July 2012, Vol. 67, No. 7
Features
Pipe Bursting Solves Environmental Issues
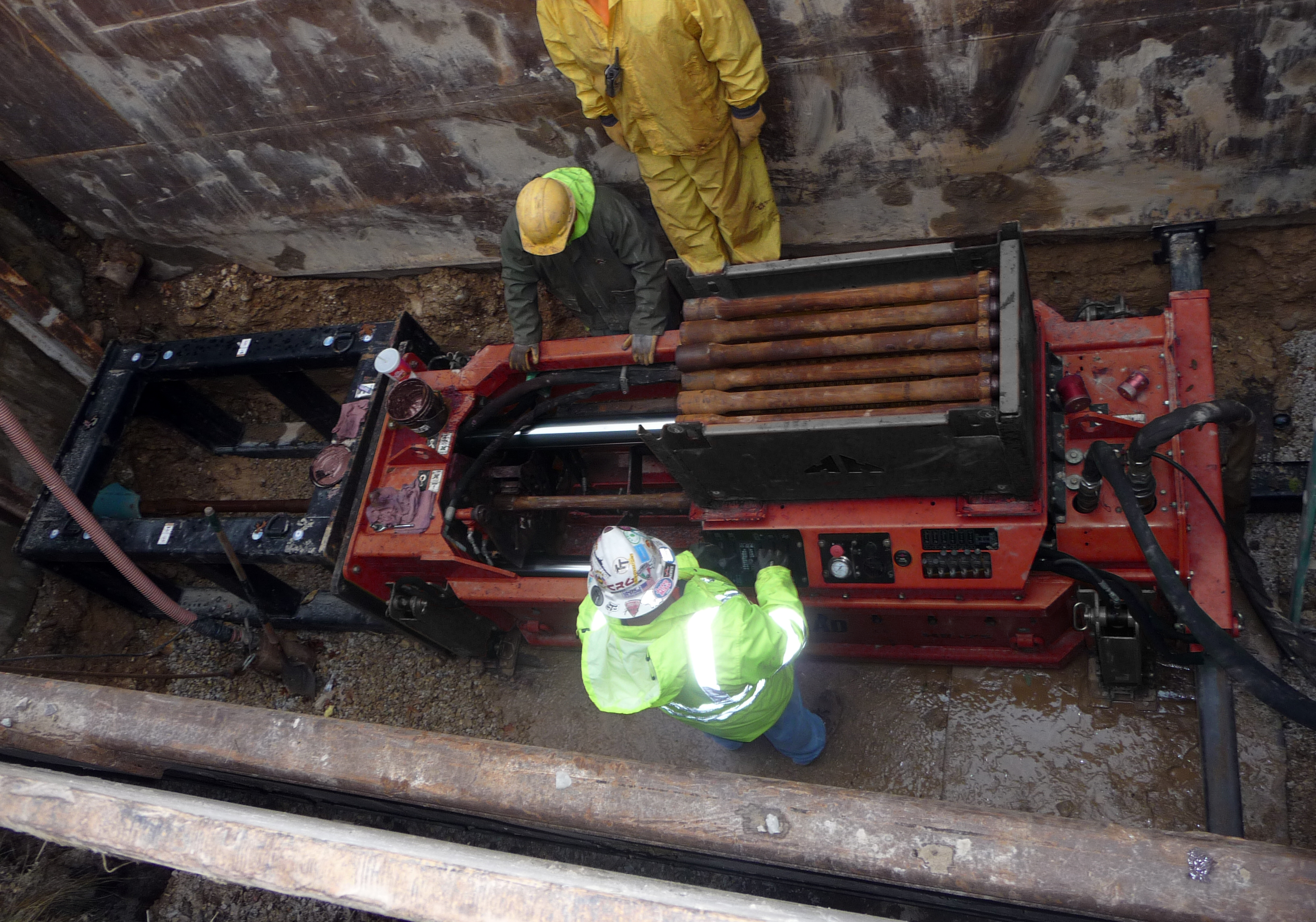
The city of Pewaukee, WI, recently upgraded its water supply system by spending $1.5 million to install 9,000 feet of 12-inch PVC water main. The city has two water systems, an East Side System and a West Side System.
“We wanted to combine the two systems to serve our customer base better,” says Jane Mueller, Pewaukee’s utility superintendent. “We wanted the reliability of the 12-inch main.”
To make the connection between the two systems, an 875-foot stretch of pipe consisting of both eight-inch PVC and 10-inch HDPE passed through wetlands. The city sought to expand that connection to 12-inch HDPE, but the wetlands presented a challenge. They are regulated by the Wisconsin Department of Natural Resources, which prohibits open-cut trenching in wetlands. Plus, the area is home to two endangered species of wildlife, a Butler garter snake and a rare species of frog.
The city’s answer: the trenchless pipe bursting process. Pipe bursting permitted the 875-foot run to be upgraded to 12-inch HDPE with only minimal surface disruption. “And just from the regulatory aspect, I think it was well worth the cost,” says Mueller.
In fact, pipe bursting for the 875-foot run cost $120 per lineal foot. Open-cut trenching also would have cost $120 per foot, but the pipe bursting avoided any expense for pavement restoration. A two-lane county road passed through the area, and an open trench would have required spending $12 per foot to restore the road.
