October 2011, Vol. 66 No. 10
Features
Keep The Bore Path On The Straight And Narrow
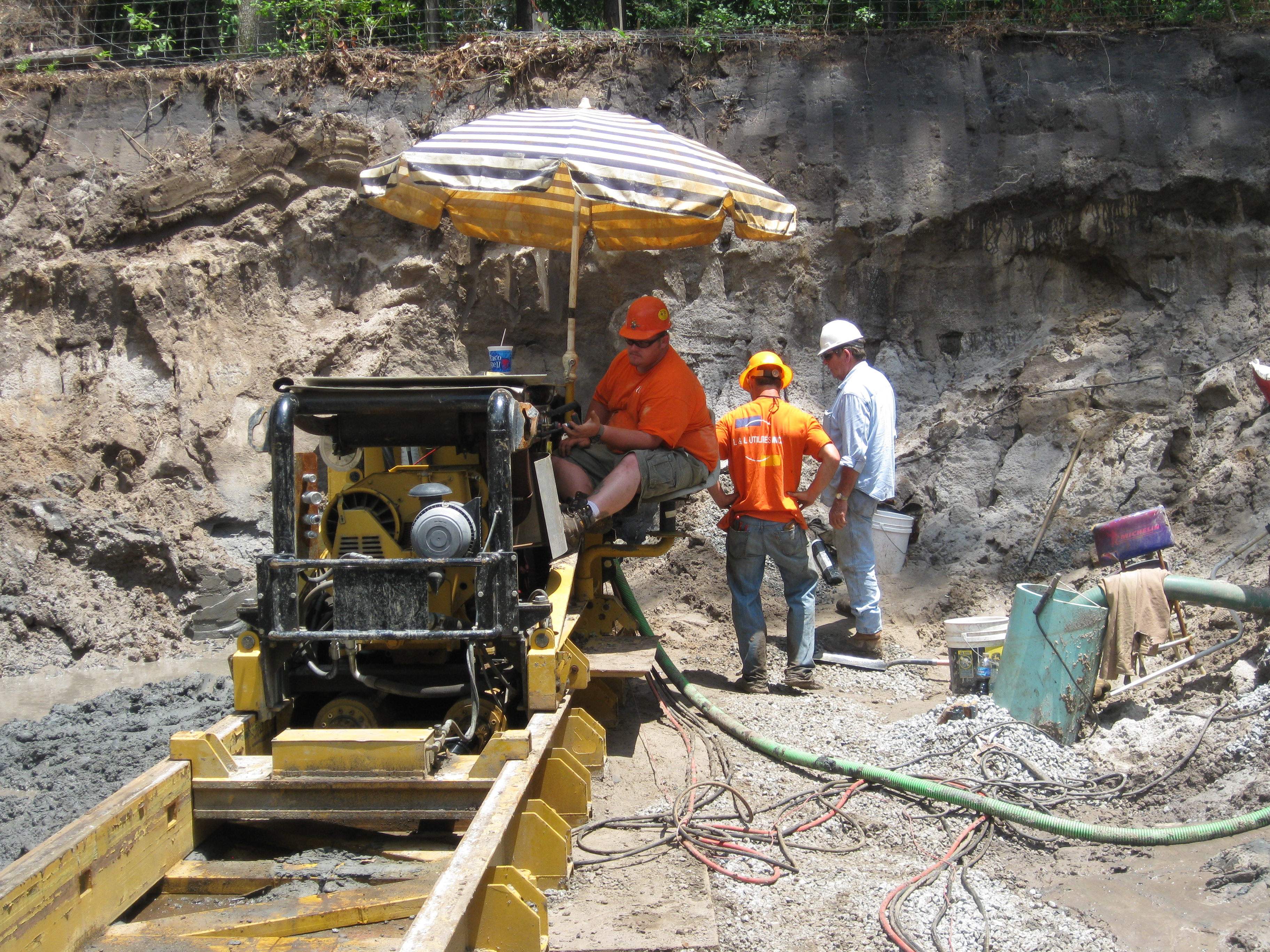
Kirk Lewis knows a thing or two about horizontal auger boring. Lewis, vice president and co-founder of L&L Utilities, based in East Dublin, GA, was first exposed to this century-old trenchless installation method at a young age while working with his father at their family-owned contracting business.
In 1995, he and his wife were able to fulfill a longtime dream of owning their own business. The company specializes in water, sewer, gas and wastewater installations, and has used auger boring successfully to complete hundreds of utility installations.
Although Lewis admits to being an avid proponent of auger boring, his years of experience have also made him aware that, as with any trenchless approach, auger boring is not without its limitations.
“Auger boring is an efficient, cost-effective method that fills an important niche in the trenchless industry,” Lewis says. “It was initially developed to complete shorter bores to accommodate larger material. Auger boring is ideal for situations like installing pipe casing under railroads, highways and creeks; bores that are typically shorter in length, most generally less than 300 feet. But attempting a bore that extends beyond the recommended capabilities of the equipment will likely present challenges.”
