September 2013, Vol. 68 No. 9
Features
Intersection Beneath The Mississippi: 7,700-Foot Bore Generates Many Challenges For Ranger
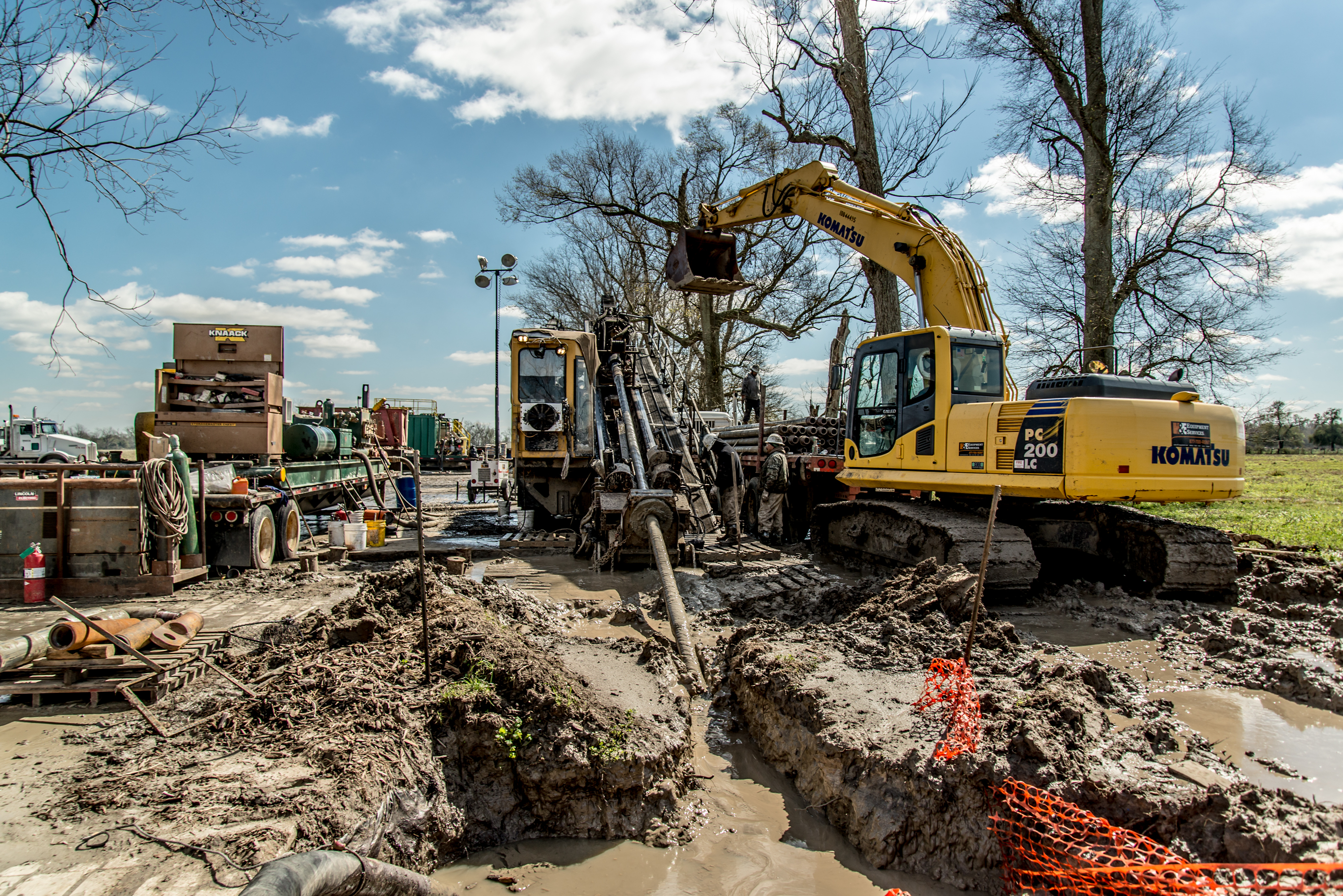
Long, deep directional drilling installations are never routine – each project is different with its own set of challenges.
Louisiana contractor Digco Utility Construction L.P, dba Ranger Field Services (a Quanta company) recently made a complex, 7,700-foot crossing beneath the Mississippi River. The project was part of a 26-mile pipeline to transport brine from a salt dome in Bayou Choctaw to a new chlor-alkali plant on the opposite side of the river at Geismar, approximately 60 miles upriver from New Orleans.
The project owner is Boardwalk Louisiana Midstream. The chlor-alkali plant is owned by Westlake Chemical and is projected to produce 250,000 electrochemical units (ECU’s) annually to generate chlorine.
The 12-inch pipe was installed 150-feet under the river by horizontal directional drilling (HDD). Several factors set this river crossing apart from more typical long-pipe installations beneath water.
Two HDD machines made pilot holes from opposite sides of the river which intersected under the river. The bore from the entry side was 4,071 feet and the exit side bore was 3,629 feet.
“Two drill rigs were used because we were required by the Corps of Engineers to stay below a predetermined annulus pressure while boring beneath the two levees,” said Boyd Simon, P.E., Ranger division manager. “Pressure was constantly monitored by a downhole pressure tool to ensure we did not go above the required allowable pressure and to alert us if any inadvertent returns were experienced inside the Corps ‘Monitor Zone’ of the levees. If that occurred, grout curtains would have had to be installed. This would have added a significant cost to the project.”
Getting started
Two Vermeer D330x5000 drill rigs were used and set up on opposite sides of the river. These machines are powered by 426-horsepower engines and develop 330,000 pounds of pullback and rotary torque to 50,000 foot-pounds.
