November 2013, Vol. 68 No. 11
Features
Geopolymers: Promising Materials For Underground Applications
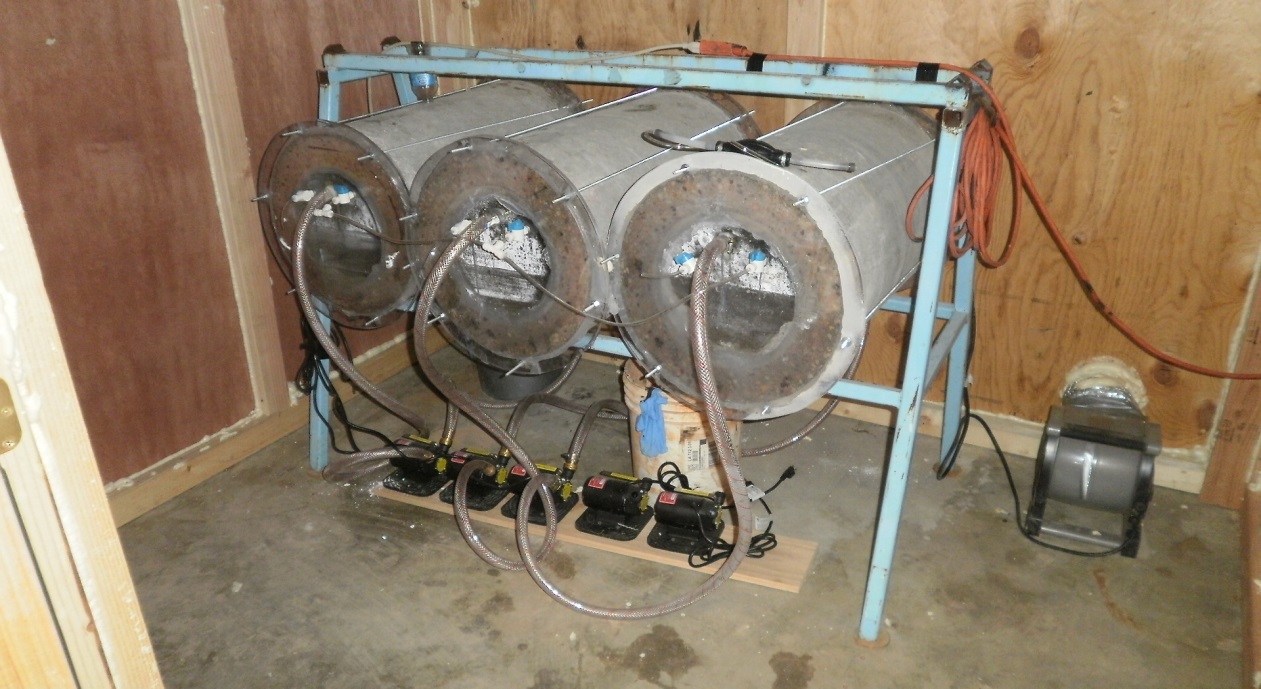
There was a time when engineers designed structures to last for eternity. Since the beginning of mankind, civilizations have desired to create an enduring legacy through their architecture. Engineers from ancient civilizations such as Egypt, Greece and Rome did not build their fabulous structures and monuments with the intention of having them repaired every 50 years.
In fact, many of those structures, even when they have been neglected for centuries, damaged through wars, or intentional destruction, are still with us. The Parthenon, the Roman Coliseum and the Egyptian Pyramids are the standing testimonies of the ingenuity of ancient engineering minds as well as the power of the empires they lived in.
Although the construction of palaces, temples and roads are primary examples of the great constructions of the past, underground construction was not an exception to this design philosophy. For example, the Cloaca Maxima, a wastewater collector running beneath the city of Rome, is still in service after 2,000 years – something hard to demand from modern sewer systems. Many similar Roman sewer systems can still be found across Europe. One valid question for modern times is whether it is possible to re-think the design of structures in order to provide a service life that is measured by hundreds, rather than tens of years.
Although the most logical solution in terms of durability is to use natural rock as a construction material, the fast pace of modern construction projects, along with a lack of suitable materials in many areas, make it unaffordable to use rocks such as marble or granite with limited exceptions. We have become accustomed to the great versatility of Portland cement. In fact, our entire construction industry currently depends on it.
The invention of Portland cement was certainly a revolution for construction materials as it helped shorten construction times and reduce labor considerably. This has made concrete the second most used substance in the world after water. However, as the industry grew and Portland cement evolved into becoming the single most important material for construction, the very important aspect of material durability was slowly pushed aside, which resulted in engineers no longer considering hundreds of years of service life when planning the construction of their structures. Buildings are constructed faster now, but must be rebuilt sooner as well. Especially in North America, it is now 60 years after the majority of the road infrastructure was constructed and many of our constructions are approaching the end of their intended design life. We are in a crisis of rehabilitation.
