May 2014, Vol. 69 No. 5
Features
Precision Auger Boring
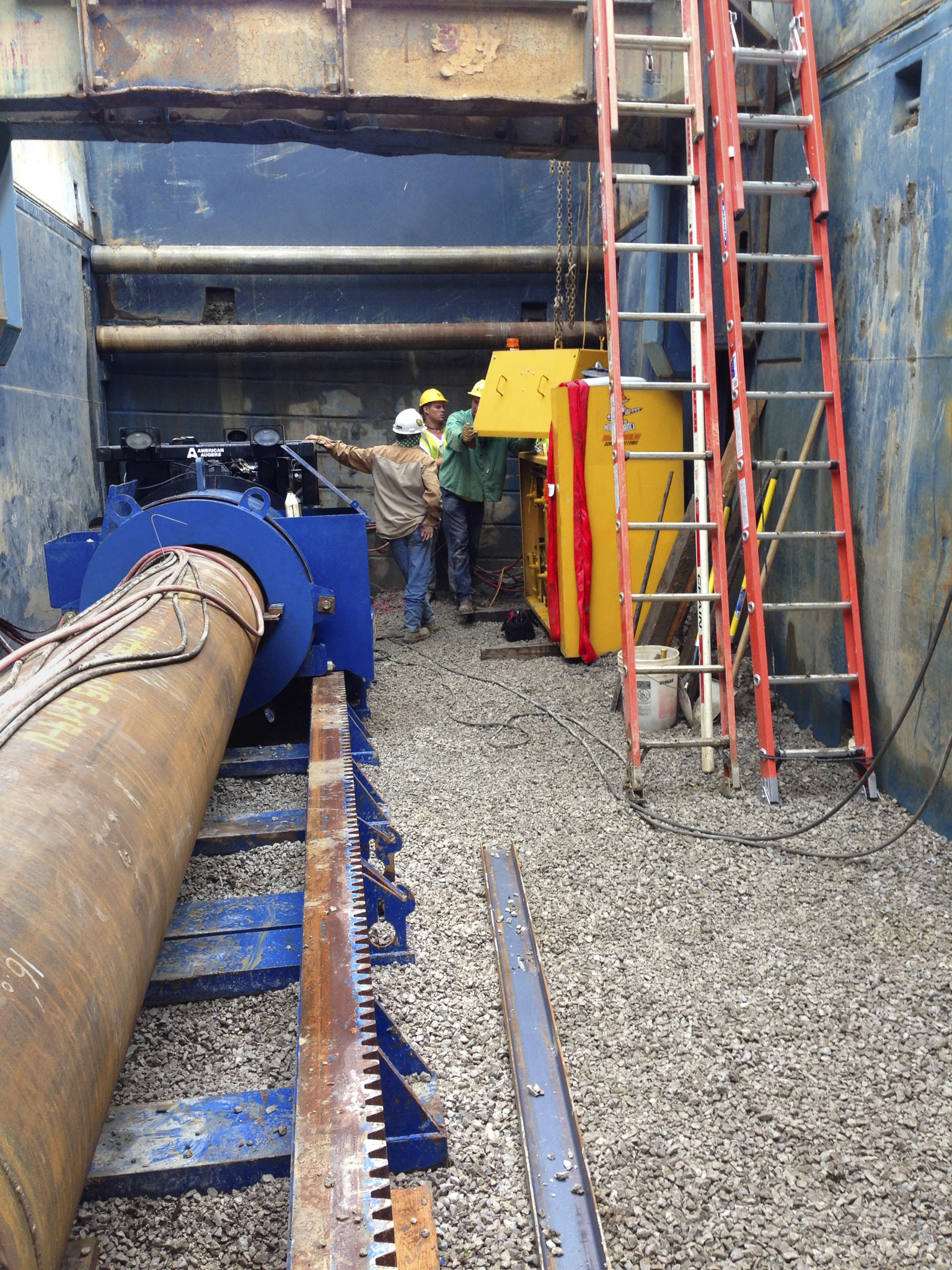
Last summer, Columbia Gas of Ohio faced a challenging pipeline installation project.
The utility company was tasked with installing a new 280-foot main gas line within 15 feet of the existing line in Columbus, Ohio’s largest city. To add further difficulty, the gas line also had to cross under the heavily traveled Interstate 71 with a frontage road and several businesses on either side. Adding to the complexity of the job was the rocky ground conditions that make up the foundation of Ohio’s capital city. Columbia Gas chose Miller Pipeline to handle this tough job.
