October 2013, Vol. 68 No. 10
Business
Extreme Pressure Water Line Using Steel-Encased HDPE Pipe Receives Award
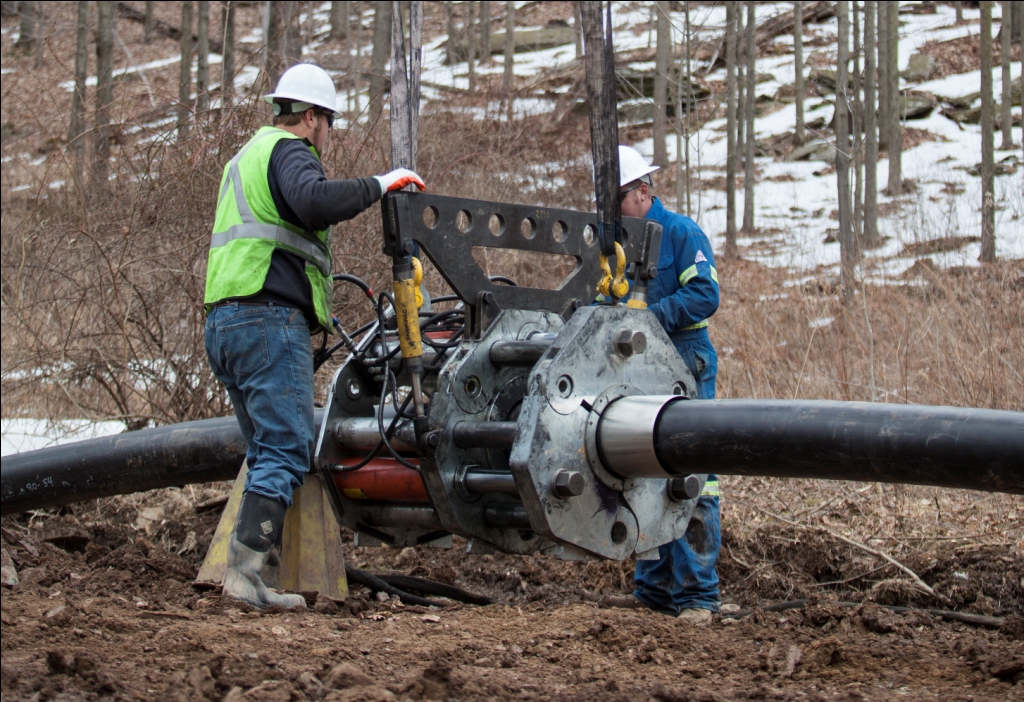
A strong yet spoolable pipe capable of handling operating pressures up to 1,500 psi was used as an alternative to traditional steel pipe to create a three-mile water transfer line in a rough region of north-central Pennsylvania.
The eight-inch diameter pipe from FlexSteel Pipeline Technologies Inc., Houston, TX, contains a corrosion resistant inner liner and outer layer made from an advanced grade of high-density polyethylene (HDPE) with a helically wrapped steel reinforcement in the middle. Due to the undertaking’s high-pressure and 16,000 foot-long installation with minimal effect on the area, which is part of a 400-acre private wildlife management area, it was named Project of the Year by the Plastics Pipe Institute Inc.’s (PPI) Energy Piping Systems Division (EPSD).
“We were very pleased to present one of our newest members with the EPSD Project of the Year Award,” stated Tony Radoszewski, executive director of PPI. “The ability of FlexSteel’s pipe to handle 1,500 psi of pressure is impressive; especially when you consider that a typical residential water system is rated at around 60 psi. This innovative pipeline used for a fracking project in the Marcellus Shale area enabled critical project deadlines to be met, while delivering enhanced functionality with minimal environmental impact.”
“This is certainly an honor we are all very proud of,” stated Tom Ferguson, CEO of FlexSteel, “especially since we just joined the PPI. Winning the Project of the Year Award is a wonderful acknowledgement of our product and years of hard work.”
The three-plus mile run of eight-inch inside diameter (ID), flexible, steel-reinforced polyethylene pipeline was designed and qualified in accordance with API SPEC 17J and API RP 15S to provide years of failure-free performance.
“With a required operating pressure of 1,500 psi, typically, steel pipe would have been specified,” according to Randy Knapp, director of engineering, PPI EPSD. “But because of FlexSteel’s composite steel reinforced product design and the use of PE 4710 for the internal liner and the external sheath it was able to meet that requirement.
Additionally, the pipe was delivered to the rugged job site spooled in 600-foot lengths on 13.5-foot reels, which was not possible with steel pipe. This ultimately saved transportation costs and further reduced the impact on the land. The long, continuous lengths that required minimal connections also greatly increased the integrity of the pipeline, provided cost savings and made it possible for it to be installed in a narrow trench and much faster than steel pipe – about one-third the time.”
According to PPI, the spoolable composite pipe structure using PE 4710 allows for the maximization of pipe performance in a system, bringing an excellent level of slow crack growth resistance and enabling a piping system to be operated at high pressure without sacrificing safety or service life.
The FlexSteel crew installed 16,886 feet of its eight-inch, 1,500 psi pipe in three weeks, which met critical project deadlines. Trench depth was five feet. Because FlexSteel pipe can be installed in long, continuous lengths, only 34 connections using 316L stainless steel midlines and flanged end fittings were required for the entire project. The result was significant time and cost savings compared to the more than 400 connections that would have been required for conventional steel pipe. “Because eight-inch diameter FlexSteel pipe is available in 600-foot continuous lengths, there are about 93 percent fewer joints than needed for steel or ductile iron pipe. This enhances the integrity of a pipeline, which was especially important for this project in the mountains of Pennsylvania,” stated Andrew Ethridge, FlexSteel’s director of technical services. 469.499.1044, plasticpipe.org
Comments