July 2012, Vol. 67, No. 7
Features
IPR, EcoCast Thwart Threat Of Sewer Collapse
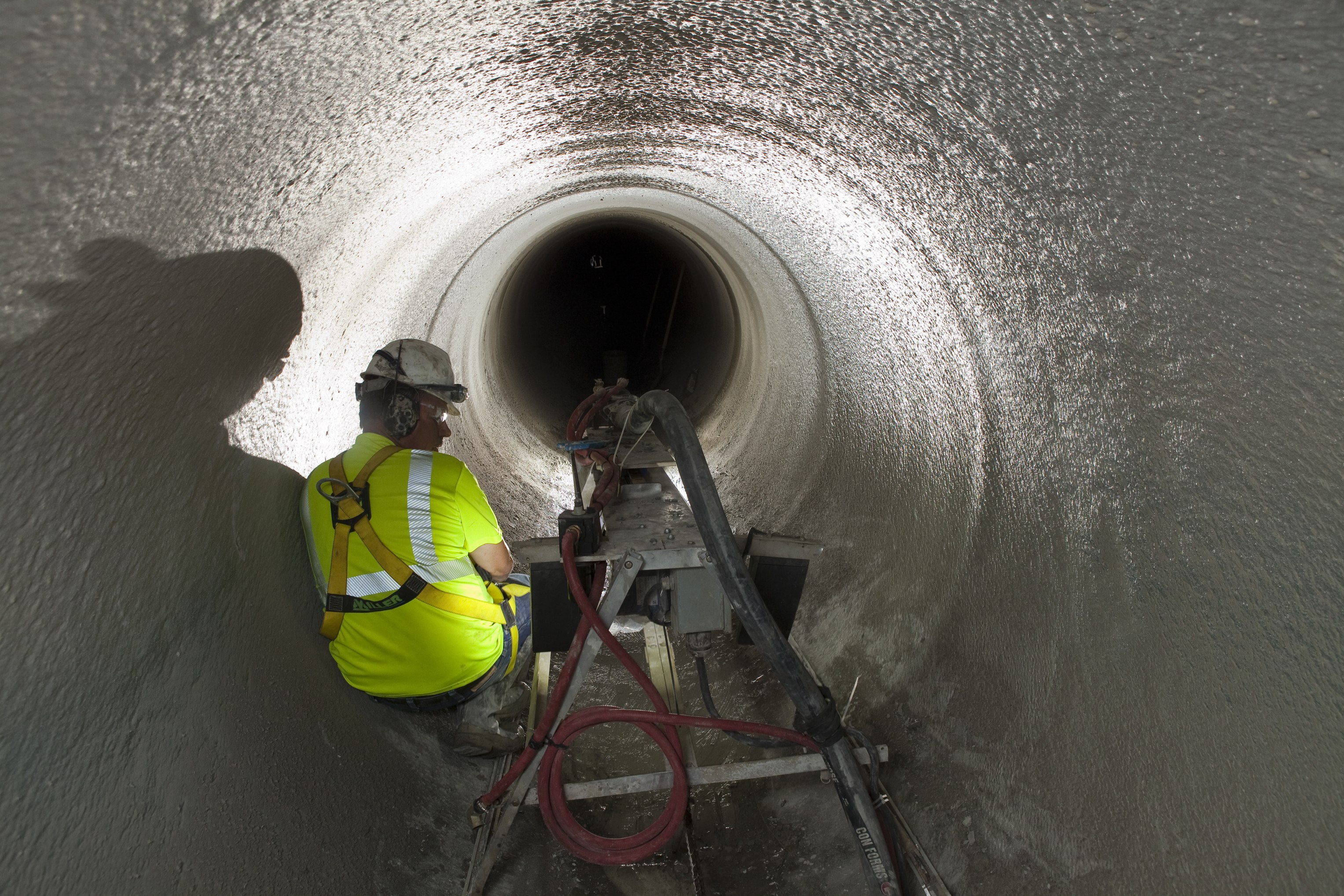
The threat that a large, severely deteriorated Houston sewer line could cause the collapse of a road at the intersection of a major highway was averted by a timely trenchless rehabilitation project.
EcoCast geopolymer liner was used to reline 700 feet of 72-inch diameter pipe that crosses under heavily-traveled U.S. Highway 59 in Northeast Houston.
The section of reinforced concrete pipe is a part of the city’s gravity-flow sewer infrastructure. It was 42-feet-deep and had been in the ground for 20 years. The pipe was leaking at multiple joints with infiltration a major concern. Ground above the pipe adjacent to the highway had shown significant settling.
“The original plan was to renew the pipe with cured-in-place pipe (CIPP),” said David Tajadod, managing engineer, the city of Houston. “But problems arose with the arrival of extremely high temperatures in the city which could affect that process, and we needed to find another method of construction so we could proceed.”
The entry excavation had already been completed and the bypass system was in place, Tajadod explained.
“We didn’t want to abandon the excavation,” he said, “and there was concern that the pipe would not make it until the fall.”
After considering the various options available, EcoCast was determined to be the best procedure for the project. The contractor was Inland Pipe Rehabilitation (IPR).