“We used an Adtech mud motor on the entry side rig because of harder ground conditions and due to the fact we did not want to push on the drill string too hard,” Simon said. “The exit rig had softer ground conditions and this rig did not need to drill the entire bore length.”
Set-up space on each side of the river was 150 by 200 feet. On the entry side, the rig was positioned about 1,700 feet from the water’s edge. The exit drill was staged about 1,500 feet from the river.
Surface conditions consisted of soft gumbo with cemented sand and traces of gravel below the surface. GeoEngineers conducted soil sampling and design analysis for the project.
A 9 7/8-inch mill tooth bit from Southeast Bit Co. was used. Steering was done by Horizontal Technology Inc. using a Tensor steering tool. On the entry side, water for drilling fluid came from the river. Water for the exit point drill unit was hauled from a fire hydrant about three-miles away. Fluid returns were maintained during the entire path of the hole with no inadvertent returns.
Drilling and intersection of the pilot holes required six days, plus two survey days. Intersection of the two bores deep under the river was a challenging part of the project.
“After several calculations by GEOEngineers using soil data and pressure models, a distance from each drill rig was determined to be the best place to attempt the intersect,” Simon said. “This predetermined distance of plus or minus 200 feet was the best area for which calculated pressures and allowable pressures were close to the same. The intent was to not let the calculated pressure exceed the allowable pressure.”
Intersect grid
To establish the exact point of intersection, a grid had to be established above on the river’s surface. Tug boats towed two, 150- by 60-foot barges with 50-foot spuds into a position above the insect point. A Tru-Tracker grid system was set up on one barge to assist with the intersect by verifying that data from the wireless system was not being affected by magnetic forces of the earth or other forms of interference.
Horizontal Technology steering technicians on each drill rig were in constant communication and the drill bit of the entry-side machine was guided into the hole of the other drill unit 150-feet below. The exit side drill bit then was tripped back to the rig as the entry drill bit pushed across the already drilled hole. Intersection of the holes was completed in six days.
Marine activity delays added almost four days to the job, said Simon.
“Work was delayed two days because of dense fog on the river,” he explained. “As the tugs were mobilizing the barges, tug captains were unable to move because of very low visibility. There were two more delay days because the wrong size spuds were sent to the location, making it impossible to spud down due to depth of mud line and water current.”
In preparation for installation, the 12-inch carbon steel pipe lined with HDPE was assembled using a new type of connector that does not require flanges, said Rod Thibodeaux, Boardwalk Louisiana Midstream engineering manager.
“The liner is being used to reduce internal corrosion and extend the life of the pipeline. The brine will only see the wetted parts of the inconel alloy connector and will not corrode like steel in brine service. The internal lining of the pipeline was all HDPE and inconel.
The coupling is under a patent pending by United Pipeline. “To our knowledge,” Thibodeaux added, “this project is the longest linked pipe of this type ever put under water.”
The assembled pipe was laid out on 137 rollers in preparation for the pull in. The weight of the pipe string was 381,600 pounds, 190 tons. However, Simon pointed out, because the pipe was on rollers, the actual force weight was less.
“There are several engineering calculations to determine the amount of pull force needed to pull pipe that is laying horizontal on the ground and the number of rollers on the pipe section. So it is not correct to say we ‘pulled’ 381,600 pounds to get the pipe into the drilled hole. Pullback went extremely well, and the most pullback pressures experienced were 140,000 pounds. However, the pipe we pulled did weigh a total of 381,600 pounds.”
Careful timing
Time was very important to the project’s owner, said Simon.
“We were mandated by the Corps of Engineers to complete this crossing before the Mississippi River water level could rise more than 11 feet,” he explained. “Melting snow from the northern states would increase as warmer months approached. Due to these concerns, Boardwalk requested we work 24 hours a day to help expedite the schedule. Once the pilot hole was completed, we utilized four different crews during reaming and swab activities for a total of 11, 24-hour shifts. Two mud engineers from DCS Fluid Solutions and two GeoEngineers employees were on site throughout the project.”
From start to finish, the river crossing was completed in 43 days, two days ahead of schedule. Simon praised the project’s two field managers, supervisors Barry Nailing and James (Tiny) Matlock, for exceptional work on the project.
Established in 1993, Ranger specializes in the underground installation of pipelines and conduits, including directional drilling installations beneath waterways, congested areas, highways and environmentally sensitive areas.
Using a broad range of construction methods – including trenching and plowing in addition to HDD – Ranger crews have successfully completed projects in some of the most difficult geological conditions in the United States.
Boardwalk Louisiana Midstream provides storage, pipeline transportation, fractionation and brine supply services for regional producers and consumers of petrochemicals, natural gas liquids and natural gas in the U.S. Gulf Coast region. The Company’s assets include 53.5 million barrels of salt dome storage capacity, including 11.2 Bcf of working natural gas storage capacity, brine supply infrastructure, and more 240 miles of pipeline transportation assets including the most extensive ethylene distribution system in Louisiana.
Westlake Chemical is a manufacturer and supplier of petrochemicals, polymers and fabricated products with headquarters in Houston. The new chlor-alkali unit is adjacent to Westlake’s existing vinyl chloride monomer (VCM) and polyvinyl chloride (PVC) facilities at its Geismar complex.
FOR MORE INFORMATION:
Ranger Field Services, (337) 837-5447, www.rangerdirectional.com
Horizontal Technology, (713) 774-5594, www.horizontaltech.com
Adtech Inc. Mud Motors, (405) 449-3362, http://adtechmotors.com
Vermeer Corp., (888) 837-6337, www.vermeer.com
GeoEngineers, (225) 293-2460, www.geoengineers.com
DCS Fluid Solutions, (940) 521-0500
United Pipeline, (800) 938-6483, www.unitedpipeline.com
Comments