August 2012, Vol. 67 No. 8
Features
Rock Mass Properties and Their Potential Impacts on Trenchless Projects
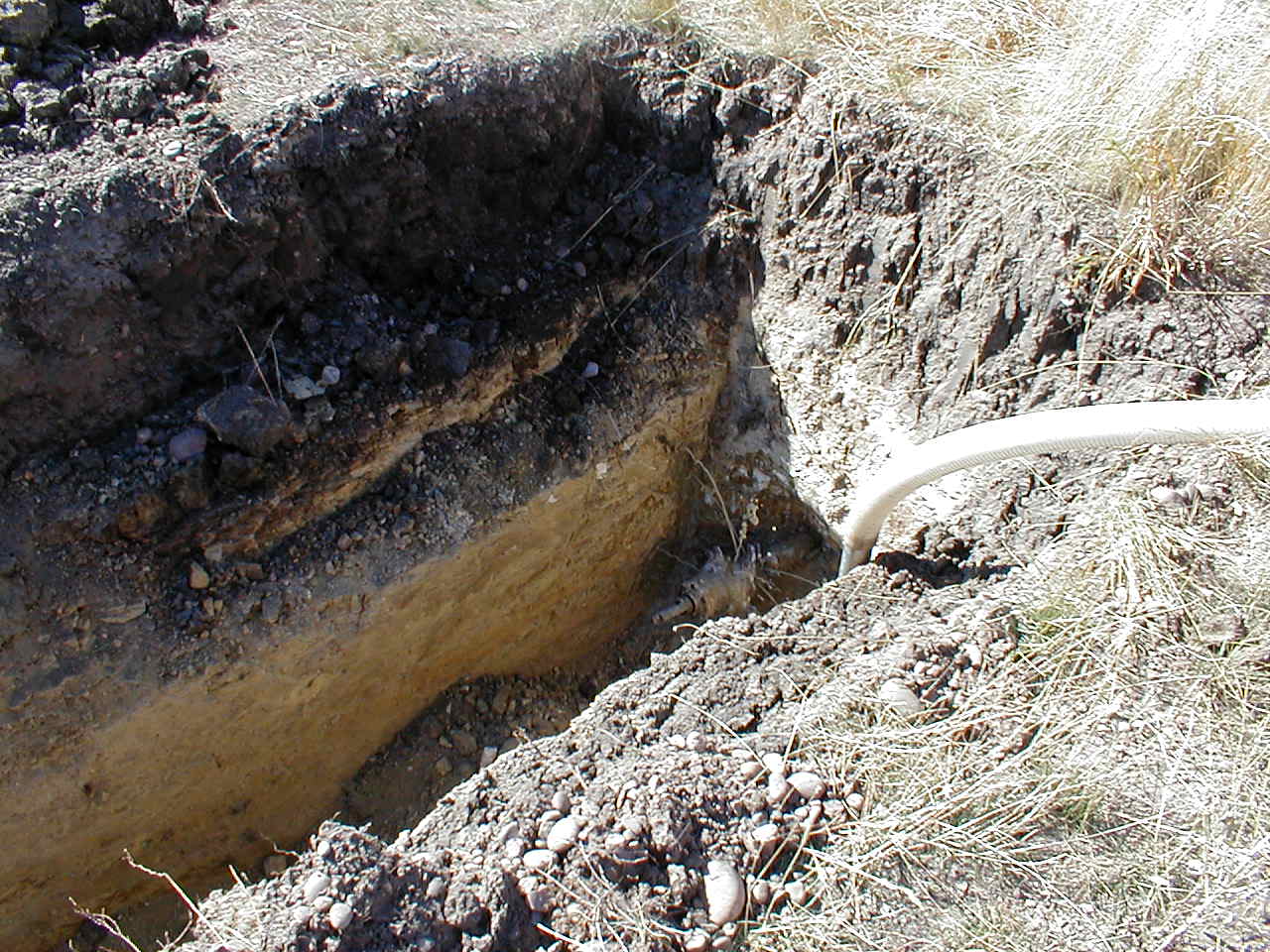
Rock mass properties will almost always have a profound influence on the excavatability of any feature to be constructed in bedrock.
