October 2012, Vol. 67 No. 10
Features
CIGMAT Report: Center Studies Concrete Coatings And Repair Methods For Corroded Steel Piles
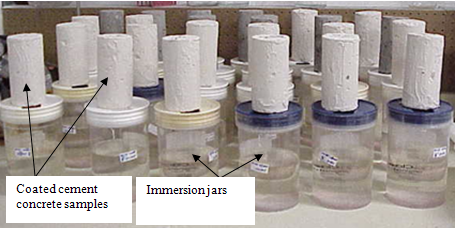
The Center for Innovative Grouting Materials and Technology (CIGMAT) is currently working on projects related to composite coatings to protect reinforced concrete and repair methods for corroded steel piles. Over the years, CIGMAT researchers have developed unique testing facilities and developed test protocols approved by the U.S. Environmental Protection Agency to test grouts and coatings for infrastructure rehabilitation. A Life Cycle Cost model (CIGMAT-LCC) for wastewater systems has been developed and may be viewed on the CIGMAT website.
In the past two decades, over 55 commercial products including coatings, grouts, liners, concrete and polymer composite have been researched and tested for various applications. The observed trends are analytically and numerically modeled to better understand the influence of various testing and environmental parameters. Every effort is being made by CIGMAT researchers to transfer technology from control studies to actual applications. The industrial members and federal, state and local agencies fund the ongoing research studies at CIGMAT. The director of CIGMAT is Dr. C. Vipulanandan (Vipu), P.E., professor of civil engineering at the University of Houston, Houston, TX.
Recently, CIGMAT received a three-year $2.6 million research grant from the non-profit Research Partnership to Secure Energy for America and funded by the U.S. Department of Energy, to conduct research on developing smart cement and drilling mud for real-time monitoring of oil well installation and performance during the entire service life. Oil field services firm Baker Hughes is providing $500,000 in additional funds.
CIGMAT organizes an annual conference and exhibition on the first Friday in March on “Construction and Rehabilitation Activities Related to Houston & Other Major Cities” at which speakers are invited from major cities and transportation authorities around the country to present and discuss projects and problems related to construction, maintenance and rehabilitation issues. The conference also covers technical issues related to maintenance and rehabilitation of water and wastewater systems, nondestructive testing methods, and development of smart materials for various applications. Several geotechnical topics related to expansive clay, rapid deep foundation construction and ground faulting are also discussed. Conference proceedings for the past 12 years are posted on the CIGMAT website at cigmat.cive.uh.edu.
Composite coatings for reinforced concrete
Corrosion in reinforced concrete structures is of concern because it requires almost immediate repairs and rehabilitation to extend the service life of the structures. Concrete structures buried underground and in the coastal region are undergoing accelerated deterioration owing to the corrosion of the embedded reinforced steel. The presence of moisture, chlorides and loss of the alkaline environment causes the embedded steel to lose its surface passivity. Accumulated corrosion products cause cracking of the protective concrete cover. Deterioration caused by the corrosion of steel is not limited to bridges but also includes offshore and coastal structures, dams, buried pipes and piles (Pan and Vipulanandan 2012; Vipulanandan et al. 2011 & 2008; Klahorst et al. 2004; Pfeifer and Scali, 1981). Steel corrosion is accelerated when the protective concrete cover over the embedded bars is inadequate and where there are cracks which accelerate the migration of moisture and salt. Hence there is increasing interest in developing relatively quick test procedures to evaluate the effectiveness of composite coatings to reduce the infiltration of water and salt solutions into concrete structures to rapidly rehabilitate and extend the service life of reinforced concrete structures.
Corrosion in reinforced concrete is influenced by three mechanisms as diffusion, corrosion and deterioration; but the diffusion period is the most critical (Liu and Vipulanandan 2003; Mebarkia and Vipulanandan 1995; Cady et. al. 1984). It must be noted that the deterioration stage will not start if the moisture, oxygen and/or chloride concentration levels are relatively low (Zemajtis et. al. 1998). Since reinforcement corrosion is dependent on the availability of moisture, oxygen, sulfate and chlorides, any methodology to reduce their ingress into the concrete mass will reduce concrete deterioration (Liu and Vipulanandan 2003 and 2004).
Several methods are used in protecting concrete surfaces including coating the concrete. Coating materials used in protecting concrete from corrosive environments include epoxies, methacrylate, urethane, silicate, siloxane and silanes (Vipulanandan and Issac, 2008; Vipulanandan et al. 2002(b), 2005). The primary function of a surface treatment is to prevent capillary action at the surface, thus preventing the migration of water and chloride ions into the concrete. Surface treatments materials used for protecting reinforced concrete structures include sealers and coatings. The general difference between sealers and coatings is that sealers penetrate the concrete surface and block the capillary pores, whereas coatings do not penetrate the concrete surface but form a thick film on the surface.
