November 2011, Vol. 66 No. 11
Features
Jack & Bore Method Installs Utilities At Ohio State Medical Center
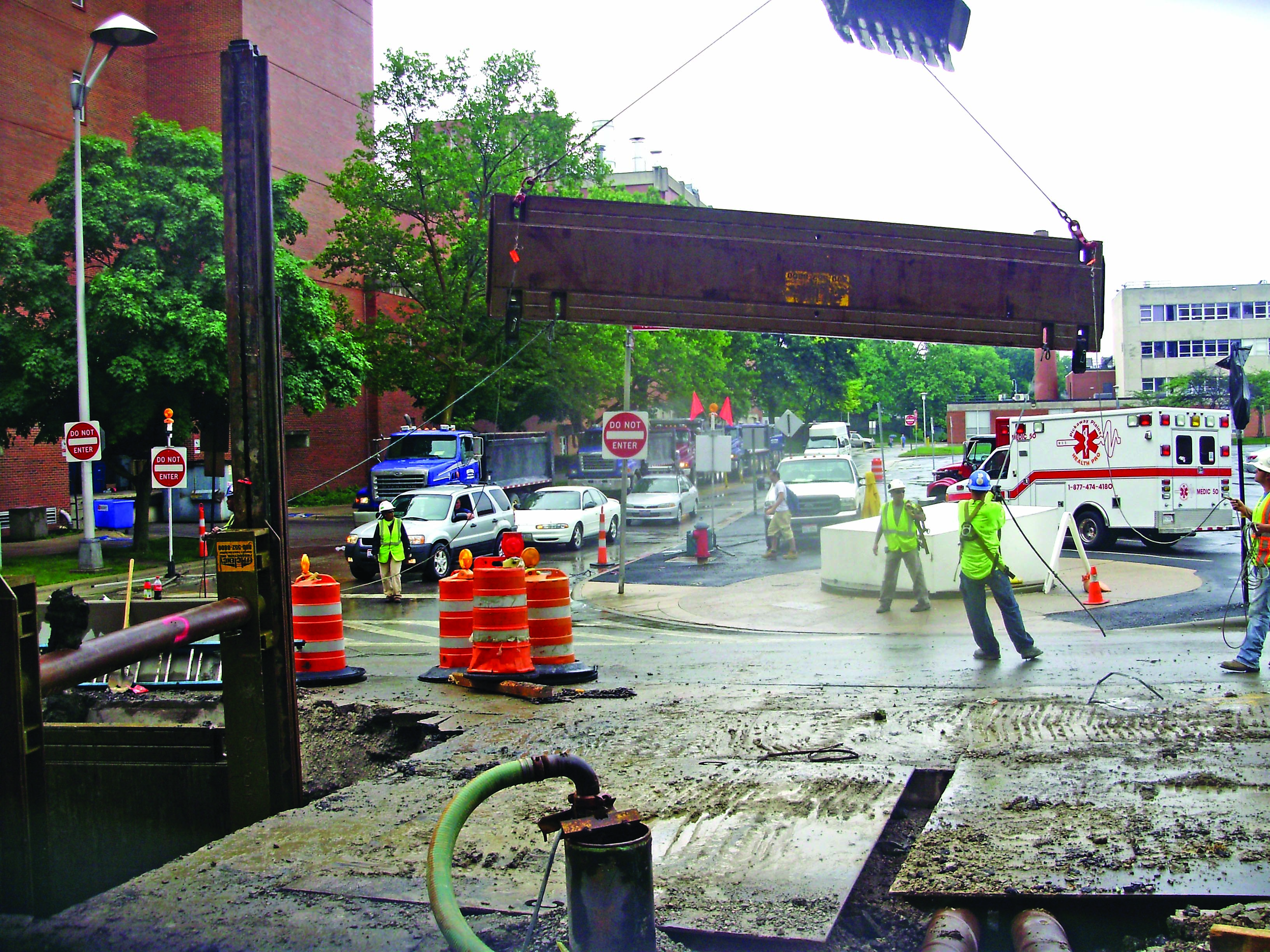
Proactive safety — that is Columbus, OH-based McDaniel’s Construction Corp.’s standard operating procedure whenever they have personnel working in a deep trench or pit. Such was the case when McDaniel’s recently installed 1,300 linear feet of conduit casing for electrical, communications and other utilities at the Ohio State University Medical Center (OSUMC) in Columbus, OH.
For a typical excavation project, McDaniel’s would open-cut to install the underground utility. But the OSUMC project was hardly typical. The utility casing needed to be installed in some very tight spots, practically right up against the Center’s buildings, and in spots as deep as 32 feet.
McDaniel’s planned out a series of jack and bore pits to push 24 and 36-inch casing below the many surface obstructions, and in some places even under other existing underground utilities. But as advantageous as jack and bore was for the project, it posed one great challenge: shoring the pits in several locations and provide fall protection.
“Normally, we’d just use enclosures made with trench shields where we couldn’t open cut,” said Steve Betsko, McDaniel’s project superintendent. “But at a certain depth, trench boxes can become unsafe for our personnel.”
McDaniel’s turned to the Efficiency Production Inc.’s Slide Rail System to address their needs.
Efficiency’s Universal Slide Rail is a component shoring system comprised of steel panels (similar to trench shield sidewalls) and vertical steel posts. The highly versatile system can be used in a variety of configurations. In addition to the obstruction-free ClearSpan configuration, Efficiency’s Universal Slide Rail can be configured into small four-sided pits; or in a multi-bay configuration to install large tanks and structures or lengths of pipe over 40 feet.
As the name suggests, the panels slide into integrated rails on the posts. Both the panels and posts are pushed incrementally down to grade as the pit is dug; a process commonly referred to as a “dig and push” shoring system. Slide Rail is considered “active shoring” which means that personnel and equipment can be safely in the hole throughout the entire installation and removal process.
The Slide Rail System’s individual component pieces can be handled with a midsize excavator which means that excavation contractors can usually install the shoring system themselves. McDaniel’s used a CAT 345 excavator to install the system.
“In total, we excavated and shored five bore pits; two doubles and one single,” explained Betsko. “All the parts are reusable over and over again, which saves time and money”
McDaniel’s rented a two-bay, four-sided multi-bay configuration which provides a larger unobstructed area for installing tanks, vaults, and other structures; or in this case, a bore jack rig. McDaniel’s system was 12-feet wide, 41-feet long and 24-feet deep.
“The ground conditions were trash, and we needed to dewater each pit,” said Betsko, but McDaniel’s was able to install the system in just two days, and have it out again in only one day. Mostly, the jack and bore pits were right up against the buildings and other structures at the medical center.
FOR MORE INFO:
McDaniel’s Construction Corp., (614) 252-5852, www.mcdanielsconstruction.com
Efficiency Productions Inc., 800-552-8800, www.efficiencyproduction.com
Comments