March 2014, Vol. 69 No. 3
New Products
New Products Introduced At UCT 2014
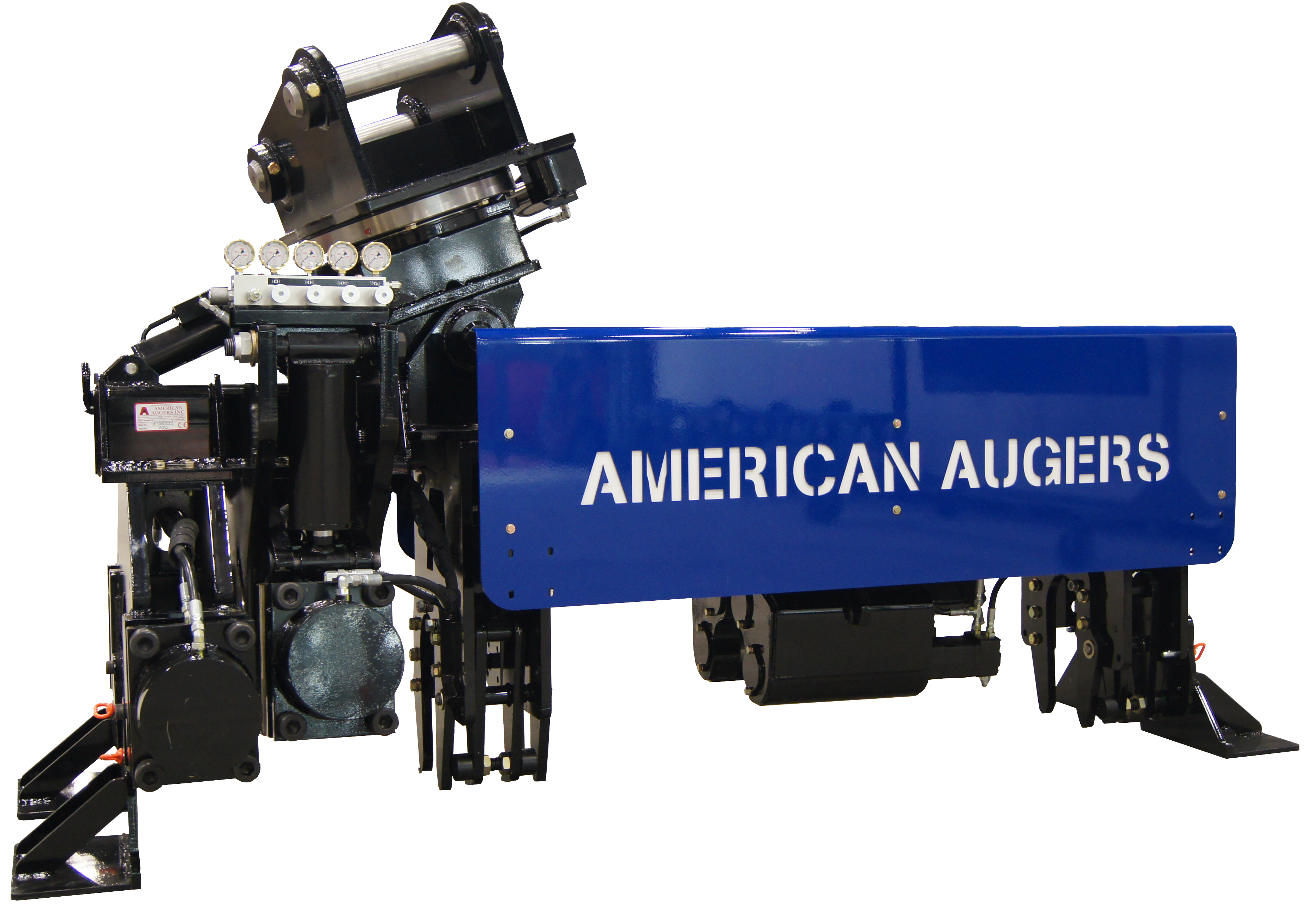
If you work in the underground construction market and are looking for the newest and best technologies to help you be more productive on the job, then look no further.
The 2014 Underground Construction Technology International Conference & Exhibition (UCT) held Jan. 28-30 in Houston, TX, proved to be the premier exhibit for these innovative products.
With standing-room-only audiences in the new technology education sessions and cutting-edge products on display in the UCT exhibit hall, attendees had the opportunity to learn about the best products and technologies the industry has to offer.
American Augers
The new, multi-functional, job-easing Mid-size Exit-Side Wrench ESW-M is one of the latest HDD accessories from American Augers.
The patent-pending Exit-Side Wrench is ideal for long installations requiring multiple reaming passes to enlarge the pilot hole. It offers up to 60,000 foot/pounds of break-out torque, up to 45,000 foot/pounds of make-up torque, 2,000 foot/pounds of torque on 60 RPM spinner and remote control.