Physics of “drifting”
One of the most common challenges facing contractors when attempting a bore in excess of 300 feet is a situation that is actually a principle of physics — often referred to in trenchless circles as drifting — which, in lay terms, is the resistance to force. Specific to auger boring, drifting is the tendency to veer off the desired course of the cutting path, a reaction that is linked to the basic operational design of auger boring machines. According to Mike Moore, vice president of sales for McLaughlin, based in Greenville, SC, the incidence of drifting is exacerbated by the inability of auger boring equipment operators to control the lateral (left to right) movement of the machine’s steering head.
“In the past, adjustments to the steering head of auger boring equipment could only be corrected for grade (up and down) directional changes during the bore,” Moore says. “The inability to control the lateral (left and right) movement during the boring process has prevented operators from making adjustments that are often necessary to accommodate for drifting. This is especially important on longer bores where there is a natural tendency for the head to deviate left or right in response to increasing the resistance.”
Alignment, grade critical
The ON Target system from McLaughlin allows contractors to adjust the lateral direction of the steering head along with the vertical movement. The ability to make lateral corrections allows operators to make adjustments in any direction: up and down, left and right, resulting in more accurate cutting paths, something that is especially useful for longer, more difficult on-grade bores.
As Moore explains, the grade and lateral movement of the ON Target steering head is controlled by hydraulic actuated panels that open and close to keep the head on the intended course. A control station features a hydraulic power pack to control the movement of the steering head, and a built-in water level helps monitor grade throughout the bore. Two halogen lights in the control station indicate lateral steering head alignment.
“This is a significant upgrade from the traditional manual knuckle that has been the industry standard,” Moore says. “When this knuckle was exposed to challenging soil conditions there was a tendency for the steering head to resist, resulting in inadvertent downward movement away from the desired path. By using a hydraulic control system, we’ve been able to remove that unknown movement factor from the bore.”
Putting ON Target to the test
Lewis put McLaughlin’s ON Target steering to the test on a recent water line expansion project just outside of Savannah, GA. The task was to install a 36-inch casing for a 24-inch water main (configured in 40-foot segments) beneath two interstate highways at the northeast corner of the I-95 and I-16 interchange. The challenges were several, including the length of the two bores (400 feet and 440 feet respectively), the soil conditions (unpredictable variations of sand and gumbo) and lastly, the depth required to complete the bores.
The two installations were among 30 bores that L&L Utilities was subcontracted to complete for an 80,000-foot water line expansion project by the project’s general contractor, Lee Contracting, based in Heartyville, SC. After reviewing the project details and analyzing the soil profiles, Lewis knew they would be facing some difficult challenges.
“There was a combination of issues that were concerning as we planned how to best approach the project,” Lewis says. “We knew the boring lengths would push the tolerances of the auger boring approach somewhat, an issue further complicated by the depth that would be required to comply with DOT cover specifications. If that wasn’t enough, there was the sand/gumbo soil profile mix; something we knew would be difficult to predict and correct as we got further along in the progression of each bore.”
Lewis was confident that auger boring was the right method but was also concerned about the incidence of drifting, given the length and depth of the bores. He chose the McLaughlin 42HD auger boring machine, with 42-inch boring capacity. What he didn’t expect was an additional tool he would put to the test after discussing the project with McLaughlin.
“I was expressing some of my concerns to our contacts at McLaughlin and they felt the ON Target steering head would be a great tool for minimizing any drifting issues,” Lewis says. “After discussing it further and learning more about the capabilities of the system, I was more than willing to give it a try.”
Digging deeper
The Georgia Department of Transportation (DOT) requirement dictating six feet of cover forced Lewis to dig the launch pit at 18 feet. The ground conditions at the pit locations were good, so Lewis’ crew only needed to add gravel in the launch pit along with steel plates to solidify the base. A big concern at that depth is the ability to maintain the alignment and grade of the cutting path, not to mention the alternating sand and gumbo mix. Boring through sand requires dewatering, while boring through gumbo requires the presence of fluid to facilitate the spoil removal.
“Boring through a gumbo and sand mix can be tricky because gumbo balls up and free-flowing sand can create voids,” Lewis explains. “We had to be careful to adjust the speed of the bore as the steering head moved from sand to gumbo and back to sand. To further complicate matters, there were several instances where we were boring through a sand/gumbo mix. This made adjusting the boring speed critical.”
After installing each 40-foot section of casing, the crew checked grade using the built-in water level and left/right alignment using the halogen light system. If necessary, adjustments would be made by opening or closing the hydraulic actuated panels of the steering head before installing the next casing segment. In the end, both bores were completed successfully. With the casings firmly secured, Lewis took a moment to reflect on all of those pre-bore concerns.
“We completed both bores well within tolerance which I consider a great accomplishment given the extremely difficult soil conditions and the length and depth of the bores,” he says. “We have a great crew and I had a lot of confidence in their instincts and experience to react and adjust the bore based on the tricky conditions. But I am also very pleased with the performance of the ON Target system.
“The ability to make corrections to both the vertical and lateral coordinates of the equipment is a huge benefit,” Lewis added. “Knowing that we could control some of the drifting issues gives contractors more confidence when tackling bores in excess of 400 feet. It was a very helpful piece of equipment to use.”
FOR MORE INFO:
McLaughlin Group, (800) 435-9340, www.mightymole.com
L&L Utilities, 478-278-3554
Comments