Columbia Gas is the largest utility in the state, serving 1.4 million residential and commercial customers and maintaining more than 20,000 miles of main gas lines. The utility has been continuously working to upgrade its infrastructure, including installing a new 24-inch steel casing for the 20-inch gas line among businesses and a major interstate.
Boring underneath Interstate 71
Columbia Gas determined auger boring to be the most effective method for this job. Because of the interstate and surrounding businesses, a trenchless method was necessary. However, the ground conditions, existing utilities and bore path beneath the interstate required absolute precision, which is why auger boring was specified over horizontal directional drilling (HDD). Any wavering beyond the straight line could be detrimental to the entire project. Also, Ray Kennedy, supervisor on the job in Ohio for Miller Pipeline, knew that they only had one chance to get this job done and done right.
“We had only once chance to get that shot,” says Kennedy. “If we made a mistake, it would require shutting down the interstate – and that simply was not an option.”
Kennedy called upon Miller Pipeline’s seasoned auger boring crew led by Richard Bowles, an auger boring veteran. Kennedy expressed to Bowles that his crew had to get the job done in one try. With so much at stake, Bowles decided the crew needed to use a guidance system to make sure the bore stayed on grade.
Bowles and his team utilized their auger boring machine fitted with the On-Target Steering System from McLaughlin, a laser guided boring system that provides the operator a clear view of the bore path.
“We needed the security of knowing that we were going to get there. If we didn’t use a guidance system, we wouldn’t know what the rig was doing. When we added the On-Target system on the head, we knew what was happening at all times,” Bowles said.
“You want to make sure that everybody is working together on a bore like this. If you have a large piece of pipe that has been permitted, designed and engineered for that project, then it could be risky if you do not use the steering head and ensure that you have more correctional control,” says Jeff Wage, vice president of McLaughlin Boring Systems, manufacturer of the MCL-24B and On-Target system.
One chance
Bowles and his crew fully inspected the jobsite before beginning the boring. The ground conditions were primarily cobble and hard pan dirt, a combination that could lead to difficult boring if done improperly. The close proximity to the existing gas line also presented a challenge; the most pressing concern was digging a launch pit so near to the line, because there was roughly 300 pounds of pressure on the line.
Before the Miller Pipeline crew began boring, they had to create adequate space for the rig. In order to do so, the crew had to close a frontage road in front of a few businesses and remove the dirt. While the step is not uncommon, having to transport yards of dirt via dump truck created another challenge for Bowles.
“It was meant to ensure that the backfill maintained its integrity. If it is left stockpiled near the dig site, then it could be rained on or become compacted; you can just never be too careful in a situation like that,” Bowles says. “So, as we dug the hole, we loaded dump trucks and trucked the dirt off and brought it back at the end of the job.”
Bowles estimates that the launch pit was 14-feet wide, 35-feet long and 23-feet deep. Once the auger boring rig with the On-Target head was set down in the pit, the crew began boring. With the interstate in front of them and being wary of the existing gas line, accuracy was crucial.
The guidance system uses sensors to continually monitor the grade. The system allows the machine operator to not only control the horizontal grade, but also lateral (right and left) directional changes. If at any time during the bore the line deviates, hydraulic fins on the side of the On-Target head will extend in any direction to push it back on-grade.
Steady and accurate
“Taking the time to get the bore in the right place and ensure that you maintain not only your horizontal but also your vertical directional control is very critical,” says Wage. “We are starting to see some auger boring bids specifying some type of steering system. Conventional steering systems do allow for some up and down adjustment on the lead end of the casing, but that’s only mechanical. The hydraulics on the On-Target allow for 360-degree steering to get back on track.”
Over the next 12 days, they drilled approximately 50-feet per day. Over the span of 280 feet, they had to climb about a foot during the boring process, all while missing the nearby sewer lines and other underground obstacles.
In spite of the challenging soil conditions, the crew soldiered on and still managed to complete bore in less than two weeks. They successfully avoided the adjacent sewer and installed the new gas lines. The ability to have constant supervision over the bore may have slowed the process, but it prevented any mishaps and helped Bowles and his crew to have more confidence in their grade.
Twelve days and 280 feet later, Columbia Gas had a new pipeline for its customers in the Columbus area. Through a combination of technology and industry expertise, they were able to overcome obstacles aboveground – and below – to complete the job.
FOR MORE INFORMATION:
Miller Pipeline Corp., (800) 428-3742, www.millerpipeline.com
McLaughlin, (800) 435-9340, www.mclaughlinunderground.com
Comments