July 2013, Vol. 68, No. 7
Features
Rehab Under The Runways: EcoCast Technology Matched Project Demands At Cecil Airport
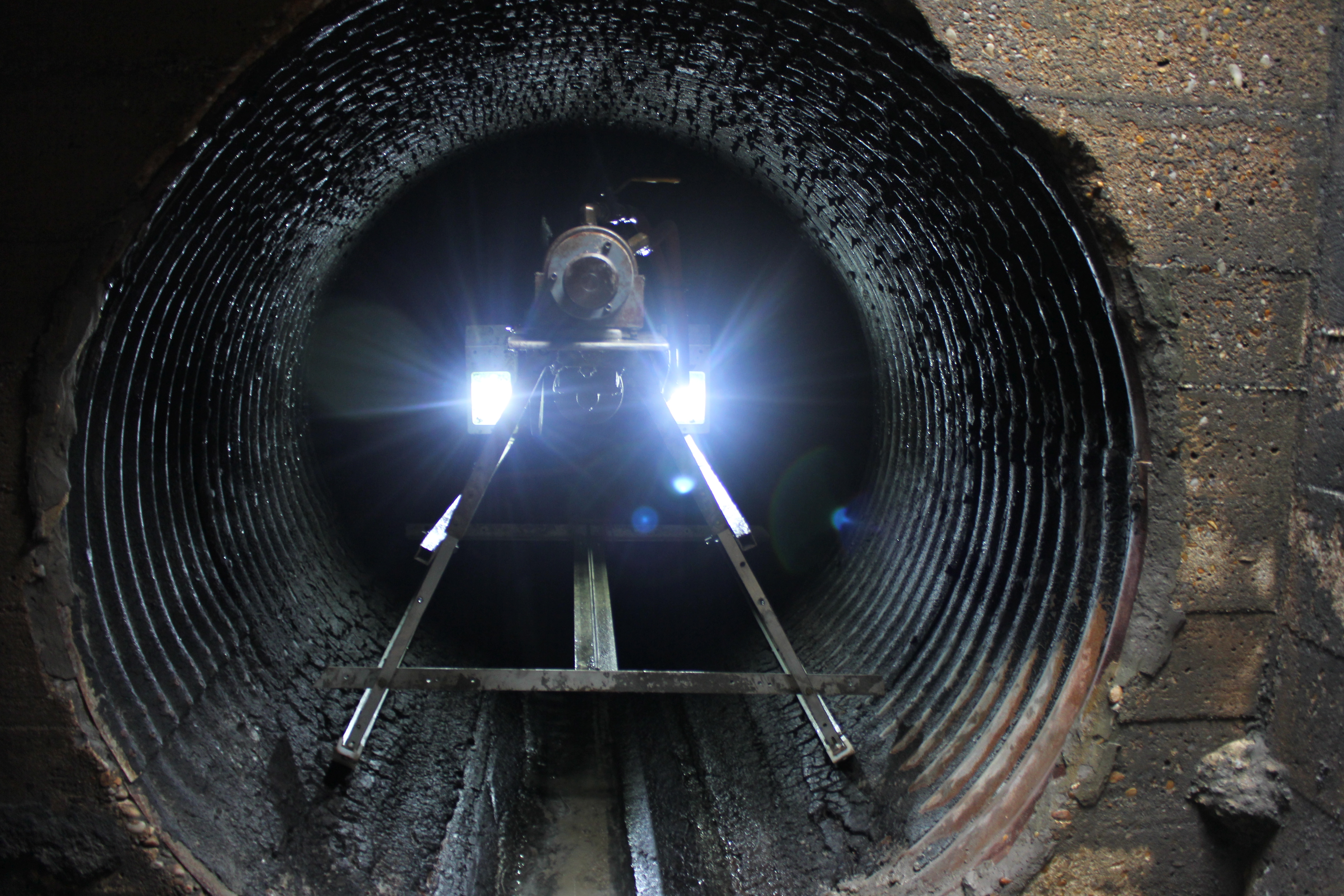
Methods to rehabilitate and replace old and deteriorating underground pipelines have advanced rapidly in the past decade, and today there are multiple trenchless procedures for replacing, rehabilitating and repairing buried infrastructure.
Indeed, utility and facility owners today are quick to turn to trenchless methods when open-cut construction is too costly, impractical or impossible.
The Jacksonville Airport Authority routinely uses trenchless construction to address issues with underground infrastructure beneath runways, taxiways and other locations where extensive excavation would seriously disrupt airport operations.
Jacksonville’s busy Cecil Airport supports government and civilian aviation operations and aircraft maintenance, repair and overhaul activities plus aviation training. In 2012, total airport traffic was 45,397, ranging from more than 3,700 to 9,300 take offs and landings per month.
Obviously a priority of any type of construction at the facility is that the work does not disrupt air traffic and other airport activities, often making trenchless construction the best option for maintenance and improvements to the airport’s underground water, storm water and sewer pipes, many of them beneath runways and taxiways.
A recent example is the rehabilitation of approximately 1,400 feet of storm water lines beneath a Cecil Airport tarmac and taxiway. Storm water is collected from grates across the facility and is transported to an outfall area located just to the east and south of airport runways, said Jacksonville Airport Authority Project Manager Art Waczkowski. The pipes have been in the ground for more than 40 years and he described their condition as “poor.”
