November 2013, Vol. 68 No. 11
Features
Many Factors Essential In Completion Of Ohio Gas Main Replacement Project
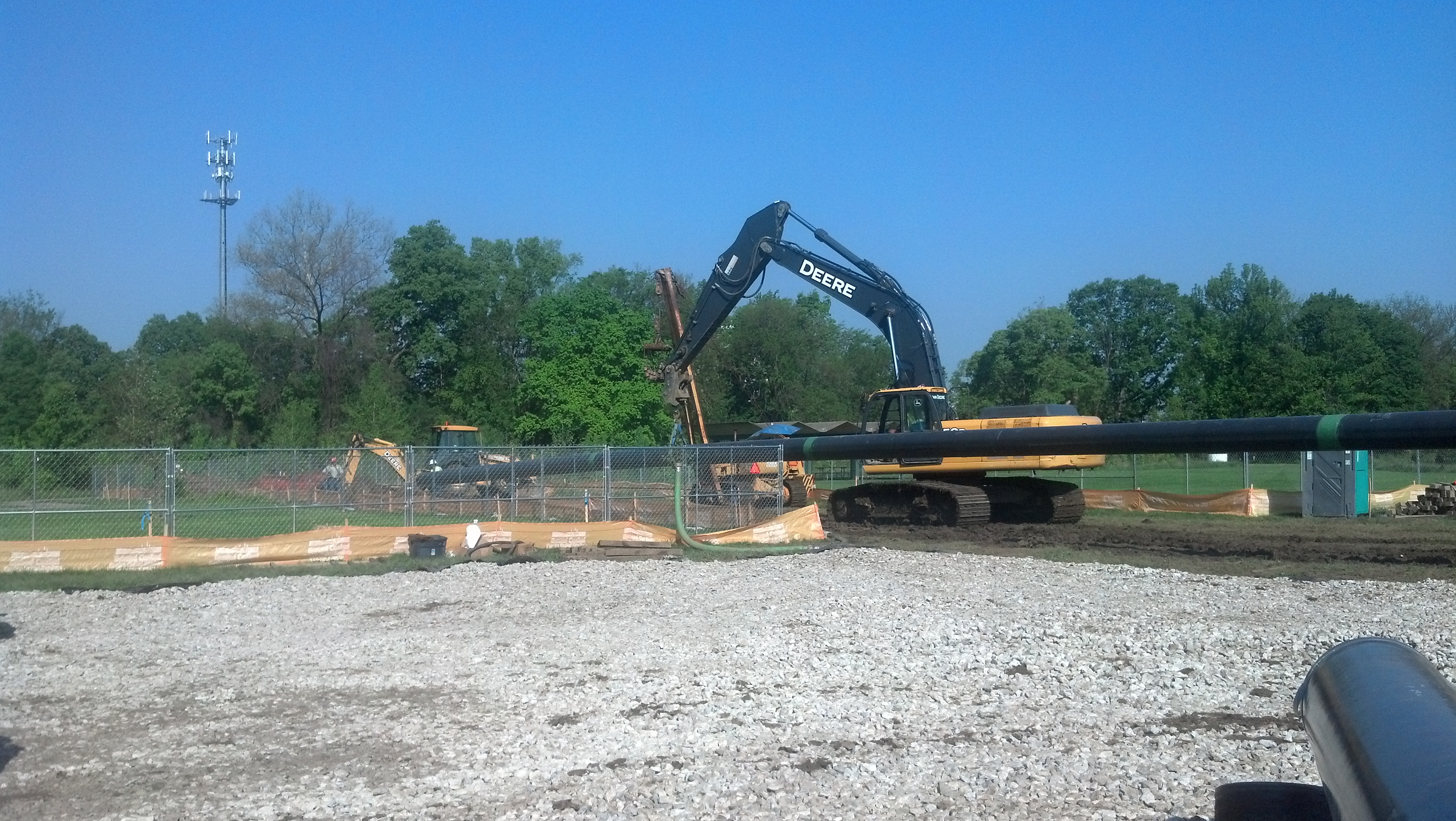
From design and planning through securing-right-of-way, permitting, logistics of getting equipment and material in place and actual construction, utility projects can be complex and challenging. Often environmental issues and public concerns further complicate the job.
A project in Ohio is a good example. A recent project for Columbia Gas of Ohio required replacing an 18-inch cast iron main installed in the 1950s.
