July 2013, Vol. 68, No. 7
Features
CIPP Project Requires Complex, Challenging Bypass Pumping Plan
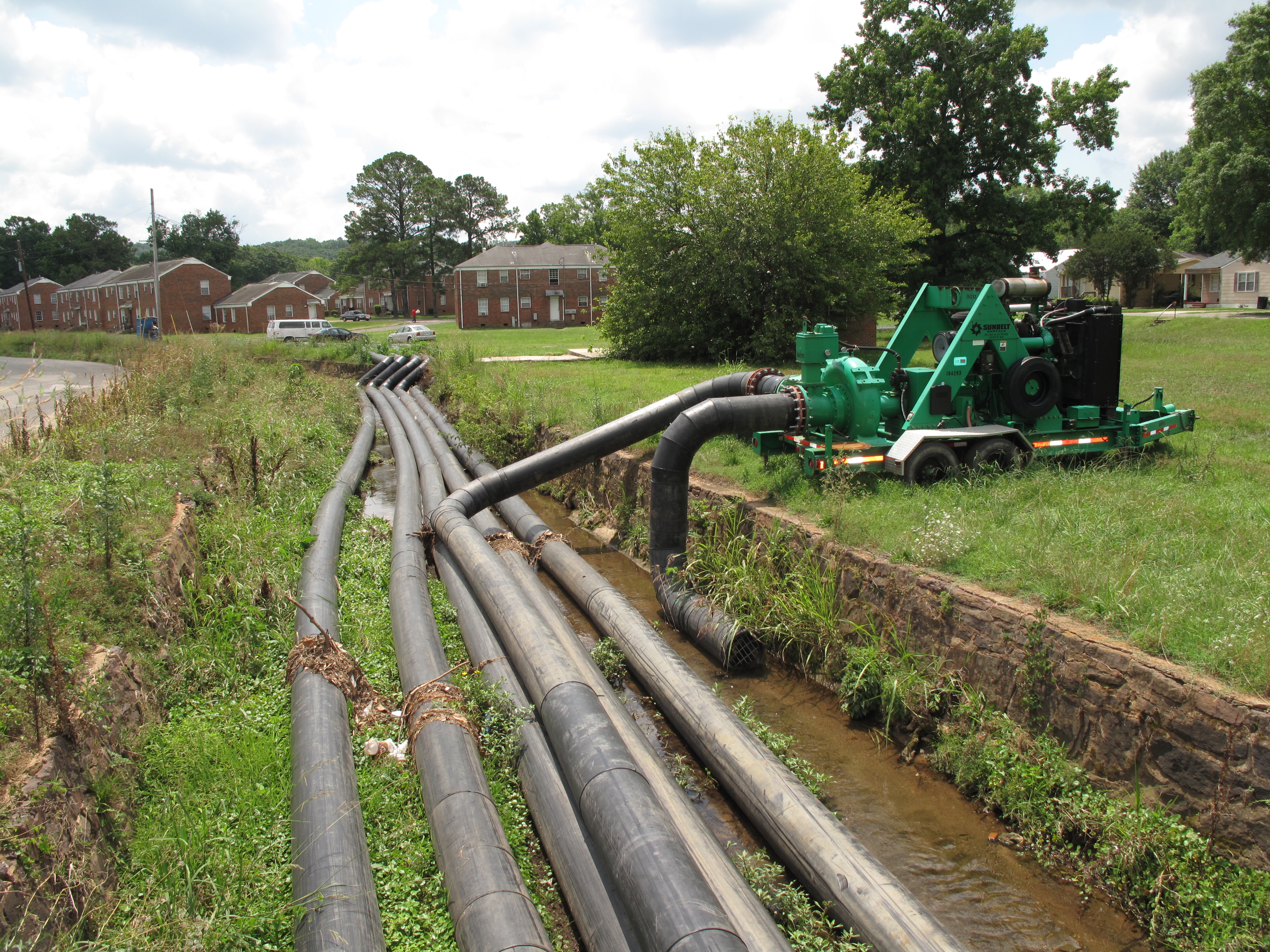
An essential element in many projects to rehabilitate buried pipe is the design and construction of a bypass system to carry flow during the period the segment being restored is out of service.
In many instances, design and installation of the bypass is just as complex as the job of rehabilitating the pipe.
A recent example is the bypass needed for cured-in-place pipe (CIPP) lining that involved 6,100 feet of 54-inch diameter reinforced concrete sewer pipe for a project for Jefferson County, AL.
To accommodate required daily flow rates, the bypass system required five runs of 18-inch HDPE pipe totaling 18,500 feet and six 18-inch Sunbelt Quiet Flow pumps.
The project owner was the Jefferson County Commission. Prime contractor was Layne Inliner, Sunbelt Rentals was the contractor for the bypass system and CH2MHill was the project engineer.
“The project involved one of the largest lining projects in recent years for Jefferson County,” said Ladd Gould, Sunbelt national strategic account manager. “The size and magnitude of the bypass made for one of Sunbelt Rental’s more challenging bypass installations.”