Concrete sealers can be divided into two main groups: pore blockers and hydrophobic agents (such as silanes and siloxanes). Hydrophobic sealers penetrate the concrete to some degree, while pore blocking sealers provide little penetration and instead form a thin film on the concrete’s surface. Pore blockers are further distinguished by their ability to partially or fully fill the surface pores; a capability not shared by hydrophobic agents (Wohl and LaFraugh, 1990). Concrete sealers work in two ways. First they substantially reduce the absorption of chloride ions and moisture. Secondly, they allow the progressive internal drying of concrete by reducing the rate of moisture gain from the environment. Hence the sealer protects the concrete and makes it breathable. Most sealers are not permanent; hence periodic reapplications may be necessary to maintain the protective properties of the sealers (Vipulanandan et al. 2008; Klahorst et al. 2004; Perkins 1997; Wohl and LaFraugh, 1990). To provide long-term durability by protecting the sealers and avoid their reapplication, the potential of resisting chloride and moisture intrusion by a combination of sealer with coating was investigated in the current study.
Performance of the silanes and coatings could be evaluated by monitoring the weight change of coated concrete specimens immersed in corrosive environment. This change in weight of coated concrete could be used as a measure for degree of deterioration of the concrete, and hence, the prediction of the weight change is very important for predicting the service life of coated concrete. Mathematical modeling of the weight change phenomenon can help in determining the coating parameters, which could be used in evaluating the effectiveness of coating materials. To evaluate the quality of concrete in resisting water intake a diffusion model for concrete cylinders without coating was developed by Mebarkia and Vipulanandan (1995). A thin film model has been developed by Vipulanandan and Liu (2002a) to evaluate the performance of coating during the immersion phase. These models were used in this study to investigate the performance of treated concrete with coatings and silanes.
Research objective
The overall objective of this study was to investigate the effectiveness of combining sealers with coating to protect the concrete from chloride and moisture intrusion. Two silanes, (Silane-1 and Silane-2) with a latex coating (Coating-1) were used. The specific objectives were as follows:
1. Evaluate the treatment with silane, with and without latex coating, in controlling the water and 15% sodium chloride solution diffusion/infiltration (Immersion Test for 21 days) and exfiltration/breathing (Drying Test for 21 days) in concrete .
2. Model the wetting process using the finite element method.
Materials used
Cylindrical concrete specimens (3-inch diameter x 6-inch height) were obtained from an on-site concrete batch plant used for constructing a bridge across a causeway. The concrete used was classified as class F concrete by the Texas Department of Transportation. Concrete specimens (cylinders) had an average unit weight of (based on 20 specimens) 140 pcf (22 kN/m3) standard deviation of 0.9 pcf, (0.14 kN/m3) COV of 0.62%, and an average compressive pulse velocity of 4070 m/s. The average 28-day compressive strength of concrete was 36.5 MPa. The water and 15% salt solution absorption in 21 days into the concrete were 1.64% and 1.53% respectively (Table 1). There was notable difference in the weight change during the drying phase for concrete that was in water compared to the 15% salt solution (Table 1).
Table 1: Immersion and Drying Test Results for Uncoated Concrete
Commercially available silanes denoted as Silane-1 and Silane-2 were applied with the latex based coating denoted as Coating-1, to the concrete substrate. Silane-1 was a micro-emulsifiable concentrate based on silanes and alkoxysilanes. The typical dilution used was nine parts of water to one part Silane (volume based), although varying dilutions can be used to achieve different degrees of water repellency. Silane-2 was clear, penetrating and breathable water repellent designed for the protection of exterior above-grade concrete. It penetrates the surface and bonds chemically to the substrate, resulting in permanent attachment of the water repellent molecule. Coating-1 was water based latex coating with rapid drying, good adhesion and high flexibility. Coating-1 was applied using rollers. Application temperature was 65°F. The coated surface was left to dry for four days before testing. Some of the properties of pure silane and coating are summarized in Table 2.
Table 2: Properties of Pure Silane and Coating
Sample preparation and testing program
The experiments were performed at the University of Houston-CIGMAT laboratory. The test program comprised of coating the concrete specimens, immersion in various solutions followed by drying at room condition.
Concrete specimens were cured for at least 28 days before cleaning and drying prior to the application of silanes and the coating. The concrete surface was cleaned using a water blaster. The specimens were dried at room condition for one day before spraying the silane sealer. The silanes were applied by spraying onto the surface using 15 psi (103 kPa) low pressure positive displacement airless spray equipment. After applying the silane sealer, the specimens were cured for five days before applying the Coating-1 (latex-based). The coating was applied using a roller. The coating was white in color and the application temperature was about 20°C. The specimens were weighed during the coating cycle accurately to 0.01 gms. Addition of Coating-1 to the specimens changed the weight of the specimen by about 3%. The coated specimens were cured at room condition for 21 days before immersing in water and 15 % NaCl solution.