In-situ earth material properties can affect the economic viability, construction schedule and overall feasibility of virtually any project, including excavations for civil, mining, petroleum and energy projects. Rock mass properties and even more importantly, their variability, must be reliably understood before undertaking efforts in project design and preparation of contract documents.
In this regard, the geotechnical challenges associated with the relatively new field of trenchless technology are not unique; rock mass properties will impact the constructability of virtually all trenchless projects that are constructed within bedrock. Similarly to drilling petroleum or water wells, blast holes or deep exploration holes, horizontal directional drilling (HDD) projects will be impacted by drill hole wander, due in-part to rock mass properties. Likewise, utility tunneling, auger boring and microtunneling projects will be affected by rock mass properties, for example, by influencing cutting efficiency at the advancing face and by differences between the design and actual jacking (thrust) force requirements. An initial understanding of rock mass properties, and their potential impacts on project design and construction, can help to significantly reduce the chances for differing site conditions claims and change orders, and can reduce the likelihood of painful schedule delays.
Soils vs. rock analysis
In most cases, geotechnical analyses applied to soils is not appropriate for analysis of rock, as the latter is frequently (but not always) analyzed using a discontiuum approach depending on the scale of the project with respect to prevailing rock mass properties. Soils engineering frequently adopts a continuum approach to analyses, based on an assumption of uniformity with in-situ material properties. Scale-dependencies may impart some level of control on whether a continuum or discontinuum approach is more appropriate. For example, in cases where an excavation diameter is less than anticipated rock block size as defined by discontinuity (e.g. joints, fractures) intersections, a continuum approach may be more appropriate for the specific situation. For projects locations consisting of jointed bedrock with relatively high intact rock strength, often the most important factor that controls behavior are the geologic structures within the rock mass. General rock mass type failures are also possible in bedrock conditions comprised of numerous joint sets and/or weathered rock, whereby failure occurs not only along discontinuities but also through intact rock that is in a weakened state due to the weathering process.
The phrase “intact rock properties” refer to a continuum of rock where flaws or discontinuities do not significantly impact the mechanical properties of the rock. In this regard, intact rock properties, if utilized as the sole basis for geotechnical design, would be operating under assumptions based on continuum approach. The phrase “rock mass properties” refers to the intact rock properties in addition to all of its flaws (e.g. joints), and is generally discontinuous in character. Intact rock properties can be markedly different from rock mass properties; using intact rock properties as the sole basis for design may result in a non-conservative assessment (i.e., over-statement) of in-situ material strengths. Actual rock mass strength parameters may be significantly lower than those derived primarily from intact material properties, and trenchless designers are advised to be clear on this distinction.
In the case of tunneling-type operations, trenchless projects could encounter the following geotechnical challenges associated with adverse rock mass conditions:
- Ground failures – In the case of larger diameter underground excavations, structurally-controlled rock block stability could result in crown (roof) failures, sidewall failures or even block instability at the advancing face. This becomes even more of a potential issue when shielding at a minimum, particularly in cases of larger-diameter machine-aided and drill and blast tunnels;
- Under-designed jacking force – In cases where a thrust force is required for advancement of the trenchless feature, unstable ground conditions like roof falls or cave-ins may bear-down on the microtunneling frame and result in underestimation of required jacking force(s); and
- Failure of jacking pit, access/jacking shafts or reaction block bearing – Structurally-controlled failures in bedrock may also impact ancillary open-cut excavations, vertical jacking shafts or dedicated reactionary blocks. In addition to the effects from a temporary loss of excavation support and potential influx of water, reaction loads from the jacking operation may need to be considered for further evaluation depending on the orientation and spacing of the prevailing discontinuities.
