. Depending on the depth of the manhole, the scaffolding could be up to 30-feet high. This presented several safety issues such as falls, danger from falling objects and overhead electrical wires.
Even so, as word of successful projects spread, interest in CIPP increased.
In 1980, Insituform of North America was formed. At the time, the Memphis-based Insituform licensee’s territory covered most of the United States. Through several stages and acquisitions, the company evolved into today’s Insituform Technologies.
A key to Insituform’s continuing success as a company and establishing Insituform CIPP as a primary method of sewer rehabilitation has come through progressive improvements in the CIPP process and methods of installing it.
In 1983, the United States Environmental Protection Agency (EPA) recognized cured-in-place pipe as a viable alternative to conventional pipeline replacement methods.
Pioneer
Tom Driver is a pioneer in advancing CIPP technology who worked for Insituform
for 27 years before his retirement in June 2010. Driver holds 23 patents related to the
Insituform CIPP process.
“Tom Driver has been in the middle of every CIPP technical innovation from the time he joined the company in 1983,” said Burgess.
Driver’s involvement with Insituform’s CIPP process actually began when he was a consulting engineer in Illinois.
“In 1979, our consulting engineering firm was hired by the city of Northbrook to find the most effective method of solving infiltration and inflow problems affecting the city’s sewer system. The new Insituform CIPP process appeared to be well-suited for portions of this project, and I thought a trenchless solution would quote well in bidding,” Driver explained
A team was assembled to conduct a study, and it’s findings were included in a landmark report co-authored by Driver which later was referenced in ASTM F1216, the industry standard for inverted CIPP.
After joining Insituform, Driver had the opportunity to work closely with Eric Wood.
“We were colleagues and became close friends, and I learned a lot working with him,” said Driver. “Eric Wood never saw a problem as a problem, but rather as an opportunity, and he instilled that attitude in those around him.”
Driver said his first decade at Insituform was occupied improving the original product.
“Among other things,” he said, “we worked on resins, improved quality control in manufacturing, obtained new patents on the installation process that eliminated the need for scaffolding to create an inversion head.”
Other advances cited by Driver include the capability to rehabilitate larger size pipes — up to 96 inches in diameter; steam curing of resins which is faster, saving time on installations and which uses 95 percent less water; improving the process for reinstating laterals; and development of a CIPP lateral rehabilitation process.
“Much of my work,” Driver said, “has been developing better ways to install liners,
to get more in the ground in less time and then reinstate laterals faster so service can
be restored. We have improved processes and greatly increased production. In the early days, a crew would do two or three installations a week. Today it isn’t unusual for a crew to complete two or three installation per day, and some have installed more than one mile of tube in one week.
“To address these tasks, I was fortunate to be allowed to assemble a team which included Lynn Osborn and Rick Baxter, eastern region operator managers, currently with Insituform for 26 and 25 years respectively. We developed procedures so that now when curing begins, a crew can move to the next job and get started. We can do more in less time, and there is less ‘wasted’ time.”
Perfect opportunity
Looking back, Driver said he believes when he joined Insituform, he was in the right place at the right time.
“That’s true of our engineers today, too, I believe,” he added. “We continue to be innovative and our company recognizes the value in innovation. It is good for the company and good for the environment. I retired in June, but continue to work with Insituform as a consultant — in part because I enjoy my association with our younger engineers. They are enthusiastic about the future of this industry and our finding solutions to our everyday challenges.”
Insituform builds much of the specialized equipment needed for the process; boiler trucks, for example.
Insituform introduced the Controlled Heat Inversion Process (CHIP) unit in 1990.
Compared to the 20- to 30-foot high scaffolding formerly used, set-up of the CHIP unit proves easier and faster than erecting scaffolding and overall installation is more efficient for small-diameter CIPP. Safety benefits include decreased risk of a fall hazard, elimination of overhead wire danger, increased stability and improved set-up procedures.
Advances in compact closed-circuit television inspection cameras and robotic cuttings for reinstating laterals has been an important factor in the growth of CIPP.
Insituform crews understand their products and procedures and how to implement them.
“Insituform always has recognized the importance of training,” said Driver. “Training includes not only operation of equipment and the installation process, but safety. Safety never has been optional at Insituform.”
Basic patents that had allowed Insituform to be the sole provider of CIPP products and services expired in the mid 1990s, opening the market for the first time to competitors.
Continuing growth
Today the CIPP sanitary sewer market in the United States is estimated to be approximately $1 billion a year, and Insituform has about 50 percent of the market.
To fill demand, Insituform CIPP tubes are manufactured at Insituform’s manufacturing plant in Batesville, MS, and in the United Kingdom. Insituform’s management system received ISO:9000 certification in 1995, and the certification was renewed in 2008.
Insituform also is expanding CIPP markets with processes for pressure pipe, including force mains, raw water lines and other systems for potable pipeline repairs.
Said President/CEO Joe Burgess: “Our expansion falls into two basic categories. First we are taking our technical portfolio for gravity pipes to the drinking water side. We seek to recreate the wastewater profile and franchise on the drinking water side with improvements suited for pressure pipe. Robotics and retapping are more sophisticated, and basically the task becomes harder as pipe diameters become smaller.
“We believe the pressure market can be as large as the wastewater market.”
The second aspect to expansion is geographic.
“In Europe,” said Burgess, “the CIPP market is mature. We now are going to Asia and the Pacific to convert markets to CIPP rehabilitation as in Europe and the United States. We are exposing the technology with demonstrations and have been successful in Hong Kong, Singapore, India and Australia. It is very exciting.”
Expansion is occurring in non-utility markets. Insituform Technologies today is a leading worldwide provider of proprietary technologies and services for rehabilitating not only sewer and water, but energy and mining piping systems, corrosion protection of industrial pipelines and is a pioneer in trenchless technology providing affordable, long-term, less-disruptive solutions.
FOR MORE INFO:
Insituform, (800) 234-2992, www.insituform.com
Insituform Timeline
1971 Insituform is incorporated and completes first commercial CIPP installation.
1976 U.S. Patent and Trademark Office issues seminal patents to Insituform.
1980 Insituform North America is established in Memphis, TN.
1982 The first U.S. manufacturing facility opens and Insituform Mid-America is
established, later becoming the largest U.S. licensee.
1983 U.S. Environmental Protection Agency certifies CIPP as a viable method for
lining sewer pipelines.
1984 First over-the-hole wetout.
1988 Batesville,MS tube manufacturing plant opens.
1992 Insituform Technologies is formed.
1995 Insituform management system received ISO certification.
1997 Insituform Technologies moves to St. Louis, MO. Insituform enters drinking
water market.
1999 Insituform expands globally.
2003 Insituform introduces iPlus composite.
2004 iPlus Infusion introduced
2007 Insituform expands Asia-Pacific operations.
2009 Insitumain introduced
2010 WRc approves industry certification.
Comments