October 2011, Vol. 66 No. 10
Features
CIPP Best Practices
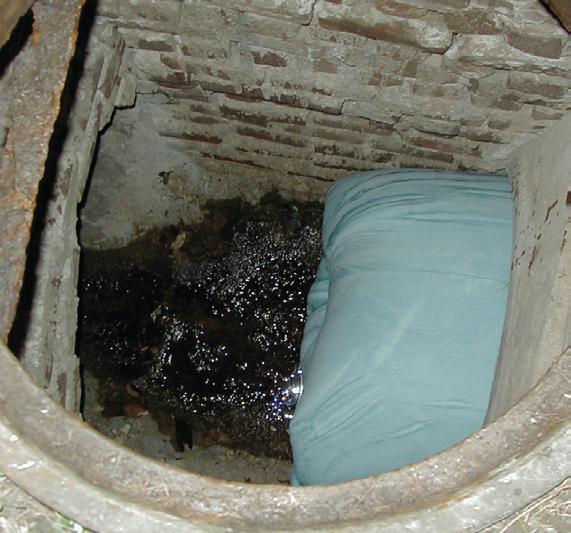
There are four key elements to having a really good Cured-in-Place Pipe (CIPP) installation:
1. Proper saturation of the tube;
2. Proper inflation of the resin saturated tube in the host pipe;
3. A full and thorough curing of the resin system used; and
4. A proper cool-down of the CIPP.
Proper Saturation
Whether the CIPP’s tube consists of only polyester felt fiber material, is a hybrid of polyester fibers and glass fibers, or is the product of only glass fibers, proper saturation with the resin system is key to a water-tight, structural performance of the CIPP throughout its intended service life.
The most commonly employed method for the resin saturation process is serial vacuum with calibration rollers. Looking at a felt fiber tube it is hard for most to fathom that approximately 90% of its volume is simply empty or void space. What this means to the wet-out technician is that the void space or pathways for the resin to fill are very small, and the only real way of coaxing the resin into them successfully is by the use of a negative pressure, or vacuum.
The level of the vacuum at the tube varies somewhat with the thickness and type of fiber matrix used. The air must be evacuated from the tube to make room for the resin. When adding resin to the tube, the technician must be careful not to add air back into the tube. Once the required amount of resin is in the tube the tube can be transported through the calibration rollers at a speed consistent with the resin’s migration into the fiber matrix.
Proper Inflation
The current state of the art for CIPP installation is to either invert the resin saturated tube into the host pipe using a column of water or pressurized air or to pull the tube into position followed by the inversion of a polymeric membrane or simply inflating the tube with air.
When the installation is made using a column of water for the inversion process it is key that the advancing nose of the inverting tube sees a pressure equal to or greater than the tube manufacturer’s stated “minimum inversion head”. The minimum inversion head provides for the proper full expansion of the tube and tight contact with the host pipe.
When the nose sees less than the minimum head longitudinal finning in the bottom half of the CIPP is almost a sure thing. Raising the head after inversion can only stretch the portion of the tube’s circumference that is not already in contact with the host pipe, creating a thin area in the crown of the CIPP. Also, if there is active infiltration observed in the host pipe an additional head equal to the level of the groundwater above the flowline of the host pipe must be added to the minimum inversion head.
Curing of the resin system
Resins used in CIPP are either heat cured or UVlight cured. With heat curing methods the water or the air is heated to a level that ramps up the speed of the polymerization process to effect hardening of the resin system. Minimum temperatures that must be seen at the interface of the CIPP with the host pipe established by the resin system manufacturer must be measured at as many points as are practical to insure that sufficient heat is being transferred throughout the liner’s wall section.
For hot water curing it is important to recognize that “heat rises”; for pipes larger than 18-inches in diameter, the water discharge tubing must be weighted to adequately heat the bottom of the CIPP. For CIPP cured by hot air (air with steam), condensate removal is imperative to avoid isolating the bottom of the CIPP from proper heating. Initial (or visual) hardening indicates that the curing has reached only the 80% cured level and complete curing requires the heating process be continued for the resin manufacturer’s minimum amount of time beyond the initial curing to insure complete curing.
As with heat curing, UV-light initiated resin systems must be exposed to the lighting for the minimum time required to fully cure; short changing the exposure time will result in an under-cured CIPP. Given the thinner cross-sections and the dependence on bringing the glass fibers into play makes obtaining a complete cure a top priority. Complete curing, whether by heat or UV-light, gives the CIPP its chemical resistance and structural properties.
Cool-down
Once curing is completed, the hardened CIPP must be brought down to a temperature where it is dimensionally stable. If the internal pressure is taken away before the CIPP has cooled down, the uncontrolled cool down can lead to an excessive gap between the CIPP and the host pipe. This shrinkage occurs with all the resin systems currently used for CIPP; polyester, vinyl ester, and epoxy.
By properly cooling down the CIPP, which includes removing the excess heat remaining in the ground as a result of the curing process, the tube will stay generally tight to the host pipe and any chemical shrinkage will be outward towards the host pipe wall. For more information, visit www.nassco.org
Comments