“Some of the concrete above the pipe had begun to settle, so it was time for rehabilitation,” he added.
Selecting the method
Clearly the project called for trenchless construction. For this project EcoCast — an advanced geopolymer liner that is centrifugally-cast onto the inner wall of the deteriorated pipes — was the method selected.
“Because this is a major aircraft maintenance and repair facility, it was important that operations continued throughout the project,” said Waczkowski. “The EcoCast set up was only a fraction of the construction footprint we originally planned for. Any other form or repair would have forced us to adjust airport operations. For example, we have used cured-in-place-pipe (CIPP) lining in the past, and the presence of the crane needed for CIPP work would have violated height restrictions and required closing one runway.”
IPR/PM Construction was the prime contractor for the project to rehabilitate the four storm water pipes with diameters of 54, 60, and 66 inches. Some sections contained multiple diameters of pipe, said Matt Werth, IPR/PM Construction Florida general manager.
Originally specified for sliplining, Werth said IPR presented EcoCast as an alternative based its application versatility, its smaller footprint requirement, compliance with height restrictions, fast installation time and less impact on the Cecil Airport customers.
The first step in the process was inspection of the pipe, pressure washing to remove sediment and loose debris and filling water intrusions and any voids in the existing pipe.
The footprint for equipment to make the EcoCast installations was small — less than 200 square feet.
“The only things needed on the ground were a hopper, a temperature-controlled water supply for mixing the material and service trucks — everything else is done underground,” said Werth. “IPR’s EcoCast liner is applied by spinning spray heads mounted on a proprietary sled.”
The system’s pump delivers material at a consistent rate and pressure, and has multiple alarms that detect too little material at the pump or too much material in the mixing bin. The patent-pending oscillating spin cast assembly applies a consistent amount of material to pipe walls, and the product’s inherent physical and chemical properties allow for a quick cure cycle.
The sled is lowered through a standard size-manhole in two sections; then quickly assembled inside the pipe. The sled itself is approximately four-feet long by three-feet high, and 2½-feet wide at the base and is pulled through the pipe by a dual-capstan winch.
The thickness of the EcoCast material is controlled by the amount of material applied and the speed of the sled through the section of pipe, Werth said. Specifications called for a lining thickness similar to a CIPP liner which is required for a typical gravity storm water line.
Quick turnaround
Most storm drain pipes can be returned to service within 24 hours of the application, Werth pointed out. When fully cured, EcoCast lining is fully structural, corrosion resistant and eco-friendly. It was the first time EcoCast was used at Cecil Airport.
Start to finish, rehabilitation of the four runs of drainage pipe took seven weeks.
As with any construction on an airport, Federal Aviation Administration (FAA), Transportation Security Administration (TSA) and Cecil Airport regulations controlled access and construction procedures on the work site.
“Prior to the start of construction,” Werth said, “IPR personnel received one week of training on safety, security and airport protocol by Jacksonville Aviation Authority personnel. Each work area was secured and marked, and we were careful to follow all required guidelines and procedures.”
EcoCast is a product of IPR/PM Construction and its development partner GeoTree Technologies. It is marketed as a proprietary system combining advanced application equipment with a custom-formulated geopolymer, specifically designed for consistent application and long-term performance. Werth said EcoCast is promoted as the industry’s first “green” geopolymer liner based on its unique combination of environmentally safe materials, small construction footprint, faster installation and less equipment requirements — all of which reduce the overall carbon footprint of the job.
EcoCast has high compressive strength, extremely high modulus of elasticity and high bond strengths with the ability to flow through long lengths of pipe, work in a wide range of temperatures and cures in a matter of hours.
“We were extremely pleased with this project,” concluded Werth, “Considering the importance of the airport to the industry and the requirements of the work environment, it is satisfying to complete this project quickly, safely and without disrupting the operations of the facility’s large commercial airline customers.”
Based in The Woodlands, TX, IPR/PM Construction is one of the nation’s largest trenchless rehabilitation contractors, providing a comprehensive portfolio of services including CIPP installation, sliplining, pipe bursting, pipe inspection and cleaning, construction management and EcoCast rehabilitation.
Established in 1941 as a Naval Auxiliary Air Station to train military pilots, Cecil Airport’s original Hanger 13, dating from 1942, houses the Department of Homeland Security and is the base of aviation operations for the U.S. Coast Guard. Since the Jacksonville Aviation Authority (JAA) acquired the airport in 1999, the facility has grown significantly. Jacksonville JetPort Inc. provides aviation services to the tenants and operators of the airport and recently completed the construction of a new 14,500 square foot corporate hangar, the fifth new hangar since JAA became the owner.
“Trenchless methods certainly have made it easier and less costly to maintain underground airport infrastructure,” said Waczkowski. “Not so long ago, rehabilitating these four sections of drainage pipe would have required cutting through the concrete surface, excavating down to the failing pipes and removing them, and installing new pipes. Then the excavation would be filled and the surface repaved. This would have been time consuming, costly and disrupted airport operations through the construction. We restored the pipes without excavation in a few weeks and without affecting airport operations.”
FOR MORE INFO:
IPR/PM Construction, 281-362-1131, http://teamipr.com
Comments