InfraSource, a Quanta Services company, was the prime contractor for the installation of 8,068 feet of 20-inch steel gas line with 12-inch block settings to bypass and control the flow of gas into and out of the existing regulator station. The pipeline’s route ran through a heavily-populated area in Columbus, OH. Most pipe was installed in an open trench with an 817-foot-long directional bore under the Olentangy River. The river split the project into “east” and “west” sections.
The replacement line could not follow the existing pipeline route because the old line ran under a cemetery where no additional right-of-way was available. Initially, 14 potential routes were investigated with the ultimate selection of a “preferred” and an “alternate” route, said Tom DeCraene, InfraSource project manager.
Ninety percent of open-cut construction was in traveled roadways and residential streets, added DeCraene.
“Excavation width averaged 4 1/2 feet with depths ranging from six to 18 feet, depending on the sizes and depths of existing utilities that had to be passed over or under,” he continued.
All eyes on project
A project of this scope in developed urban areas attracts public attention and scrutiny and often criticism and complaints. To educate the public-at-large and in particular residents and business owners in the affected area, Columbia Gas used its own personnel and also retained an independent communications company.
“Days ahead of excavation, we potholed the utilities that we knew were in conflict with our trench path,” DeCraene said. “Most were identified by the state one-call system, Ohio Utilities Protection Service. Some were located by on-site investigation. Then we would plan ahead to avoid the utilities by staying on a grade to miss them, by adding prefabricated fittings, 90 degree, 45 degree, etc., or by bending the pipe.”
The river split the project in half with east and west segments each containing approximately 4,000 feet of new pipe. Work proceeded on both parts at the same time with each segment having its own dedicated crews. DeCraene said soil on the west side was sand and gravel with more clay on the east side. Typically, soils changed around existing utilities. A short rock formation was encountered on the west side. Crews installed an average of 60 feet of pipe per day.
Digging was done with large excavators – John Deere 200 and 350 Series models. Support equipment included rubber-tire side booms, rubber-tire loaders, tandem dump trucks to haul spoil, boom trucks and pipe trailers.
To minimize any compaction issues, the pipe was padded with sand and a flowable fill was used to the bottom of the pavement. Paving then was restored. Flow fill and paving was subcontracted to Decker Construction.
“High water issues only came into play when we had to go under large storm sewers,” said DeCraene. “Then we used approved shoring equipment, trench boxes, hydraulic shoring, electric pumps and large generators.
“Crews were not allowed to string pipe along the trench path, so pipe sections had to be hauled to the job site from two storage areas, one on site, the second near the project area. Also each day, we had to remove all the equipment from the job site and steel plate the trench to maintain traffic, especially on the east side of the project in the residential areas. The west side of the project was more commercial and we were able to install steel plate and leave some of the equipment on site.”
Heading off problems
Any problems encountered regarding the proposed location of the main were addressed on site with the gas company and InfraSource making suggestions relative to constructability, said DeCraene. Traffic control and public safety was performed by subcontractor Area Wide Protective, whose crews addressed traffic congestion by posting detour routes and alerts ahead of construction and maintaining them throughout the project.
The HDD river crossing made at the beginning of the project and was subcontracted to the Mears Group, also a Quanta company. DeCraene said the initial bore plan required alignment and depth changes.
Mears used an American Augers DD-330 developing 330,000 pounds of pullback, he explained. The drill unit was set up in an entry pit and began drilling with a jet assembly and 9 7/8-inch mill tooth bit. The majority of crossing was through sand and gravel, not ideal for HDD applications.
“For drilling through the descending curve,” said DeCraene, ”conditions were deemed too hard for the bit set-up, and the decision was made to trip out and install a 6¾-inch mud motor and 9 7/8-inch TCI bit. The pilot hole had 25 feet of cover beneath the river bottom. The sand and gravel conditions made it essential to implement a drilling fluid program to ensure the hole remained open throughout the installation.”
The pilot bore required six days, including mobilization and set up. Upon pilot hole completion, 24-inch and 34-inch reaming passes were performed prior to making a swab and cleaning pass before product pullback.
“Four product pipe strings were strung out in Clinton-Como Park during drilling and reaming. Pullback of the 20-inch, .500 wall thick X-52 steel pipe was completed in one day,” DeCraene related. “Pullback force peaked at 70,000 pounds and rotary torque remained low, confirming the hole was ideally prepared.”
