August 2012, Vol. 67 No. 8
Rehabilitation
Making The Grade: Smart A mixes teaching with testing at Grouting Fundamentals field day
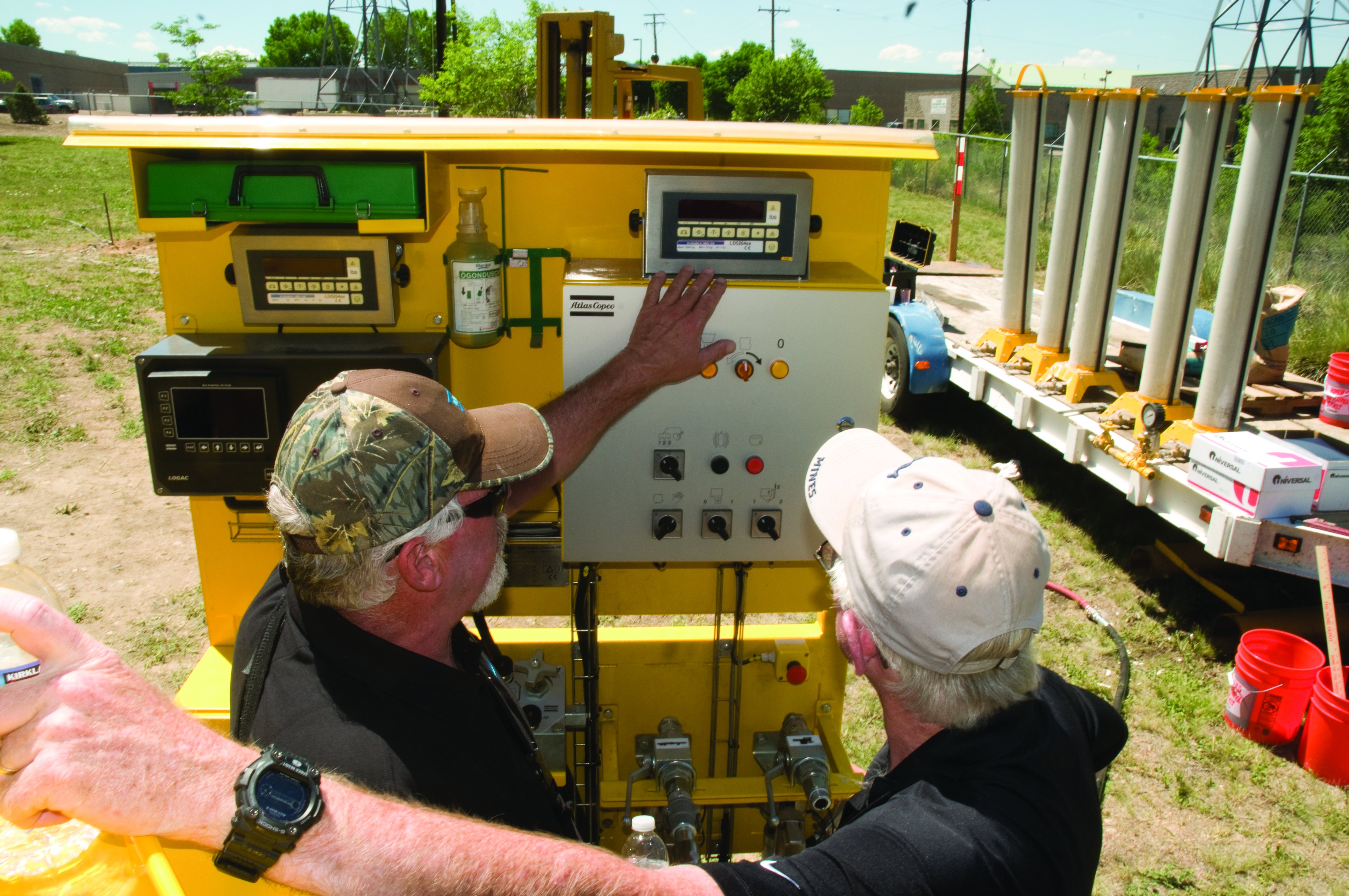
For the third year in a row Atlas Copco has contributed to the Colorado School of Mines Grouting Fundamentals and Current Practice field day. As part of the week-long class, students are presented with practical demonstrations of strategies, techniques and equipment.
More than 80 students attended this year’s course, which Colorado School of Mines has offered annually since 1979 except for the year 2001. Enrolees represented private contracting firms from the U.S. and Puerto Rico, as well as government agencies such as the Army Corps of Engineers and the Bureau of Reclamation. They also came from several countries from South America and Europe.
This year’s field day was hosted by Baski Inc., Englewood, CO. Demonstrations included micropile push and pull testing, admixture presentations, and a low-mobility compaction grouting application used on one of the company’s concrete storage slabs, as well as the school’s annual sand column permeation testing.
Intelligent grout plant
Atlas Copco donated use of a new Unigrout Smart A grout plant and a three-person presentation team. The plant was used to provide uniformly mixed grout to the exact specifications required for a Bureau of Reclamation sand column permeability test. The test was created to evaluate penetration performance of various grout brands by ratio and admixture content, comparing permeation differences resulting from such things as changes in grout thickness and the addition of plasticizers.
Business Development Manager of Atlas Copco Geotechnical Drilling and Exploration Bill Warfield delivered a brief presentation on the Unigrout Smart A as Ken McClanahan operated the system to mix and pump the grout for the sand column test.
Brian Iske of De Neef Construction Chemicals, who donated some of the materials used in the field experience, said that the Unigrout Smart A is exactly the kind of plant needed for his products. A colloidal mixer, Iske said, is the best way to ensure that every particle is completely and uniformly wetted during mixing for correct consistency.
How This Smart System Works
Unigrout Smart A intelligent grouting system comes in two versions, Dosac Lite and Dosac Full.
Dosac Full can store up to 99 grouting mix programs, enabling a pre-programmed batch to be called up on demand. Dosac Lite stores only one program, precisely repeating the water-cement ratio and mixing time batch after batch, for as long as water and grout are available.
In addition to its Cemix high-speed, high-sheer colloidal mixer and Cemag agitation tank, the Unigrout Smart A includes a Dosac control panel, two grout pump options and a Logac monitoring and logging unit. It is driven by a hydraulic power plant, such as a diesel-powered Atlas Copco Pug 45 D.
The plant may be operated in either fully automatic or manual mode. Upon start-up, water is injected into the Cemix and the high speed, high shear colloidal mixer starts. As soon as load sensors determine the correct weight of water is in the container, a separate circuit starts the cement silo’s auger feed. The silo is vibrated as cement is being fed into the tank, which guards against compaction, ensuring uniform consistency of the powder.
When the programmed mixing time is reached, the unit automatically transfers the batch to the Cemag agitank. The Cemag holds twice the volume of the Cemix, so it is possible to have up to three batches ready for pumping with only one agitank. Additional agitanks can be added to keep larger volumes and different batches available as needed.
The Unigrout Smart A uses one control box to operate either of its two pumps: a progressive cavity pump or the Pumpac piston pump.
The Logac grouting monitor and logging system may be used with any Unigrout grouting plant, but it comes as a standard feature of the Smart A. Set to grouting, Logac will record pressure, flow, and cumulative volume for each grouted hole by hole number.
Comments