January 2011 Vol. 66 No. 1
Features
Robotic Tools For Video Inspections Of Live 12- 36-Inch Natural Gas Pipelines
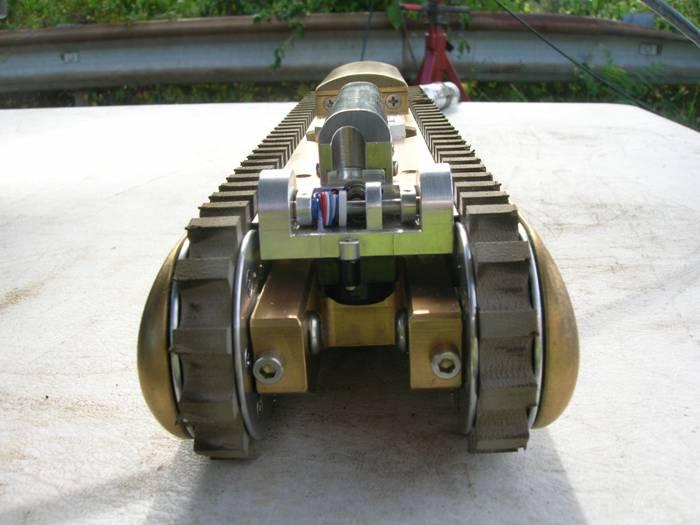
For more than 30 years, video inspection has been a fundamental analytical tool for the evaluation and assessment of pipeline integrity. Originally developed as an aid for sewer system maintenance, video inspection equipment has played a key role in the development of a variety of trenchless rehabilitation methods.
A cost-effective video inspection of gas pipelines will generate significant savings when conducted prior to pipeline repair or rehabilitation.
Pipeline rehabilitation technologies, for certain applications, typically yield significant economic savings and safety improvements for the natural gas Industry. However, benefits can quickly disappear for a project when internal obstructions or unrecorded fittings, such as valves and drip standpipes are encountered during the rehabilitation process. Most of the in-pipe trenchless technologies available today, for example, cured in place lining and modified PE slip-linings, require the pipeline to be taken out-of-service which can be costly and may interrupt service to customers. This is particularly true for large diameter pipelines 12 inches and greater that require decommissioning and purging of the pipeline. One way to mitigate internal pipeline problems prior to the project is to provide internal video inspection. Having the capability to pre-inspect the pipeline under live gas conditions assures that there will be no major obstructions or fittings that can negatively impact the project.
There is a growing need in the gas industry, in particular for companies that own and operate older large diameter pipelines, to replace or rehabilitate aging infrastructure. The ability to perform quick and reliable internal visual inspections under live-gas conditions using “no-blow” techniques (without gas escaping to the atmosphere) will provide operators with the necessary information to apply the best engineering solution. Local Distribution Companies (LDCs) are in need of internal camera inspection systems that provide high resolution video in a safe, efficient and cost effective manner.
The following describes the development of a series of Live Gas Internal Pipeline Video Inspection Systems developed by ULC Robotics and funded by NYSEARCH/NGA for their member gas companies. The inspection tools are designed to be quickly inserted through a relatively small access hole under “no-blow” operations. These quick entry systems are commercially available and can be provided as a service by ULC Robotics. Currently, ULC Robotics has three systems available for pipeline video inspection:
• Large Variable Geometry Crawler (LVGC) – live gas mains 20- to 48-inch;
• Small Variable Geometry Crawler (SVGC) – 12- to 16-inch; and
• Pipeline Periscope – pipelines 12 inches and greater.
The video inspection systems developed by NYSEARCH/ULC Robotics are designed for rapid deployment, high reliability, low cost and have the ability to provide detailed video data. Gas distribution companies will be better able to react quickly to emergency and maintenance issues by locating internal pipeline problems such as cracks, pipe damages, abnormalities, unknown branches, service tees, valves, fittings and water intrusion. These newly developed inspection systems can become an invaluable tool for pipeline rehabilitation projects by providing critical information for assessing pipeline cleanliness, corrosion activity and structural integrity. The availability of this data assists pipeline operators in the planning stages and as a result can produce significant cost savings. The use of these video inspection tools, prior to a major project, will allow engineers/operators to make cost effective decisions when selecting repair/replace options.
