October 2011, Vol. 66 No. 10
Features
Modern HDD Tech Finally Brings Gas To Branson
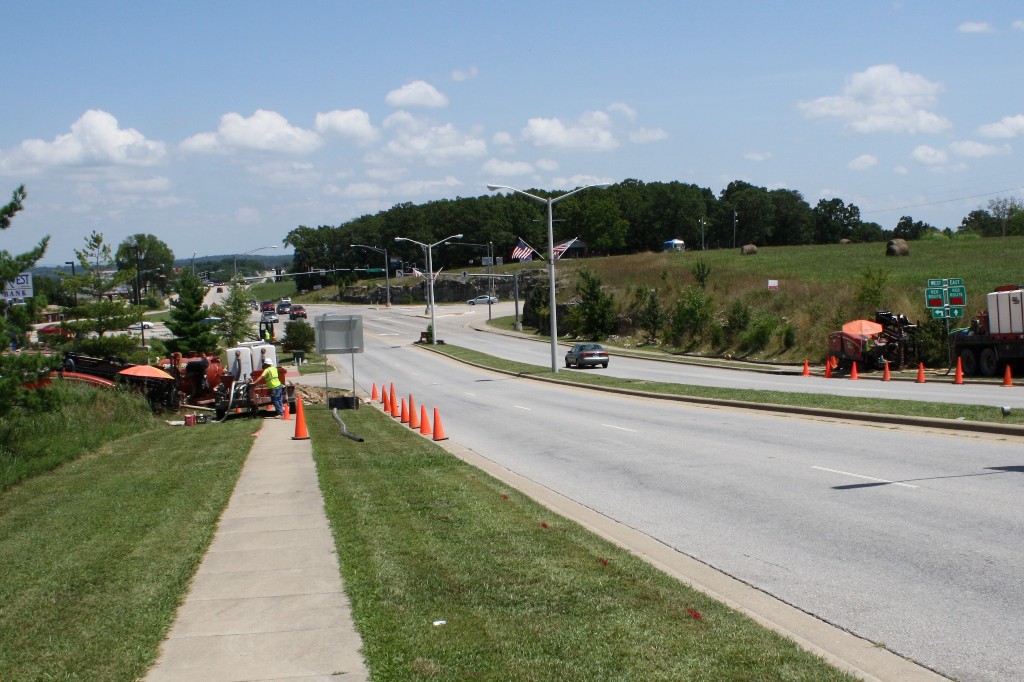
Branson is a popular Southwestern Missouri family vacation center, home to Silver Dollar City, hotels, fine restaurants, more than 50 live performance centers, a dozen championship golf courses and a host of other attractions. Yet city homes and businesses are just now being connected to natural gas.
A 48-mile-long, eight-inch diameter steel gas transmission line was completed last year through the rugged Ozark Mountains to bring gas from Aurora to Branson, and then crews constructed a distribution system within the city to bring gas service to customers.
The gas service provider is Southern Missouri Gas. Summit Utilities Management Services LLC, Littleton, CO, managed construction for both the transmission line and distribution system within the city.
Gas has been a long time coming to the Branson area, and a major reason is that rocky soils in the area make putting gas pipe in the ground extremely difficult and costly.
Bret Brown, Summit business development and construction manager, said the transmission line route contained the hardest rock he has ever encountered.
“Not only was the rock extremely hard,” he said, “but changes in elevation of the terrain, steep side slopes and drop-offs made construction difficult. We’ve done pipe projects in the Rocky Mountains, but this one was more difficult.”
The same hard rock is just beneath the surface of most of Branson.
Barrier to entry
Over the years, said Brown, several companies have held franchises to provide gas to the area, but they all dropped plans because the terrain and rock made construction too costly for the potential of a relatively small customer base. Beginning June 2010, crews of multiple subcontractors have been in Branson burying gas mains and service lines. Brown said most of the main-line work was completed in December 2010. Service work continues as customers are added. He added that the Branson gas distribution system to service approximately 1,000 customers comprises about 80 miles of mains consisting of 2-, 4- and 6-inch pipe, all HDPE pipe. Services will include another approximately 15,000 feet of pipe in 3/4-, 1 1/4-, 2- and 4-inch diameters.
Approximately 85 percent of construction of the distribution system has been completed by horizontal directional drilling (HDD), said Brown. Most services also are put in the ground by HDD.
One of the primary subcontractors for gas distribution construction in Branson was Woods Construction Inc., based in Colorado Springs, CO.
The company’s work in Branson focused on installation of gas mains and service lines with about 85 percent of the pipe installed by HDD, said Ed Libby, Woods Construction president and site supervisor for the work in Branson.
“We did do some open-cut work with trenchers and a small rock saw, but this project never could have been successfully completed without the capabilities of directional drilling,” said Libby.
“Most of the construction was in developed areas. To dig and hammer rock to put pipe in the ground would have made the cost too great,” Libby explained. “This was a project for which HDD was the least expensive way to perform the task.”
Woods Construction crews installed more than 100,000 feet of HDPE main line pipe in a mix of 2-, 4- and 6-inches. Most services were ¾-, 1¼- and 2-inches. Three hundred bores were made, ranging in length from 80 to approximately 1,320 feet. The average bore was 330 feet.
