September 2014, Vol. 69, No. 9
Features
Acute Entrance, Exit Angles Complicated Water Pipeline Crossing
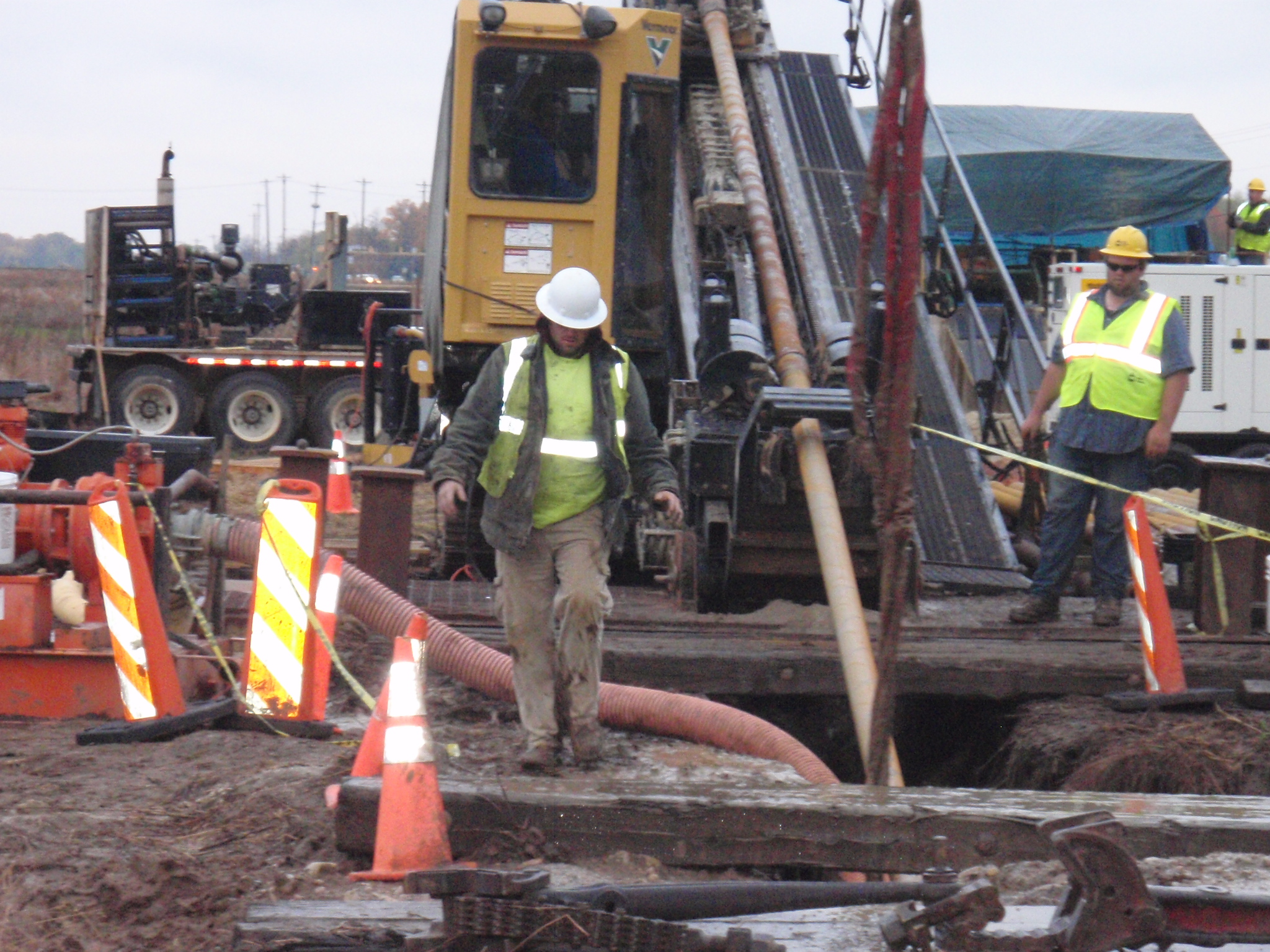
As if running a 30-inch diameter, 1,000-foot pipeline 40 feet under a river wasn’t enough of a challenge, the crew also had to deal with sharp elevation changes for the horizontal directional drilling (HDD) installation under the White River in Indianapolis, IN.
For this Citizens Energy Group project, Miller Pipeline Corp., also headquartered in Indianapolis, faced mixed soil conditions, multiple jurisdictions, wetlands, topographic relief, multiple property owners, levees, construction access and regulatory requirements. In spite of all the challenges, Miller completed the potable water project on time and within budget. The keys were proper planning and pipe that could meet the extreme turning radius needed for the steep entrance and exit angles.
Just north of Indianapolis, Hamilton County has a population of 275,000 and is one of the fastest growing counties in Indiana. The White River was in the path of Citizens Energy’s planned water transmission main needed to meet growing demands. Citizens Energy Group is a Charitable Public Trust providing services to more than 266,000 customers in and around Marion County.
