March 2014, Vol. 69 No. 3
Features
Sliplining Under San Francisco’s Hectic Embarcadero Area
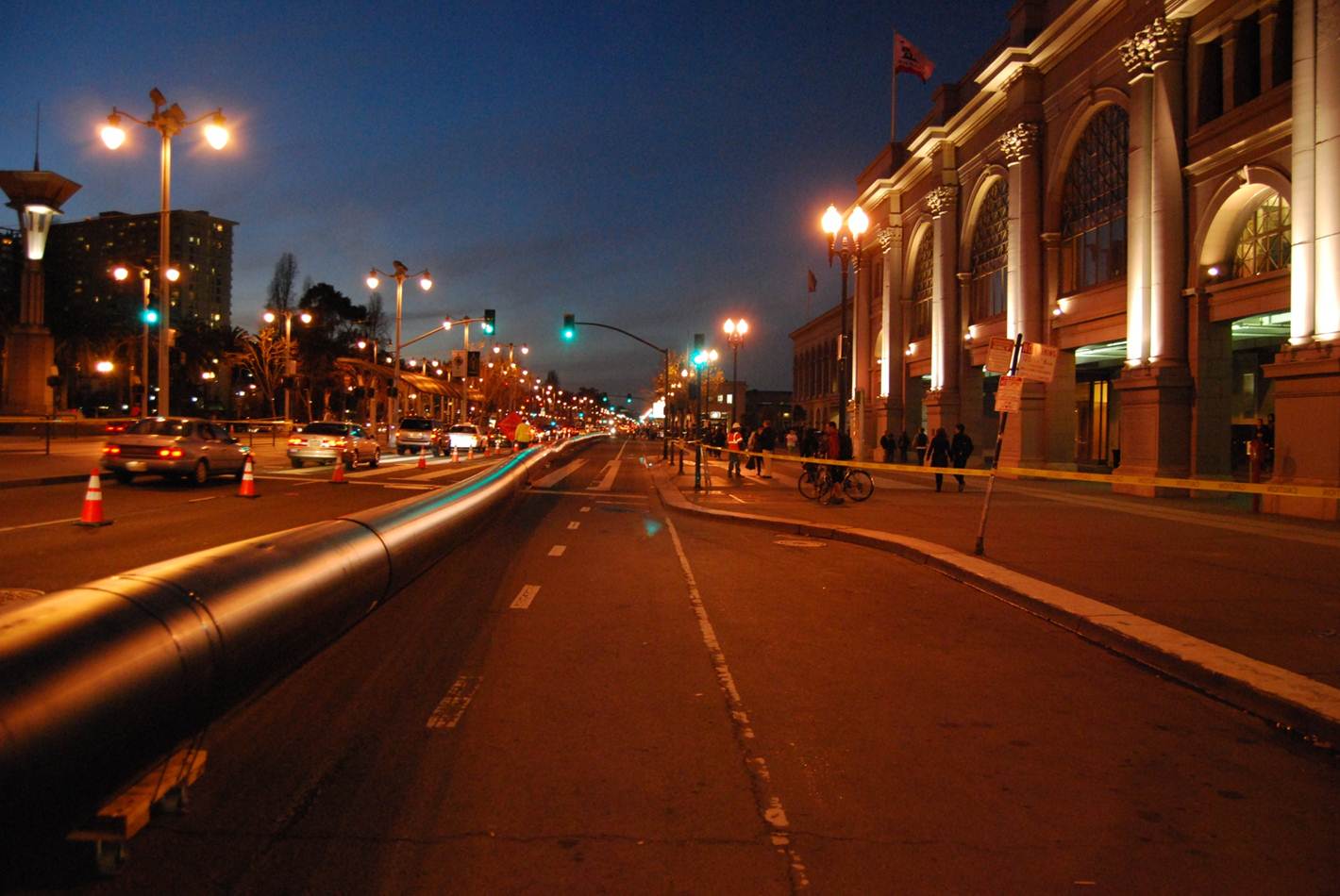
Two of the primary benefits of trenchless construction and rehabilitation technologies are their capabilities of replacing or rehabilitating failing pipelines in locations where it is impractical or impossible to perform extensive excavations.
Also, trenchless methods are valuable when it is essential to limit surface damage and disruption of services and normal surface activities.
Due to repeated failures, the city of San Francisco found it necessary to make emergency repairs to portions of a 36-inch steel sanitary sewer force main buried under the Embarcadero, a busy shoreline drive adjacent to the bay, and a major visitor and tourist destination throughout the day, evenings and weekends. An additional complication was the force main crossed underneath two transit rail lines owned by separate agencies. Because the force main serves as an integral part of the city’s wastewater system, it could not be shut down for more than 24 hours at a time.
The San Francisco Public Utility Commission (SFPUC) made the decision to install new HDPE pipe inside the failing pipe by the trenchless method of sliplining. The project was initiated under an emergency-procured design-build contract.
Lockwood, Andrews & Newnam was the design engineer for the project; Shimmick Construction was the prime contractor and also did the sliplining. Ultimately, 1,100 feet of 28-inch diameter HDPE pipe was sliplined.