Rock sets job apart
Rock is what set the work apart from projects in ‘normal’ conditions, said Libby. Otherwise, it was a typical job.
“But the rock was extremely hard,” he stressed. “In some areas it was on a hardness scale of 31,000 psi. We did test breaks at various locations in the project and more than half the rock was more than 20,000 pounds psi.”
For all HDD work, Woods crews used two Ditch Witch JT3020 All Terrain (AT) drill units and one JT4020 AT machine. Equipped with a dual-pipe mechanical drive system, the AT system permits relatively compact drill models to effectively drill in rock as well as dirt and clay.
Libby said the AT machines completed all bores making it unnecessary to use machines with mud motors to drill through the rock.
“Using larger equipment with mud motors and the support equipment necessary would have been economically unfeasible,” said Libby. “Cost of the drilling fluid alone would have been 10 times more.”
The dual-pipe drilling system enables relatively compact equipment to drill through rock without a mud motor. The mechanical dual-pipe system delivers maximum downhole horsepower and operates on low volumes of drilling fluid. The AT design employs an inner rod to drive a rock bit, and the outer pipe steers the downhole tool for drilling pilot holes and provides rotary torque for the hole opener during backreaming.
The Ditch Witch JT3020 is a relatively compact, self-contained unit mounted on rubber tracks that enable it to move across both paved surfaces and grassy terrain with minimal surface disturbance. It develops 30,000 pounds of pullback, 4,000 foot pounds of spindle torque and maximum spindle speed of 225 rpm. Pilot holes were drilled with Ditch Witch carbon tri-cone bits with Ditch Witch backreamers set up in 8- and 12-inch diameters.
Ditch Witch fluid mixers and other support accessories were used with the three drill units.
The larger, more powerful JT4020 AT has 40,000 pounds of pullback, 5,000 foot pounds spindle torque and spindle speeds to 250 rpm. It was used for the longer bores.
Slow but steady
Drilling in hard rock obviously is slower than working in dirt or clay. “Our goal going in was to achieve a shot a day with the two JT3020s and one every two days with the JT4020, and on most days we were able to meet those goals,” Libby said. “Production would have been double that in good conditions.”
Tracking for both machines was done with a Ditch Witch 8500 tracker.
“In addition,” said Libby, “we used three Ditch Witch FX30 vacuum excavators for potholing and clean up of drilling fluids, and a small 3700 Ditch Witch rock saw in Branson.”
Libby said in addition to distribution construction in the city of Branson, Woods completed about 3,000 feet of transmission lines on the project.
Established in 1996 by Ed Libby and Maurice Woods Jr., Woods Construction is a full service utility construction company providing underground and overhead installation services in gas and electric transmission, gas and electric distribution, telecommunications, water and wastewater systems.
In addition to the home office in Colorado Springs, there are yard locations in Cripple Creek, CO, and Branson, MO.
Ridenhour Construction, Jefferson City, MO, installed approximately 70,000 feet of 2-, 4- and 6-inch HDPE mains in Branson.
“We’re not far away from Branson, and we know the area well,” said President Joe Ridenhour. “So we were well aware of the conditions and that the rock is very hard.”
Ridenhour said two Ditch Witch JT3020 AT units were purchased specifically for working in Branson. Ridenhour crews made approximately 350 bores ranging in length from 50 to 500 feet.
Proving ground
“I’d say if a machine can drill in Branson, MO, it can drill anywhere.” said Ridenhour.
Ditch Witch roller cone bits were used to drill pilot holes. Pilot holes were guided with Ditch Witch 752 tracking equipment. A variety of backreamers were used. Ditch Witch FX30 vacuum excavator equipment was used to clean up drilling fluids.
“The hardness of the rock slowed production,” Ridenhour continued, “but we averaged about 200 feet per day per machine and completed our portion of the project without a lot of problems. Pipe routes went through both residential and commercial areas, but HDD limits surface damage and minimizes disruption of traffic and normal activities. The public was pleased to be getting gas service and accepted our presence.”
Ridenhour has been in the underground utility construction business for 19 years. The company began operations by conducting both underground and overhead work, but today it specializes in underground projects. In addition to gas, projects include communications and power construction.
“We still plow in a lot of innerduct, but don’t operate trenchers anymore,” Ridenhour said. “If we need to open a hole we use a backhoe or excavator. Some projects require aerial work and we still have that capability, but our focus is on underground.”
Summit’s Brown said work soon will begin to bring gas service to Hollister, just south of Branson.
Summit Utilities Management Services specializes in constructing natural gas distribution systems to provide natural gas to residential and commercial customers.
Southern Missouri Natural Gas, Mountain Grove, MO, owns and operates over 400 miles of natural gas pipelines and is expanding its system to serve the communities of Houston, Branson, Hollister, Mountain Grove, Lebanon, West Plains and other small towns.
FOR MORE INFO:
Ditch Witch, (800) 654-6481, www.ditchwitch.com
Ridenhour Construction, (573) 761-1630, http://ridenhourconstruction.net/
Woods Construction Company, (719) 213-2098, www.woodsconstructionco.com
Summit Utilities, (800) 720-8193, www.summitutilitiesinc.com
Comments