The specimens were totally immersed in selected test reagents in closed immersion jars. The two test solutions selected for the study were (1) tap water (pH = 7 to 9) and (2) 15% NaCl solution (representing the accelerated test condition in marine systems) as recommended by NCHRP 244 (Pfeifer et. al. 1981). In this test, changes in weight of specimen and appearance of specimen were monitored for 21 days (CIGMAT CT-1, ASTM G 20) (ASTM 1998, CIGMAT).
In order to study the drying pattern of coated concrete, the NCHRP 244 (Pfeifer et. al. 1981) method was used. The weight changes in the coated and uncoated concrete were monitored at regular intervals for up to 21 days. Drying of the coated specimens is shown in Fig. 1.
Figure 1: Specimens being dried for measuring the weight change during the drying cycle
Test results
Wetting Phase (in water)
The relationships between the percent weight change and time for coated specimens in water and 15% NaCl solution are shown in Figures 2, 3, 4 and 5 respectively. The average weight increase in water after 21 days, for specimens coated with Silane-1 was 1.09% as compared to 0.69% for specimens coated with Silane-2. Similarly, weight increase for coated specimens with Silane-1 and Coating-1 combination was 2.3% as compared to 1.21% for Silane-2 and Coating-1 combination. Maximum weight gain was observed for specimens coated with Coating-1 as compared with any other combination. This implies that Coating-1 absorbed more water and governed the water intake for cases where Coating-1 was the outer layer.
Wetting Phase (in 15% NaCl solution)
Weight increase in 15% NaCl solution after 21days, for specimens coated with Silane-1 was 0.69% as compared to 0.26% for specimens coated with Silane-2. Similarly weight increase with specimens coated with Silane-1 and Coating-1 combination was 2% as compared to 1.51% for Silane-2 and Coating-1 combination. Weight gain of specimens coated with Coating-1 was similar with specimens coated with Silane-1 and Coating-1, which reinforces the fact that Coating-1 governed the solution uptake in the cases where Coating-1 was the outer layer. However it can be observed that the combination of Silane-2 and Coating-1 was more effective in resisting the solution intake in all cases as compared to the Silane-1 and Coating-1 combination.
Drying Phase
The residual solution in the specimens at the end of the drying phase reduced to zero for the Silane-1 and Coating-1 combination as compared to 0.05% for the combination of Silane-2 with Coating-1 when immersed in water. However Silane-2 with Coating-1 proved to be a better combination over Silane-1 with Coating-1 when immersed in 15% NaCl solution as it drained out all the solution at the end of the drying phase. Corrosion of reinforced concrete is very much influenced by the diffusion phase (Cady et. al. 1984) and hence the immersion process should govern the selection of the coating type to be used for protecting structures.
Figure 2: Weight change kinetics in water followed by drying for concrete coated with Silane-1 and Coating-1
Figure 3: Weight change kinetics in water followed by drying for concrete coated with Silane-2 and Coating-1
Figure 4: Weight change kinetics in 15% NaCl solution followed by drying for concrete coated with Silane-1 and Coating-1
Figure 5: Weight change kinetics in 15% NaCl solution followed by drying for concrete coated with Silane-2 and Coating-1
Finite element modeling of the weight change
The effect of mass transfer coefficient of the coating material on the weight change of coated concrete cylinder was also studied by using the finite element method. A commercially available finite element program was used for the modeling. Due to the symmetry the concrete cylinder was modeled as a 2D axis symmetric model. The concrete diffusion coefficient (Dconc = 15×10-12 m2/sec) was obtained based on the test results (Vipulanandan et al. 2011). Three node linear triangular elements were used. The finite element mesh configuration with triangular elements used in this study is shown in Figure 6. Mesh sensitivity analysis was performed by varying the number of elements from 8,365 to 15,462. The prediction (weight change with time in Figure 7) converged with a minimum of 12,792 elements onwards. Hence a total number of 12,792 elements were used for detailed analyses. The model was solved to get the degree of saturation and normal diffusive flux at different instants with time. In Figure 7, the finite element model prediction of weight change is compared to the experimental results and the agreement was very good.
Figure 6: Finite element model used for modeling the weight gain of coated cement concrete cylinder
Figure 7: Comparison of FE model prediction of weight change with the experimental data for Silane-1coated concrete immersed in water
Conclusions
Applicability of two commercially available silanes (Silane-1 and Silane-2) in combination with a latex based coating (Coating-1) in resisting absorption of water and 15% NaCl solution was investigated. The following conclusions are advanced:
1. The test method (21 days of immersion followed by 21 days of drying) was effective in identifying the differences in performance of the composite coating.
2. Finite element modeling of the weight change phenomenon of a coated concrete cylinder revealed that the initial rate of weight gain was governed by the quality of the coating material (diffusion parameter); however, the total amount of weight gain was governed by the quality of concrete behind the coating.
Comments