New tech
EcoCast is a high-strength, fiber-reinforced geopolymer that can be applied by mechanical pumping, spraying and trowel application. EcoCast liners form a crystalline structure for higher resistance to acids and greater surface durability, says IPR, developer of the product with development partner GeoTree Technologies. For the Houston project, the liner was used in conjunction with the company’s Anti-Microbial System (AMS), a coating that bonds to the geopolymer surface and destroys bacteria that causes corrosion.
The extreme depth of the pipe and limited access because of the distance between manholes were two factors that drew attention to EcoCast, said Nick Banchetti, IPR general manager.
Hot summer temperatures also complicated the installation.
“At the time [summer 2011], we were in the middle of the longest, hottest drought in the history of Texas,” said Banchetti. “Temperatures were over 100 degrees for about 90 percent of the time that work on the project was under way.”
Banchetti said one benefit of using EcoCast is that it avoided concerns that extreme heat can cause other technologies to begin curing prematurely.
Several factors complicated work on the project. “Lack of room to work was a problem — one of the access manholes was literally in a lane of the highway frontage road,” Banchetti said. “The length of the pipe run also caused concerns, and its depth created a very sharp bend that the liner had to follow into the pipe.”
As with many types of rehabilitation projects, the first step was to bypass flow in the pipe. The bypass system was installed to handle 20 million gallons per day (GPD). Service Pump and Compressors provided six, 8-inch pumps and three sets of 18-inch HPDE pipe for a total length of 4,000 feet.
Next came thoroughly cleaning the inside of the section of pipe. “The first step in the cleaning process was to use a jet vac truck to collect the majority of debris in the pipe,” said Banchetti. “Then IPR personnel entered the pipe and used high pressure washers to clean all interior surfaces. Materials that were cleaned from the pipes surface were gathered through the downstream manhole and disposed of properly.”
Next, multiple repair techniques were employed to eliminate infiltration which ranged from weepers to runners. Chemical grouting and cementitious materials were used to stop all infiltration before proceeding with the lining process.
Spin cast process
For this project, EcoCast was applied to the inside of the pipe by spin casting.
“The EcoCast process begins by placing the oscillating spin cast assembly into the far end of the pipe along with the product delivery hose, retraction chain, air hose and electric power line to the unit,” explained Banchetti. “The entire assembly is moved by a direct-drive electric motor at a predetermined speed. The application process is monitored continuously.”
Banchetti said the equipment utilized by IPR is designed specifically to deliver a very consistently mixed product at a known water to mortar ratio. The water ratio is carefully monitored and must be maintained on a measurable, consistent basis.
“The pump delivers material at a consistent rate and pressure, and has multiple alarms that detect either too little material at the pump or too much material in the mixing bin,” Banchetti explained. “The patent-pending oscillating spin cast assembly is unique to IPR. It delivers the ability to apply a very consistent amount of material to the pipe wall, applies a thicker lining per pass, and provides a final surface to the liner that enhances flow characteristics.”
Banchetti said physical properties of EcoCast, such as very high compressive strength, extremely high modulus of elasticity and very high bond strengths were matched to the material’s ability to flow through long lengths of pipe, work in a wide range of temperatures and to cure quickly.
The liner’s initial cure occurs in a matter of hours. Once the liner has initially cured, the Anti-Microbial System coating is applied to the pipe’s surface. Full flow may then be released within 24 hours of AMS application.
Right people, right product
Project Manager Gary Sherill and Technical Director Steve Henning played key roles in the successful completion of the project, said Banchetti.
Joe Cutillo, IPR president and chief executive officer, said that even though the project was in a very difficult location — both for traffic control and pipe depth — and performed during the hottest drought in the history of Texas, IPR personnel produced an end product that exceeded all expectations.
“Because IPR has the ability to perform every major rehabilitation technique in-house,” said Cutillo, “we believe it allows us to provide clients with the best possible technology for each particular project or site situation.”
The city of Houston’s Tajadod said utility staff members were aware of the new EcoCast product and method of installation.
“When the opportunity to use it presented itself, we were able to work with IPR on this project,” he said. “We created a change order because of the change in the scope of work, but did not have to increase the contract price. The completed work is a benefit to the community.”
Information from IPR identifies EcoCast as the first “green” geopolymer liner in the industry. It is designed to stick and adhere to virtually any surface; unlike traditional cement mortars, the geopolymer is capable of bonding and building to great thicknesses. It is an engineered, 100-percent, fully-manufactured product with no added non-contributing fillers. It is used for restoring concrete, brick, or corrugated metal storm and sewer pipes and is particularly effective for large-diameter pipe applications.
The city of Houston’s wastewater collection system contains more than 6,250 miles of sewer pipelines in sizes from six to 144-inches in diameter, with over 130,000 manholes. Sewer depths range from two to 80 feet. As in most systems this size, the threat that a large, severely deteriorated sewer line could cause a collapse at a major intersection or highway is common.
IPR is one of the nation’s largest trenchless rehabilitation contractors and provides a comprehensive portfolio of trenchless rehabilitation services.
FOR MORE INFO:
Inland Pipe Rehabilitation (IPR), (281) 362-1131, www.teamipr.com
Comments