“So the total cost per lineal foot would have been $132 for open cut,” says Ken Ward, project manager with the engineering firm of Ruekert & Mielke Inc., Waukesha, WI. “Pipe bursting saved us about $11,000, because they would have had to cut into the road with an open trench.”
Class C burst
To burst 875-feet of eight-inch and 10-inch pipe and upsize to 12-inch HDPE definitely ranks as a Class C pipe bursting project, according to the specifications of the International Pipe Bursting Association. Much of the run involved two upsizes.
The pipe bursting process uses a bursting tool or cutting head that is inserted into the pipe being replaced. A rod string is pushed through the run of pipe, and it is used to pull back the tool or cutting head, which shatters or splits the old pipe. An expander behind the head displaces fragments or pieces of pipe as the new pipe is pulled in behind it. Two types of bursting systems are available: pneumatic systems that use the percussive action of a hammer with a bursting head to crack the pipe – and static systems that use brute pulling force to pull back a cutting head and expander.
A key benefit of the method is reduced excavation requirements, which allows new pipe to be installed in areas where restoration would be costly and disruptive. Pipe bursting is the only rehabilitation method that permits replacement of the old pipe with a larger one.
In Pewaukee, the existing pipe consisted of three sections, all buried at about nine-feet deep. On the eastern-most end, where the pipe burst started, there was approximately 100 feet of C900 PVC pipe, eight inches in diameter. Moving westward, the next 200 feet consisted of 10-inch HDPE. The third and western-most section was 575 feet of eight-inch C900 PVC pipe.
The contractor, Advance Construction of Green Bay, WI, began construction by fusing together 40-foot sticks of HDPE pipe. It was specified as SDR 11 with a DIPS (Ductile Iron Pipe Size) equivalent of 12 inches. Advance sunk a 10-foot-deep insertion pit at the east end, and constructed two transition pits at the points where the pipe changed diameter and type. At the western transition pit, Advance placed a 40-foot trench box. The pipe bursting machine was anchored in the western-most pit.
Advance elected to pull the entire 875-foot run in one long pull, but with tooling changes at the transition points. For the job, the contractor chose to rent a HydroBurst HB 175 static pipe bursting machine from HammerHead Trenchless Equipment, Oconomowoc, WI. The machine features 175 tons of pull-back force and is powered by a 73-horsepower engine. The hydraulic system develops 4,000 psi of pressure and has a flow rating of 43 gallons per minute.
HDD created friction problem
For the 200-foot stretch of HDPE pipe, a specialized cutting head was developed to slice through the pipe. However, this pipe was installed by directional drilling in 2004, so it had only been in the ground for seven years. Furthermore, the HDPE pipe still had lubricant jell surrounding it. When the cutting head and expander began to pull through the 10-inch HDPE, there was not enough ground friction to hold the pipe in place to slit it.
“We knew that was going to be difficult,” says Ward. “That newer HDPE just expands, and we knew the chance of getting hung up on it was pretty high, because it won’t shatter. It just expands.”
Jeff Tremel, project superintendent for Advance, explains the problem and solution: “There are two knives welded onto the tool, and the theory is to slice the poly, then the expander will go through and slip the two halves to the side. But because of the lack of ground friction, that did not happen. We ended up dragging the old pipe, because there was not enough resistance in the ground.
“The old pipe just kept coming forward into our transition pit,” says Tremel. “We had to cut it by hand – with a pipe saw – to get it out of the way. Otherwise it would have strewn all over like spaghetti. We split it because it came over the top of the rods.”
At each of the two transition pits, Advance changed tooling. “We changed tooling twice,” says Mike Walk, the training specialist for HammerHead who operated the machine. “We put the 10-inch pilot on when we went into the HDPE, and then when we got back to the PVC, we put the eight-inch pilot back on.” The pilot is a piece of steel tubing that keeps the bursting head centered inside the old pipe.
Plan comes together
Tremel of Advance said the PVC pipe burst exactly according to plan. “Bursting the C900 went perfectly,” Tremel said. “It split, shattered, fractured, went right to the side. It worked like it should.”
Both Tremel and Glenn Joski, Advance president, said HammerHead provided excellent technical support throughout the project.
HammerHead provides their customers free project consultations. “Part of providing the consultation is gathering information,” says Nate Hrabosky, regional sales manager for HammerHead. “We send out a pipe bursting questionnaire to the contractor well ahead of the actual burst. The questionnaire asks the contractor 44 questions about the project – and requires an answer to each one – so that we can provide the correct solution for their project and make sure the right equipment shows up on the job.”
Tremel said a crucial factor to the project’s success was the set-up in the pit that contained the bursting machine. “It was very critical that we restrain the machine back,” he says. “We did it with I-beams and plates. We drove two 12-inch I-beams into the ground like tent stakes, and that’s what the machine pulled against.”
Joski said the actual pipe bursting work took just three days. The first day was spent in preparation, and the pull-back took two days. After cutting in a fire hydrant at a transition pit, Advance made the connections at the reception pit and buttoned up the project.
Mueller said she was very satisfied with the pipe bursting process. “I would definitely consider using pipe bursting again,” she concludes.
FOR MORE INFO:
HammerHead, (800) 331-6653, www.hammerheadtrenchless.com.
Comments