Emergence of alternative cements
Alternative cements (non-Portland cement based) have been around for about a century. Among these, alkali activated cements are of special importance. Reactions between alkalis and iron blast furnace slag were observed as early as the 1930s. During the 1960s, Zeolite A was prepared by reacting kaolinite with concentrated sodium hydroxide solutions. In 1972, water-resistant ceramic tiles were made without firing in reactions of kaolinite with alkaline solutions. It was in that same year, during the aftermath of a series of catastrophic fires in France, that scientist Joseph Davidovits, while researching noncombustible plastics and inorganic polymers, developed a process based on geosynthesis principles, which produced a “man-made” rock which he christened as “geopolymer.”
Although the term geopolymer and even the more scientific term “polysialate” are not universally recognized, Davidovits can be credited with the invention of geopolymer chemistry. Since then, geopolymer related research spread around the world, especially in countries like Spain, the Czech Republic and Australia with the latter being home to many geopolymer-related engineering contributions and the first commercial geopolymer products. The United States caught the ‘geopolymer fever’ relatively late, but has been ‘catching up’ since the early 2000s and can now be considered second only to Australia in terms of geopolymer research.
Even though early geopolymer formulations were mostly based in metakaolin, a calcined product from kaolin clay due to its high purity level and controlled properties, a significant commercial interest in geopolymer materials arose when it was discovered that fly ash, a byproduct of coal combustion, could also be used as an effective precursor. This discovery enabled the mass production of geopolymer by making use of the vast available supply of fly ash, helping to address two important environmental challenges, fly ash landfilling and CO2 emissions related to the production of Portland cement.
Fly ash serves as an attractive raw material for mass production of geopolymer concrete not only due to its chemical composition (a rich source of alumina and silica), but also because of its spherical shape and its particle size which is already in the cement fineness range (45 µm). Although fly ash has been used as a partial replacement of Portland cement to enhance durability, reduce costs and lower carbon footprint, geopolymer binder technology that utilizes 100 percent of fly ash as a binder offers an even lower carbon footprint and energy consumption, alongside the beneficial use of a larger volume of an industrial by-product that otherwise is likely to end up in a landfill.
Geopolymer and Trenchless Technology Center
The connection between geopolymer binders and the infrastructure construction industry was established in 2006, when a geopolymer laboratory was launched inside the Trenchless Technology Center (TTC) of Louisiana Tech University under the supervision of Dr. Erez Allouche. When geopolymer research began, it became apparent that the use of the technology could be relevant for underground rehabilitation if the material was used as a cementitious coating for deteriorated concrete sewer pipes. Geopolymer’s potential as a protective material in terms of corrosion resistance had already been proven by other researchers around the world, but it would be the first time that its use would address a particular real-life problem. The main challenge was to develop the material to a point where it could be applied using conventional mix, pump and spray equipment. Two years of work yielded a sprayable geopolymer formulation which is now a patented technology (Figure 1).
The importance of geopolymer research grew quickly. As soon as the first application was successfully developed, dozens of new product ideas – from corrosion resistant floors to rocket engine testing facilities – continued to emerge. The TTC research team took the approach of developing customized geopolymer products that would solve various problems, from corrosion and high temperature exposure to high strength and even a ‘programmable’ setting time to enable the material to be used in a number of applications, including coatings, grouts, structural concrete for pipes and manholes, and down-hole applications for the oil and gas industry. To date, the TTC has developed a dozen specialized formulations for a wide range of applications.
It is of particular importance to make use of the large and valuable fly ash stockpiles which are generated and landfilled every year, including fly ash sources that cannot find a use as a blend with Portland cement. The idea of a 100 percent fly ash-based concrete is of interest to power generation stations, which view it as a ‘green’ beneficiation application for their waste streams. Specifically, a close relationship was developed between the TTC and Cleco’s Dolet Hills power generation station, located in Mansfield, LA. Research conducted at the TTC over a period of five years proved that fly ash generated by this power station was suitable to produce high quality geopolymer products. This partnership yielded significant advancements in the development of geopolymer technology and a large number of peer reviewed technical publications.