It is designed for use on a Caterpillar 320 excavator using 80 mm pins with 12 ½ inches between pins. Other connections are available on request.
American Augers drill units compatible with the exit-side wrench are DD-220T up to DD-1100RS models.
Sharewell HDD Services
A new method of securing horizontal directional drilling machines to the ground to provide stability during drilling and especially during product pullback has been introduced by Sharewell HDD Services.
Named the Cleat, the patent-pending system is a steel structure with hardened steel spikes or “cleats” protruding from the bottom. Using a steel structure, the horizontal directional drilling (HDD) rig drives up on the structure forcing cleats into the earth.
“Anchoring of HDD rigs from 100,000 pounds of pull and greater has always been a challenge,” explained Dan Sharpe, president of Sharewell HDD Services. “In many cases, you must drive in pilings, pour cement or chain off to large dozers. Then after the job, you have to clean it all up, which is time consuming.” Sharpe goes on to explain that after watching his kids play soccer, he wondered if a cleat-like device could be used to hold an HDD rig. And thus a prototype was developed to see if it would work – and it did!
For set up, the Cleat and bull bar, if used, is set up with the bar facing the direction of the bore path. The drill rig is driven onto the Cleat, pushing the cleats into the ground and positioning the machine against the bull bar. The short, eight-inch cleats do not go deep enough to penetrate existing utilities, Sharpe added. If circumstances dictate, the rig can be chained to the cleat.
When the job is complete, the machine is driven off the Cleat and the unit is removed for use on the next site.
“We plan to offer different sizes of Cleats for different soil conditions,” Sharpe continued. “For small rigs less than 40,000 pounds, only the front Cleat is needed. For 60,000 pounds rigs and higher, we may use a Cleat the entire rig can crawl on; the bigger the rig, the more sections of Cleats you will need.”
Horizontal Technology Inc.
Horizontal Technology Inc. (HTI) exhibited the DataTrax Cad Steering System and the Viper Series RockReamer.
The DataTraX Cad Steering System dramatically changes the set up and use of magnetic steering tools including as-built report capabilities. The system is Auto-Cad compatible, allowing for easier set up and improves tracking accuracy.
The DTX steering system offers the user a wide range of flexibility. The system has been used to hit a 1-foot target at 190-feet deep, intersect oncoming bores or drill between existing lines. When precise accuracy is less an issue, the job can be set up with a single wire stretched over the entire length of the bore. When set up properly, the DTX system can often exceed, ± 1 percent of the depth. The recorded data can be converted to Auto-Cad and is GIS compatible. Perhaps the best feature is that there are no costly footage fees.
For HDD jobs where enlarging the pilot hole is often the most expensive project cost, the new Viper and Jumbo Viper RockReamer was designed to address this problem by providing longer life, better penetration and smoother operation with enhanced cutter security.
The Viper Series RockReamer improves penetration rates while extending cutter life. Larger cutters and greater arm clearance improve strength and down-hole life, lowering contractor per foot costs. It comes with replaceable cutters and arms and can be customized to the contractors needs with field replaceable cutters or weld on cutters and arms. The tool has strategically placed forward and rear jets.
The Viper RockReamer cutter is secured in place with an internal, protected boss on the top and bottom of the cutter. Even with worn bearings and hours of abuse, the cutter will not separate from the body unless the arm is worn and broken.
“That is where the Viper gets even better,” said John English, president, Horizontal Technology Inc. “Split bit arms are only slightly under gage and are very thin. The cuttings, always present, on the bottom of HDD holes consistently eat away at the cutter gage and back of the arm causing premature weakening, fatigue and failures. The steel on the Viper arm is noticeably larger and thicker creating the most secure cutter possible. When you combine the strength and added gage clearance with the toughest, largest hard metal protection you have extended the hole opener life substantially.
“Speed and weight create friction and, other than the wear created by contact with rock and loose cuttings, this bearing wear determines the life of the cutter,” he added. “A 12 ¼- bit has three relatively small cutters that will fit inside a 12/14-inch hole. If the rotary is 90 RPM, the individual split bit cutter may be rotating over 140 RPM on its own axis. If the same cutter is used on a 36-inch split bit it may be rotating in excess of 300 RPM on its own axis. Viper hole openers have massive bearings to allow more weight with less torque. The size of the cutters reduce the individual cutter rotation speed in every size hole. This reduces friction and expends cutter life. If used at the proper weight and rpm, the Jumbo Viper will provide in excess of 200 opening hours.”
The Viper RockReamer is available from 8 ¾ inches to 72 inches in TCI or MT cutter configurations. Viper RockReamers have field replaceable arms and cutters or, for those who prefer a tool not adjustable in the field, it can be ordered with fixed arms requiring a weld process to replace the cutter and arm assembly.