To eliminate the additional cost of bypass relocation, the system was designed to bypass the entire work area — just over 7,800 feet, said Gould.
“In order to achieve the specified flow of 40-million gallons per day (mgd),” he explained, “Sunbelt concluded that five runs of 18-inch HDPE were necessary to reduce the total dynamic head on the bypass system. This design required the installation of 38,500 feet of 18-inch diameter HDPE pipe. Constructing the full-length bypass also reduced the expense of placing additional suction structures on the sewer.”
Bypass route
The project plan did not specify the route of the bypass leaving Sunbelt with the responsibility of selecting the best route for the five runs of pipe.
“As it happened,” Gould continued, “there was a drainage canal that ran through the town of Bessemer where the pipes could be placed which greatly reduced the bypass impact on the area by avoiding road closures, traffic control, trenching and property restoration.”
Suction structures were installed upstream from the starting point of the lining on the existing 72-inch sewer that fed the 54-inch pipe. Because of the depth of the sewer and volume of sewage that was required to be bypassed, three new structures were “dog housed” on top of the 72-inch sewer for suction access.
“To provide the full 40 mgd pumping capacity, the six 18-inch pumps were put in place, one being a backup which actually allowed for more than 50 mgd capacity,” Gould said. “All six pumps were set up on transducers to avoid unnecessary fuel burn. In addition to the suction structures, the six pumps were ‘benched down’ by lowering the elevations of the pump pads four feet to reduce the suction lift, thereby increasing bypass efficiency.”
Once the pumps were placed, the discharge was then piped into a 40-foot-long, 42-inch manifold with six 18-inch ports with knife gate valves for the bypass pumps, and five 18-inch ports with valves for the five 7,800-foot lengths of 18-inch HDPE discharge lines.
A month after the project was bid, the status of the project became unclear when Jefferson County filed for Chapter 9 bankruptcy protection.
“After reassurances from the county and project engineers, work proceeded as planned,” said Gould. “However, mobilization of the bypass was delayed due to permitting issues with a railroad. The bypass discharge pipes had to pass through a creek under a railroad bridge, which caused concern for the railroad about the amount of potential water displacement if there was a heavy rain event. To address this concern, we added a 24-inch, Sunbelt 425 horsepower auto-priming diesel pump with auto-start to elevate any excess high water from the creek.”
Sunbelt utilized three setup crews with three McElroy 617 TracStar fusion machines working in different locations to expedite the set up.
“While the 38,500 feet of bypass piping was installed, the pumps and manifold were tied in to the system,” Gould continued. “Once everything was connected, the bypass was then hydrostatically tested and liquid level transducers were programmed to run the pumps at different surcharge levels.”
Construction challenges
Construction of the bypass took almost two months to complete.
“This time would have been reduced had there not been a major weather event during the second week of the bypass build,” said Gould. “The town of Bessemer, where the discharge piping was located, experienced heavy rainfall and tornados causing approximately 2,000 feet of discharge piping to be washed down the creek. Our crews spent the next few days retrieving the discharge pipe. Needless to say, the flash flood became a major concern of the project from a liability standpoint, requiring that a new plan be developed.”
Sunbelt worked with Layne to get a new route approved by CH2MHill.
“As a result,” Gould said, “the creek was used for only 30 percent of the project which greatly reduced liability, but it came with extensive traffic control and an unavoidable road cut. The impact, however, was reduced on the residential streets by running the discharge down the center and utilizing traffic control with detours and one way traffic to avoid multiple driveway cuts.”
Gould said the bypass system ran flawlessly for eight weeks with Sunbelt performing pump watch with a fully stocked service vehicle 24 hours a day, seven days a week.
“The technician was responsible for monitoring, servicing and fueling the pumps,” he said. “In addition, the technician was responsible for monitoring the air pressure in the pneumatic plugs blocking the 72-inch sewer line. Due to the large diameter of the sewer, the plugs have a limited amount of allowable back pressure so the surcharge levels in the sewer were closely monitored by the readings from the pumps transducers.”
Despite unexpected challenges, CIPP lining was completed ahead of schedule. Bypass breakdown took only about a third of the setup time. However, Gould said it was not done all at once, but was carefully planned to allow for load-out of pipe to be shipped to other bypass projects across the southeast to avoid handling the pipe more than once.
“The success of the project is the result of combined efforts of a strong team, including the design engineer, CH2MHill, prime contractor Layne Inliner and Baird Contracting, a Layne subcontractor,” concluded Gould.
Based in Fort Mill, SC, Sunbelt Rentals is a wholly-owned subsidiary of Ashtead Group and operates more than 400 rental locations throughout the United States serving the needs of a wide variety of customers ranging from utility, commercial, residential, municipal, specialized service industries and do-it-yourself customers. Sunbelt identified itself as the second largest equipment rental company in the U.S.
FOR MORE INFO:
Layne Inliner Technologies, (812) 723-0704, www.inliner.net
CH2M Hill Area Office, (205) 326-8912, www.ch2m.com
Sunbelt Rentals, (800) 667-9328, www.sunbeltrentals.com
McElroy Manufacturing, (918) 836-8611, www.mcelroy.com
Comments