However, this technology does not come without its challenges. A key challenge is the inherent variability of fly ash streams. Geopolymer cannot be a widely accepted commercial product unless the fly ash variability problem can be overcome to allow the manufacture of a consistent product with predictable properties. Unlike Portland cement, fly ash is a by-product and is not subjected to quality control. Aside from coal, which is the main source of this variability, each power plant has different operating temperatures and cooling rates which significantly affect the morphological composition of the fly ash. Traditionally this has not been a concern for fly ash use as a Portland cement replacement because the cooling process has little effect on pozzolanic properties. However, it could have a significant impact on fly ash for geopolymer use. Thus, it became necessary to establish a knowledge base that would allow researchers to determine if a particular source of fly ash is suitable to produce geopolymer concrete with certain characteristics.
Research at the TTC demonstrated that the current ASTM C-618 classification of fly ash into Class F and Class C is insufficient to predict its potential as a geopolymer precursor. To develop more accurate guidelines regarding the applicability of a given fly ash stockpile for geopolymerization, the TTC collected over 70 fly ash samples from all across the United States and around the world, and conducted exhaustive statistical studies to understand the effect of the fly ash related variables (like its chemical composition or impurity content) on the resulting mechanical and rheological behavior of the geopolymer mix. This resulted in the world’s largest fly ash database for geopolymer purposes.
Another concern among construction specialists is whether it is possible to utilize common mix design guidelines such as ACI 211.1 in the design and proportioning of geopolymer concrete. Some professionals recommended abandoning such guidelines because they were designed for Portland cement and do not address some of the aspects of geopolymer technology such as the alkali activation system or curing mechanism. However, the TTC chose to take a semi-empirical approach to study all these aspects and incorporate them into a computerized version of the guideline, a custom developed software package that enables its users to select the most suitable geopolymer mix for their specific application using a modified version of the ACI guideline to obtain geopolymer proportioning (Figure 2).
Geopolymer properties
Geopolymer’s outstanding properties include high early strength, high corrosion resistance to acids and sulfates, thermal stability up to 2,300 degrees F, and resistance to fire without exploding, unlike hydration based concretes. Its unique polycondensation mechanism, which uses water only as a conveyor and not as a reactive, produces a stable silicoaluminate network which is responsible for these properties. In theory, any material with sufficient amounts of silicon and aluminum oxides can be used as a raw material, and can potentially produce geopolymer concrete, with quality level dependent upon on parameters such as particle distribution, amount of bound water and impurities, among others.
The TTC has conducted extensive studies on fly ash-based geopolymer for a number of properties including compressive and flexural strength, pot life, acid and sulfate resistance, carbonation, chloride penetration, curing methods and workability. This research demonstrates that depending on the activation system and curing method, geopolymer concrete with early compressive strength of up to 16,000 psi can be achieved. Moderate temperature curing (140 degrees F) is still the preferred curing method of geopolymer concretes, although research at the TTC has also demonstrated that ambient cured geopolymer can gain strength in a similar timeframe to Portland cement systems.
Some of the reasons behind the lack of acceptance of previous geopolymer technology were the poor workability, fast setting and hardening times and inability to produce ambient cured geopolymer mixes. The TTC has begun a comprehensive research study on the mechanisms behind the setting and hardening process of geopolymer and has found that current ASTM standards are not adequate to measure it in geopolymer systems. Work is under way to modify these standards to enable adaptation to geopolymer binders, including the incorporation of emerging ultrasonic shearwave technology. A technical report on this research thrust is expected to be released soon.
Regarding corrosion resistance, the TTC’s patented sprayable geopolymer offers corrosion resistance up to eight times greater than that of Portland cement-based sprayed mortars. Extensive research regarding geopolymer corrosion resistance against several acids reagents as well as sea water was recently completed at the TTC with excellent results demonstrating the ability of the material to be used in applications ranging from chemicals and wastewater storage facilities, to industrial sewers and saline lines in desalination plants.
Another interesting feature regarding geopolymers is the protection it offers to carbon steel rebar. Its denser and less permeable structure decreases chlorine intrusion up to 90 percent providing more effective protection to the steel rebar (Figure 3). This is enhanced by geopolymer’s chemical adhesion in addition to the mechanical interlock to steel surfaces which increase pull out strength by up to three times compared with these observed for Portland cement. Surprisingly, geopolymer concrete also exhibited greatly enhanced pull-out strength for embedded smooth stainless steel rebar, further indicating a possible chemical adhesion (Figure 4).
The high temperature and fire resistance of geopolymer binders is an important aspect of the product. Hydration based cements will contain bound water which explode out of the concrete matrix when exposed to temperatures above 800 degrees F. Geopolymers, on the other hand, possess a stable molecule with no “chemical” or bound water which provides stability up to 2,300 degrees F. Current research is being conducted at the TTC to further increase geopolymer stability limits to 2,800 degrees F and beyond. Test results have shown that geopolymer can withstand ablation significantly better compared with current refractories due to its toughness and strength. While some refractories may provide stability at higher temperatures, their brittle nature makes them fail under abrasion and ablation when exposed to aggressive environments such as rocket engine impingement (Figure 5).