The frame and axel mounted DD-330 drill rig is powered by a 500-horsepower diesel engine. In addition to 330,000 pounds of pullback, it develops maximum rotary torque of 48,000 foot pounds. The mud motor employed was a 6 3/4-inch Adtech with a 2.1-degree bend. A Rockmaster MCS 750 mud cleaning system was capable of pumping 500 gpm.
A Paratrack II guidance system was used. “Survey surface wire was laid out on each side of the river to track location and depth as the drill progressed,” DeCraene said. “Wire was not allowed to be placed under the river, so the crew relied on the azimuth behind the bit to steer laterally across the unwired portion of drill path.”
From the time equipment arrived on site, until pipe was pulled into place, was 13 days.
Safety first
Safety always is a priority for InfraSource, and a complex project such as this one which involved multiple companies always is challenging.
“On the first day of the project,” said DeCraene, “Columbia Gas and InfraSource conducted a ‘Safety Kickoff Meeting’ with all the players that would be working with us to share our safety goals, contact numbers, locations of medical facilities and other important information relating to safety. We began each day with a ‘Job Hazard Analysis’ meeting, discussing the day’s possible safety issues that could be encountered that day.”
From start-to-finish, DeCraene said the project required just less than four months.
“We had gas flowing through the new connections five weeks before the deadline,” he concluded.
The Columbia Gas operations group was led by Project Management Leader Dave Starkey; Gary Estep, project manager; and construction coordinators, Rich Bass and Tom Kuhner.
The InfraSource team was headed by Marlin Miller, general foreman. Chuck Coon served as the east segment foreman and Gordon DuBay as the west foreman.
Columbia Gas of Ohio safely delivers natural gas to approximately 1.4 million customers in 61 of Ohio’s 88 counties. With headquarters in Columbus, it is one of the seven energy distribution companies of NiSource Inc. and is the largest natural gas utility in the state. NiSource companies deliver energy to approximately 3.8 million customers located within the high-demand energy corridor stretching from the Gulf Coast through the Midwest to New England.
InfraSource is an industry-leading construction services provider for natural gas utilities and operators throughout North America. Its comprehensive scope of services includes transmission and distribution construction, maintenance, engineering, integrity solutions and turnkey project management.
Based in Rosebush, MI, Mears Group, Inc. has grown from a local engineering firm into an international engineering and construction company with a horizontal directional drilling division that is one of the world’s largest. Mears is a Quanta Services company.
FOR MORE INFO:
Infrasource, (734) 821-3710, www.infrasourceinc.com
Mears Group, (800) 632-7727, www.mears.net
American Augers, (800) 324-4930, www.americanaugers.com
American Directional Technology (Adtech), 405-449-3362, http://patriotpdm.com
John Deere, (309) 748-0114, www.johndeere.com
Public Relations
InfraSource’s Columbus, OH, gas project was in an densely-populated urban area of residences and businesses, one being the local NBC television affiliate, guaranteeing work – and any problems – would receive immediate media attention. There also were environmental concerns associated with restoration of Clinton Como Park which was within the work area.
At the outset, it was expected that activist groups would become involved. Indeed, over the course of the project’s planning and construction, more than 800 e-mails were received from the Sierra Club, which objected to the preferred route.
A key to minimizing trouble in such situations is educating area residents and businesses about details of the project and the timeline in which each step will occur. The Columbia Gas communications department worked closely with the company’s project management group and began sharing information with the community well before construction began.
Columbia used a variety of communications channels during planning and construction. Prior to the start of construction, the company hosted a public open house at a local library, published a printed brochure and information on the company web site. In addition, Columbia identified and provided project information to a diverse group of stakeholders, including residents along the preferred and alternate routes, elected officials, neighborhood organizations, environmental groups, local businesses, a historic preservation group, state utility regulators, local safety forces, the city parks department and a volunteer group dedicated to Clinton Como Park.
Columbia established telephone and e-mail hotlines for the project, and hired a local public relations firm, which created a blog and Facebook and Twitter sites to provide residents with current information about construction milestones and schedules.
“Led by Ken Stammen, the COH people were extremely helpful,” said Tom DeCraene, InfraSource project manager. “Complaints from the public and/or advocacy groups were addressed by the COH Communications group and operations people. Immediate problems resulting from construction were addressed directly on a case-by-case basis.”
Comments