Comprehensive design
Planning is important on any project, but this complex San Francisco sewer rehabilitation could not have been successfully completed without a comprehensive design plan taking into account the many challenges and solutions to the conditions and situations that would be encountered.
The existing 36-inch outside diameter steel pipe was installed in the mid-1970s with some sections buried as deep at 15 feet. The pipe was lined with tar and had been repaired multiple times throughout the years using various methods, including internal joint seals.
Complicating the entire project were site challenges, including marine soft soils (locally referred to as bay mud), fill material, and contaminated material, to name a few. Furthermore, due to the congested corridor, several utilities, including a duct bank containing eight 2-inch conduits was subsequently installed directly above the majority of the force main. The 36-inch force main was installed through an existing BART (Bay Area Rapid Transit) platform that was backfilled in the 1970s.
Due to the obstructions in place during the construction of the original force main, there are multiple double offsets throughout the line, ranging from 5 to 20 degrees. At a few locations, the bends are within five feet of each other, creating double offset joints which further complicated the sliplining process.
The site itself posed numerous restrictions. The Embarcadero is a major thoroughfare with vehicle traffic counts exceeding 40,000 per day, and with many shops and businesses along the bay, pedestrian traffic is non-stop throughout the day and only reduces during the early dark hours of the morning. The city of San Francisco required construction activities to be performed between the hours of 8 p.m. and 5 a.m. when lanes were permitted to be reduced from three to a single lane with all three traffic lanes reopened to traffic after 5 a.m. A 24-hour shutdown to slipline the pipe could only occur during the weekend period when the vehicular and pedestrian traffic were slightly more manageable.
During construction, there also were a number of street closures for special events, including San Francisco Giants major league baseball play-off games, followed by Word Series games and parades. Additionally, a number of local fun-runs and similar events impacted the progression of the work. Each of these special events required suspension of construction activities which delayed completion.
Subsurface conditions
Subsurface soil conditions and historical and environmental issues also affected the project. The predominately soft marine soils contained fill material, much of it debris from the 1906 San Francisco earthquake.
The consistency of the soils required full solid shoring for any excavations. Due to the proximity to the San Francisco Bay, dewatering of the excavations was not feasible because of the influx of bay water and the influence of bay tides. The shoring had to include watertight interlocking capability and a seal slab. Longer sheets were required to create a seal in the bay mud, 50-feet below ground surface in an effort to minimize dewatering.
The existing fill material around the pipe is comprised of building and ship debris used to expand the Bay shoreline more than 100 years ago after the 1906 earthquake. As a result, Shimmick was required to retain the services of a historical archeological consultant in the event debris of historical significance was encountered.
Due to the strict environmental regulations for California and the city, precautions were required in case suspected hazardous or contaminated material was encountered. These precautions extended to the handling and disposal of the excavated material and the waste material encountered within the existing force main.
Sliplining operations were conducted over a period of several months due to various delays in access to the site. Pipe installation was done in two pulls. Pits were constructed at the starting (tie-in) point, the existing double 45-degree location and at the exit (tie-in).
Fusion
Because of tight site constraints, the lay down area for stringing fused HDPE pipe sections and pulling the pipe into the steel host pipe left limited construction options.
A key component of the pipe insertion planning effort was determining which locations were feasible for stringing the fused pipe together. To accomplish this and also allow for continued pedestrian access to the shops located along the Bay, the size of the insertion pits was made as short as possible. Nevertheless, the HDPE pipe material’s bending radius controlled the pit lengths and consequently, rollers were used for deflecting the HDPE pipe while inserting it from the ground surface into the excavation and host pipe. These rollers were aligned to comply with the material’s bending radii and the pull forces required to insert the HDPE.
Two issues occurred while fusing the pipe sections. First, the cold temperatures extended the duration of the fusing operations by almost twice the originally anticipated time.
Second, pulling the fused 1,100-feet of 28-inch HDPE pipe in place prior to the sliplining process required extensive planning efforts. In order to string the pipe, some major intersections had to be closed to pedestrian traffic, requiring very extensive pedestrian control, assisted by the police.
Sylvia Hartonto, P.E., Shimmick Construction, and Rafael Ortega, P.E., Lockwood, Andrews & Newnam, who worked closely on this job, agreed that planning was critical.
“A project involving the challenges noted requires detailed planning at every stage of the project,” they said. “Planning is essential for any major infrastructure project, and especially so when undertaking a major rehabilitation effort with extremely difficult site constraints. Every detail: permitting, material delivery schedules, and anticipation of weather delays, among other things, have to be considered. This was of the utmost importance to the success of this project.
The use of sliplining for this project enabled the city to significantly minimize the impact to the public. However, the planning, coordination and collaboration by all parties to successfully complete this project were essential.
Based in Houston, TX, Lockwood, Andrews & Newnam Inc. is a national firm offering planning, engineering and program management services.
Shimmick Construction Company, Oakland, CA, is one of the premier general engineering contractors in the Western United States.
FOR MORE INFO:
Lockwood, Andrews & Newnam (LAN) Inc., (713) 266-6900, www.lan-inc.com
Shimmick Construction Company, (510) 777-5000, www.shimmick.com
Comments