Geotechnical challenges
For trenchless methods that rely on drilling mechanics as the primary means of advancement, the following geotechnical challenges must be anticipated in rock masses with structurally-controlled behavior:
- Near-field drill hole deviation – Also sometimes referred to as drill hole “wander” or “deflection.” Drilling involves cutting or comminution of the rock, followed closely-behind by placement or installation of a linear product like drill casing or plastic pipe, for example. As the length of the drill string or product pipe increases in down-hole length, there is a corresponding reduction in the flexural rigidity of the linear member, which in-turn imparts a bearing force directly on the geologic material that forms the outside diameter of the drill hole. If the material is rock, then the rock needs to be able to impart an equal and opposite force back on the pipe in order to resist bending. In cases where a weak rock mass is present or where discontinuities in the rock are persistent, open and frequent, “unanticipated” drill hole deviation may result. For smaller diameter bores as may be the case with many HDD projects, open joints and seams in the bedrock could result in a preferred path of least resistance for the drill string, potentially resulting in excessive drill steel deflection along the drill path.
- Hydraulic continuity problems – If persistent and open discontinuities intersect the proposed bore path, then the possibility of a “frac-out” along a discrete joint plane cannot be ruled-out. A frac-out has implications for both the drilling operation and the surrounding environment. There can be potential permit violations and water quality impacts, in addition to the loss of a critical lubrication and cutting transport agent. If anticipated, drilling fluids can be conditioned or in more extreme cases, ground pre-treatment via pressure grouting could also be undertaken.
- Geostatic stress state – Understanding in-situ stress state at depth can be helpful in determining the required drilling fluid pressure and drill mud properties that are needed to ensure a stable hole, and to minimize chances of frac-out. In cases of overburden soils, geostatic stress at depth may be estimated by simply multiplying soil unit weight by the depth of soil between ground surface and proposed bore depth. This is sometimes also used as a crude initial estimate for geostatic stress estimation in bedrock; however, in the event that the rock mass either contains relic horizontal stresses or where rock mass conditions are highly variable, rock mass classification correlations and/or down-hole pressure meter testing may be beneficial in evaluating in-situ stress state, particularly for projects with advanced level of risk.
Pre-construction comprehension
A pre-construction understanding of the basic rock mass properties will help to significantly minimize adverse affects from structural geologic and overall rock mass controls. Many of the potential geotechnical challenges presented herein can be foreseen with an adequate field investigation program, including rock mass characterization, targeted use of instrumentation, and a laboratory testing program, completed by experienced geotechnical and rock mechanics practitioners. An appreciation and basic understanding of the prevailing discontinuity and rock mass properties can help the geotechnical and trenchless engineering design team better evaluate:
- Required drilling trajectory geometry like optimal bore diameter, elevation, entry/exit angles, horizontal and vertical curves, and overall pipeline orientation during feasibility or scoping level evaluations;
- Desired drilling fluid properties like the need for additives, viscosity control and need for any ground pre-treatment (e.g. grouting);
- The possibility of encountering mixed-face ground conditions;
- Drilling bit selection and characteristics of any back/over-reaming during pull-back, if required;
- Cutter-head selection with respect to abrasion resistance and desired production rate;
- The most appropriate trenchless method of product installation;
- Ideal entry/exit pit and receiving shaft locations with respect to ground conditions;
- Optimal direction of drive for tunneling-type operations, with respect to prevailing discontinuity orientations;
- Additional product pipe abrasion and puncture resistance demands;
- Ideal opening size with respect to discontinuity geometry and frequency;
- The need for tunnel support (e.g. lining, shielding); and
- MTBM lubrication demands;
Drill and blast tunnelling under a dam in Pennsylvania. Note the geologic structures on the rock sidewall.
ABOUT THE AUTHOR: David Scarpato, P.E., is a senior rock mechanics engineer for Haley & Aldrich in Bedford, NH. He can be contacted at DScarpato@HaleyAldrich.com, (603) 361-0397.
Comments