Summary of benefits:
• Live Inspection of 12- to 48-inch Pipelines;
• Fast Deployment;Entry Through Small Hole;
• Use Standard No-Blow Equipment;
• Navigate Bends and Offsets;
• High Resolution Video Imaging & Recording;
• Maintenance Planning;
• Rehabilitation Method Selection; and
• Emergency Response;
Large VGC
The Large VGC is a crawler system designed for 20- to 48-inch live gas mains operating up to 100 psig. The crawler is launched through a 4-inch taphole drilled into the main using standard no-blow hot tap technology. After the inspection, a standard completion plug is installed.
No-blow technology assures that no natural gas escapes from the system as the tapping, entry, inspection, and exit of the equipment takes place. This allows the operators to work in a safe non-gaseous atmosphere. The crawler has an expanding track system which allows it to travel over debris and some obstacles that are commonly found in steel and cast iron pipelines. The crawler is equipped with a pan and tilt camera for high resolution internal inspection and it is tethered to a control system. The combination of these components allows for precise video inspection for a variety of applications. The system is designed to travel up to 500 feet in each direction from the entry point and is capable of navigating through a limited number of pipe bends and branch tees.
Small VGC
Based upon success of the Large VGC, a smaller version of the crawler was developed for inspection of 12- to 16-inch pipelines. The design required the small version robot to enter the pipeline through a 3-inch taphole. This would allow the robot to enter pipe as small as 12-inch without the need of pipe reinforcement fitting. Small VGC works with the existing launch system and controls, and is interchangeable with the larger VGC robot which lower costs by permitting one support system to function with both tools.
Small VGC provides inspections of live gas mains under no blow conditions via a taphole drilled using standard hot-tap equipment. Unlike its larger cousin, the new 12- 16-inch robot does not have expanding tracks. Its compact design cannot accommodate the parts and components needed for the expanding strut system. Instead, a fixed track design was developed to allow sufficient clearance to maneuver over pipe debris and around many obstacles. All motors that drive the tracks are inboard and allow for enough clearance to climb up pipe bends, as steep as 45 degrees.
Inspection results
ULC Robotics successfully completed video inspection services for several major gas companies in the Northeast (Con Edison, National Grid, PSE&G and PECO). Inspections performed by Large and Small VGC on 12-, 16- and 20-inch cast iron and steel pipelines achieved travel distances up to 500 feet in a single direction. This provided companies with critical pipeline information prior to any repair/rehab work being performed. Repair/rehab work being considered included internal joint sealing using Cast Iron Joint Sealing Robot (CISBOT) technology and Cured-in-Place lining. For example, recently ULC Robotics performed an emergency internal video inspection of a leaking 16-inch diameter cast iron main for Con Edison located at the foot of the Brooklyn Bridge in Manhattan. The Small VGC was used to pre-inspect the leaking pipeline prior to the rehabilitation. This provided Con Edison and the contractor with critical information during the planning stage. Shown nearby are two pipeline problems uncovered by video inspection that enabled pipeline operators to make the appropriate repairs.
Pipeline periscope
Pipeline Periscope is a high-resolution video inspection tool for use in live 12- to 48-inch low and medium pressure mains. It is designed for quick and easy access and permits a visual inspection of up to 200 feet from a single taphole (100 feet in each direction). The no-blow operation allows direct mounting of Periscope’s access tube to a gate valve. A control system is attached to the Periscope via cable that allows remote camera and lighting control. The camera has pan, tilt, and zoom capability and provides high-resolution video imaging of a one inch object 100 feet from the entry point. The Periscope device enters the pipe through the 4-inch diameter taphole drilled with standard tapping equipment. After the inspection a standard completion plug is installed. No special fittings are needed during the process.
Conclusion
The gas company members of NYSEARCH/NGA have identified and funded an important gas industry need. Large VGC, Small VGC and Pipeline Periscope provide the industry with a complete set of tools for obtaining high resolution video inspection for large diameter pipelines. Pipelines operators now have the ability to obtain reliable video inspection of their larger diameter pipelines during the pipeline rehabilitation planning stage. These video inspection systems have been laboratory and field proven to provide high resolution footage for low and high pressure pipelines up to 100 psig. They are designed to perform under no-blow live gas conditions (no gas being emitted to the atmosphere) and equipped to provide control monitoring, data recording, user manuals and operating procedures. All three video inspection systems are commercially available for sales or service through ULC Robotics.
NYSEARCH is a non-profit voluntary R&D organization serving 20 gas LDCs in North America that fund new technology development on a voluntary basis. Additional details are provided on NYSEARCH’s website www.nysearch.org. Commercial literature and actual video displays can be found on the ULC Robotics website http://www.ulcrobotics.com.
Comments