October 2013, Vol. 68 No. 10
Features
Major CA Bursting Project Proves Very Cost-Effective
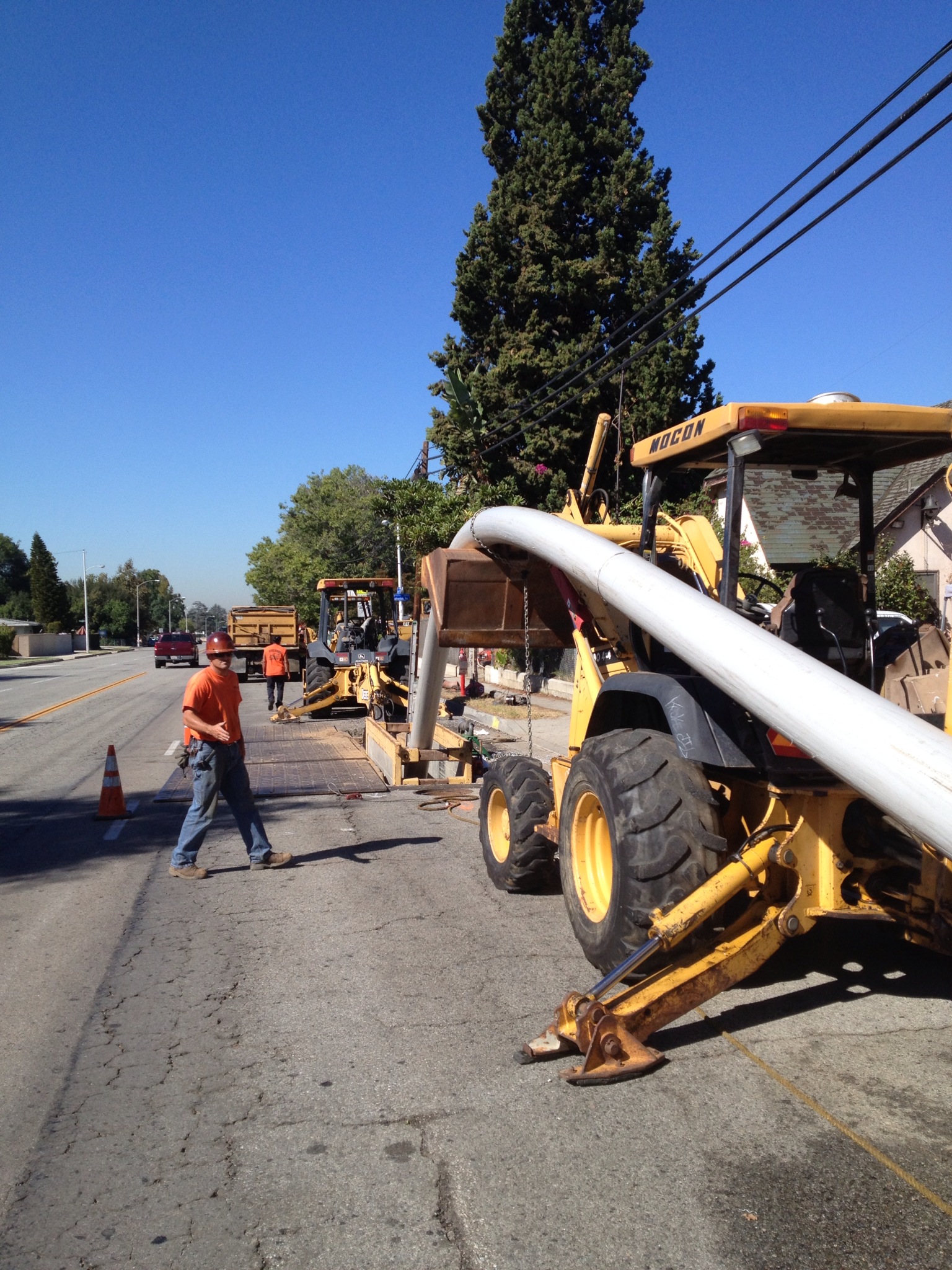
In California, the city of Covina is nearing completion of a citywide improvement program to upgrade and update the city’s underground sewer infrastructure.
“Our plan was to ‘fix’ the system under one comprehensive plan,” said Kalieh Honish, Covina director of public works. “The project was designed in 2011, the contract awarded in February 2012, and the upgraded system basically is complete and in service.”
One recently completed 6.2-mile segment replaced old vitrified clay pipe with HDPE pipe of several sizes. The project originally was planned to be mostly open-cut, but ended up with new pipe being installed primarily by pipe bursting.
Honish said the start of construction was delayed due to issues encountered during the initial bidding process. The first round of bidding allowed bidders to price the work either as open-cut or trenchless pipe bursting with a small portion specified for pipe bursting primarily because of surface conditions.
Because of various issues, the city chose to rebid the project, this time specifying that a higher percentage of the project be done by pipe bursting.
“When the prices came in on the second round of bidding, pipe bursting provided significantly lowered costs,” Honish continued. “Considering pipe bursting is a proven technology, it is less invasive, there is less disruption of traffic and less debris to clean up and remove, all with a substantial costs savings, the question was, ‘Why do open-cut?’ Simple math made pipe bursting the obvious choice.”
Engineering for the project was done by Willdan Engineering, Anaheim, CA; Vasilj Inc., Irwindale, CA, was prime contractor; and Mocon Trenchless Corp., Indio, CA, did the pipe bursting on this segment of the project.