Finally, geopolymer’s ecological nature poses it as one of the most significant new materials to reduce the carbon footprint of projects. The utilization of geopolymer concrete could mean the reduction of up to 85 percent of these emissions when used in substitution for Portland cement along with 80 percent reduction in energy consumption.
Geopolymer applications
Geopolymer applications developed at the TTC include the aforementioned sprayed mortar, which recently reached a market ready development stage, in addition to a growing variety of products including mix and pour, precast, drycast and quick set products.
The initial idea of using geopolymer for manhole rehabilitation was followed shortly by the idea of producing pre-cast geopolymer concrete pipes and manholes. The TTC produced a geopolymer formulation suitable for mass production of pre-cast concrete pipe which has been subjected to D-load testing with satisfactory results (see Figure 6).
One particularly interesting test currently under way at the TTC is Microbial Induced Corrosion. Geopolymer can be used as an encapsulation agent for biocide agents that can be stored in a slow release to prevent bacterial growth and break the MIC cycle. Figure 7 shows the experimental setup with three geopolymer coated concrete pipes subjected to bacterial growth. Results will provide an important testimony as to the ability of geopolymer mixes to inhibit bacterial growth.
Another application in which the TTC has been involved is the development of geopolymer-based refractories to be used for slag containment in the gasification industry. This is of special importance when a monolithic refractory is desired to be used.
Also, geopolymer “mix and pour” ambient cured formulations have been developed as acid spill protection pads for medium and large scale projects. The challenge of the use of large scale equipment has been overcome by the TTC’s proprietary technology which has enabled the production of “geopolymer premix” to be used by installers (Figure 8).
Energy production industry
Even though EPA has increased its regulations for coal burning facilities making it more difficult for producers to keep aging facilities on line, coal is still the main source of electrical production in the United States and around the world. Therefore, high volumes of fly ash are expected to be available in coming years with the ever latent problem of their disposal. Geopolymer technology offers a beneficial alternative for these industries.
Geopolymer also presents itself as an interesting material for the nuclear energy industry, due to its reported ability to encapsulate heavy metals and radioactive waste and provide shielding for radiation. Most of this research has been conducted in Eastern Europe and therefore more research in this area is needed in the United States, but it could possibly provide safer access to nuclear energy.
Geopolymer is an exciting new material that will certainly contribute to the advancement of the construction industry in general and the underground construction industry in particular. The idea of having a material that resembles a manmade rock with its inherent chemical stability is exciting, especially when the advantages of modern construction techniques can be retained.
The Trenchless Technology Center at Louisiana Tech University sees geopolymer as a valuable new tool in the toolkit, able to provide yet another alternative for the construction and rehabilitation of buried infrastructure systems.
Geopolymer’s outstanding properties will continue to serve as a source of innovation, and new applications are likely to emerge alongside additional technical advancements. We believe that it is only a matter of time before geopolymer-based products become more commercially available, providing a unique set of solutions to the challenges facing our ever urbanizing society. With the potential to restore some of the longevity of the structures of the past on one hand, while fitting into the emerging trend of ‘green technologies’ on the other, geopolymer binders just might be recognized as the cement of the 21st century.
TTC Industry Advisory Board
Industry
* Aqua-Pipe
* IPEX
* LMK Enterprises
* Reline America
* Reynolds Inliner
* AOC Resins
* Geotree Technologies
Contractors
* Insituform Technologies
* BRH Garver Construction
Associations
* LA CETF
* NASSCO
* UCTA
Media
* Benjamin Media
* Underground Construction
Consultants
* Boyer Inc.
* Brierley Associates
* Carollo Engineers
* CH2M Hill
* Jacobs Associates
* Jason Consultants
* Kleinfelder/S E A Consultants
* MWH Americas
* Parsons Brinckerhoff
* Pipeline Analysis
* PipeMedic+
* Southern Trenchless
* Brenford Environmental Systems
Education/Research
* Battelle Memorial Institute
Public Works
* Boston WSC, MA
* City/Co of Denver, CO
* City of Columbus, OH
* City of Dallas, TX
* City of Houston, TX
* Citizens Energy Group, IN
* City of Los Angeles, CA
* City of Monroe, LA
* City of New York, NY
* City of Ruston, LA
* City of Shreveport, LA
* Miami-Dade County, FL
Comments