Herrenknecht
Herrenknecht provides the highest safety standards on its newest HDD mega rig generation including anti-slip coatings at the critical points where pipe assembly personnel tend to slip during drill pipe assembly as well as emergency stop switches. This is the result of a very detailed risk analysis done for every piece of equipment including the valuable input of the various contractors using the equipment on a regular basis.
Key features of the operation cabin are the comfortable operators chair with contemporary joystick operation, integrated mouse pad and load sensor which prevents rig operation when the operator isn’t sitting in the chair. An easy to customize touch screen panel, together with multiple screens and cameras, complement the features inside the operator’s cabin.
The rig itself is equipped with numerous sensors which provide a large amount of data to control the system as well as to log the data for future evaluation. A special feature includes the measurement of the actual torque via a load pin assembled at the gearbox housing.
In addition, the remote diagnosing system enables the machine supplier to support the contractor when diagnosing problems as well as the ability to maximize efficiency during operation.
LMK Technologies
LMK Technologies recently previewed their new “Multi-Lateral” installation process at UCT 2014. This innovative installation process allows for two opposing service connections to be renewed at the same time. In the past, the process of renewing service connections across from one another involved multiple steps. First, one connection was repaired, followed by the opposing service line being reinstated, and finally allowing for the second service connection to be renewed. This was a costly and inefficient process that resulted in multiple layers of liners. Reinstating the second connection required cutting through and damaging the first lateral connection liner. There might also have been leakage due to the cold joint that was formed by overlapping sections of liner, as well as decreased water flow due to the buildup of liners.
LMK has been able to address the need for a more efficient and effective lining process utilizing their lay-flat hose launching device and a made-to-order main tube with two lateral tubes. The main liner tube is inverted into and through the main pipe, and as it reaches the service lateral pipes, the lateral liner tubes simultaneously invert and extend up into the lateral pipes. The end result is a continuous liner with uniform CIPP thickness, requiring no reinstating of service connections. In addition, LMK’s rehabilitation liners include Insignia compression gaskets at the ends of the main and lateral liner tubes.
LMK installation crews have successfully installed numerous “Multi-Lateral” liners on various projects with service connections at the 3:00 and 9:00 positions. It is estimated that 5 percent of all service connection configurations may be opposing or slightly offset, which is ideal for this new installation process.
Installation success depends upon taking precise measurements during the initial pipe survey, utilizing a CCTV camera system, so that the liner can be custom fabricated at LMK’s state-of-the-art production facility in Ottawa, IL. The materials and fabrication process have been optimized to ensure a smooth inversion process and a finished CIPP product that is ASTM F1216 compliant.
North American Specialty Products
Heralded as the next generation of segmented restrained-joint sewer pipe, North American Specialty Products introduces StraightShot. The spline-locked PVC pipe with a flush joint is designed to help contractors and municipalities achieve greater precision and efficiency in trenchless sewer infrastructure projects. Featuring the company’s time- and field-proven Certa-Lok mechanical joining system, StraightShot offers the advantages of a smooth, flush joint without the need for costly fusion or solvent welding required with HPDE and fusible PVC pipe.
“Prior to the introduction of StraightShot, contractors looking for a flush-joint pipe had to turn to a fused product, which meant stringing out hundreds of feet of pipe at the jobsite,” said Mark DaSilva marketing and product development manager for North American Specialty Products. “StraightShot offers the strength of our Certa-Lok restrained-joint technology in a compact, flush-joint pipe – arguably the biggest innovation in PVC pipe in over a decade.”
StraightShot is an ideal solution for guided boring and gravity sewer projects where precise grading is critical. It is also excellent for sliplining and micro-tunneling applications. Because it can be easily assembled in a launch pit as pullback continues, StraightShot enables crews to minimize disturbance to the surrounding community during installation. And unlike coupled- or belled-joint pipe, StraightShot can be installed in a smaller bore hole with less resistance during pushing or pulling applications, which contributes to lower project costs.
StraightShot is available in 1-, 2- and 3-meter lengths, making it ideal for manhole-to-manhole installation. Aligning with cast iron dimensions, StraightShot comes in outside diameters of 8 inches or 15 inches, both in DR14. The pipe is very resilient and well-suited for both pulling and pushing operations, with the 15-inch option able to withstand up to 167,700 pounds of pressure with a 2:1 safety ratio.
Vacuworx
Using vacuum technology, the new HDD Pipe Handling System requires only one worker to lift drill stem and position it into the rig using wireless remote control. Vacuworx’s latest innovation tilts pipe from 0-30 degrees for loading and unloading without the use of slings. The HDD Pipe Handling System handles all standard drill stem down to 3 inches and is suitable for use with the MC Series.
Comments