“Our contract called for 28,541 feet of pipe bursting,” said Rob Morrow, Mocon president. “This was most of that section. There was a limited amount of open-cut work. As the job progressed change orders added more bursting footage, and we ended up doing 33,112 feet of bursting to install HDPE pipe in 8-, 10- and 12-inch diameters with some 16- and 20-inch pipe.”
Diverse route
The bursting route went through residential neighborhoods, commercial developments and some industrial areas.
“Much of the path ran under asphalt and concrete paved streets including the city’s main street, other heavily traveled streets and secondary roads,” said Morrow.
For the full length of the segment, Morrow said Mocon made 97 bursts. The average reach was 310 feet with some as short as 50 feet. The longest was 460 feet.
“Existing manholes remained intact and were rehabilitated at the same time as the pipe,” he continued. “Prime contractor Vasilj excavated pits and completed open-cut work. There were a lot of schools in the area. We did all reaches in front of schools during the summer so normal activities would not be disrupted. We also passed a hospital where it was important to limit interruption of everyday activities.”
As on most major projects, there were unexpected challenges. “We went through a mobile home park where a trailer was sitting halfway across a manhole,” said Morrow.
Morrow said one difficult reach required installing new pipe from a cul-de-sac, under a block wall and into a trailer park.
“Of course, trailers were parked on top of the line that was being replaced,” he said. “But even worse, one was parked halfway across the manhole opening. To solve this dilemma, we ran a double capstan winch from the next downstream manhole and ran the cable upstream and around a pulley – there also was an angle point at that particular manhole – and then up the insertion pit at the next street. Installation was achieved by using a reversible tool which allowed us to burst into the trailer park manhole without needing a receiving pit.”
The process then was duplicated on the next reach heading back upstream and received in the same trailer park manhole.
“In another area,” Morrow continued, “we went through a park with a baseball field and bursting allowed us to pass through the minimal excavation so only a small area in the park had to be shut down.”
Equipping the job
All the bursts were completed with one crew using TT Technologies Grundocrack pneumatic hammers with 10- and 20-ton variable-speed Grundowinch winches.
To eliminate receiving pit excavations at difficult areas such as intersections, trailer parks, near telephone poles, and similar conditions, a reversible Hercules Grundocrack pneumatic hammer with front expander and the 10-ton winch was used for installing 10- and 12-inch pipe for single upsize runs.
A rear expander Hercules 8.5-inch diameter pneumatic hammer and the 10-ton Grundowinch was used to install 10-inch pipe on longer runs to provide more power and better maintain grade.
To provide more power on longer run lengths for single and double upsizes of 12-inch pipe, a rear expander Gigant 10.5-inch diameter Grundocrack pneumatic hammer was used and depending upon conditions, either the 10- or 20-ton winch would be used.
For maximum power on long runs of 16- and 20-inch pipe for making single, double and triple upsizes, the rear expander 14-inch Koloss pneumatic hammer was employed.
Morrow said work went smoothly throughout the project.
“We didn’t make the task too complicated,” he said. “We had one crew putting pipe in the ground every day. Most of the time a dozen crew members were working at bursting, pipe fusion and digging. Mocon personnel also were responsible for pipe fusion. The only times two crews were working was when Vasilj was doing open-cut the same day.”
The 33,000-plus feet of bursting was completed in approximately nine months.
The cost of the sewer capital improvement program initially was estimated to be $12 million. It was completed on schedule with the final cost estimated to be $4.4 million.
Costs
In the second and final round of bidding, cost differences between pipe bursting and open-cut construction were dramatic, ranging from $71 to $200 per foot for pipe bursting and $95 to $383 per foot for open-cut, based on a summary of all bids.
“Everything went very smoothly,” Morrow concluded. “The project design was good and anticipated potential problems so there were no unexpected construction issues. We installed more the 30,000 feet of pipe with just a hand full of small problems.”
Morrow said a significant aspect of the project was the continuity of replacing the whole system’s arteries – from the smaller pipes thought the larger diameter pipes – without skipping any reaches in between. It also is one of the larger pipe bursting projects to be undertaken in Southern California, he added.
Reflecting on the completed project, Honish said the design concept was fairly straight forward. However, one of the most difficult aspects of planning the project was obtaining the approval of various county agencies to proceed with construction. Another challenge was obtaining accurate, reliable underground data and records to ensure that the trenchless work would not interfere or disrupt any other existing subsurface utilities or improvements. In addition, detailed soil analysis was required to ensure that the bursting wouldn’t “heave” the street or disrupt other utilities.
“There is no one construction method to maintain and upgrade sanitary sewer systems,” she concluded. “I would say trenchless technologies should be given serious consideration when that application meets a project need. Trenchless often can be a major headache saver by not having an open trench through intersections with the resultant traffic congestion and safety issues, and by not closing commercial driveways, access points reduced surface damage, restoration costs, et cetera.
“When the opportunity to use trenchless construction presents itself, it is essential to work with qualified consultants and contractors to achieve the desired results.”
Mocon Trenchless is a pipeline rehabilitation contractor serving the western United States and specializing in rehabilitation of wastewater, stormwater and potable water pipelines. In addition to pipe bursting, Mocon is experienced in pipe ramming and pilot tube microtunneling.
Covina is approximately 20 miles east of Los Angeles in the San Gabriel Valley and has a population of about 49,000. The city’s sanitary sewer system includes approximately 121 miles of piping infrastructure and one lift station. The system services 12,000 parcels of land accommodating residences, businesses and institutions.
FOR MORE INFORMATION:
TT Technologies, (800) 533-2078, www.tttechnologies.com
Willdan Engineering, (714) 940-6300, www.willdan.com
Mocon Trenchless Corp., (760) 564-2536, http://mocontrenchless.com
Comments