According to Chris Schuler, general manager, municipal service division for Miller, “the profile of the bore was pretty significant. We couldn’t be 30 feet-deep when we came out because the tie-in was only about eight-feet deep. We needed to get the pipe turned up and leveled off to a workable depth.
“There was a big elevation change from the east side to the west of the river. We were basically going high up to a cliff which is hard to imagine in Indianapolis, but naturally it was there right where we were working. It’s about a 45-foot drop to the level of the river and then we ended up having to be approximately 40-feet below the bottom of the river – a total of about 85 feet.
“The challenge was that we had a very short distance to go up and down and level off at a depth where we could tie into the existing main on the east side,” Schuler pointed out.
Miller used 1,100 feet of 30-inch diameter, solid wall, PE 4710 high-density polyethylene (HDPE) pipe with a dimension ratio (DR) of 13.5. McElroy Manufacturing Inc. units were used to heat-fuse sections of HDPE pipe to construct a leak-free line.
Flexible pipe
According to Camille George Rubeiz, P.E., director of engineering, municipal and industrial division for the Plastics Pipe Institute Inc. (PPI), “PE 4710 pipe has the attributes to make it the preferred choice for trenchless and complex projects such as this. It is flexible, highly ductile, durable and has leak-free, fully-restrained fused joints. HDPE pipe’s flexibility and bending radius allows it to adapt to the challenging site conditions. For this DR 13.5 pipe project, the minimum bending radius was 25 times the outside diameter.
Typical pressure for the new Citizens Energy feeder line is 100 to 130 psi at a rate of two to 4-million gallons a day. “PE 4710 pipe offers a higher performance material and provides increased flow capacities and long-term service,” explained Rubeiz.
According to Jeff Miller, manager of Wet Distribution Design for Citizens and whose department is in charge of design for all water distribution capital projects, “We started using HDPE pipe along with HDD back in the mid-1990’s primarily for creek crossings or in projects where we can minimize any digging. The HDPE pipe allows trenchless use and flexibility. We needed that on this job because the east side was higher than the west, and we didn’t have the land that would allow the pipe to follow a gradually sloping path.”
“This job is pretty high up there on the difficulty scale and we’ve done some really challenging jobs,” stated John Gregor, manager, HDD division for Miller. Gregor, who has more than 21 years of HDD experience, added “this one ranks right up there as one of the hardest jobs I’ve been involved in.
“Overall, the toughest part of this job was the elevation changes with the short distance to work in and the ground conditions, which were less than desirable to say the least.
“We made the hole from the low end and immediately hit moderately hard Cherty limestone rock which has abrasive factors to it. We were half way across the river, 43-feet below the river bed and we hit a pocket of both sand and large cobble for about 60 feet and then we hit rock again. At the same time, we had to make up the elevation difference of 82 feet in a short distance. The entire line was just 1,000 feet long. So yes, we had our challenges – an 82-foot elevation difference in a short distance plus all the different soils and coming up and out of the rock again, sand and eventually back to clay,” Gregor said.
Judgment call
The Miller crew, however, didn’t change bits due to the short distance. “The bit was designed to cut rock and was not efficient in clay. But it was a short distance so we decided to bite the bullet and keep going when we reached the clay,” Gregor said. “It might take longer to get through it, but if we had tripped out and changed the tooling we still would have had the same amount of manpower and hours invested into it. It was just a judgment call on our end. If it had been a longer distance, we probably would have stripped out and changed,” he explained.
“We were doing push reaming and running our hole openers through the rock first. One of my biggest concerns, however, was if we were to pull a hole opener through the sand, clay and cobble and possibly damage it before we got to the rock, we wouldn’t have a smooth cut. We wouldn’t have known that until we would have gotten to the rock. We were pushing the hole openers through the rock and took steps increasing the hole diameter — 24, 38, 42 and eventually got to a 46-inch diameter path for the OD on the pipe that was of a little over 32 inches.
“We were lucky,” Gregor stated. “We started off with a 1200 radius and pretty much maintained that the whole way. You really don’t know until you do your survey and put it on paper, and maybe we could have gotten a lesser radius at that top. I like to set my radius higher than they need to be so that way you do have a little flexibility.”
For the pilot run, there were seven in the crew and then nine for the reaming and pulling. A Vermeer 330 x 500 drill along with a Para Track 2 guidance system was used. Additional equipment included a Mud Technology MPCT 1000 Mud Maxx, two Vermeer SA400 mud pumps along with high volume bentonite. “We used one pump out there until we got to the final cut, then we had to put two SA 400’s together to get the required volume to deal with a hole that big and carry the proper amount of cuttings out of the hole,” Gregor said.
“We even pulled three large gauge copper tracing wires with it and they made it across. We just hooked it to the end of the pull head and dragged it though there freely.
“Even with little bits of downtime, which is typical with larger drills, we were at 35 days total. I felt it was perfect. I can’t image we could have gotten it done any sooner than that,” he added.
“HDPE pipe has been made since the late 1950s and in the early 1980s gas utilities started installing one- and two-inch distribution lines using HDD,” explained Tony Radoszewski, president of PPI. “Matter of fact, Citizens predecessor company, Indianapolis Water Company, pioneered work in adopting HDPE and it was the first major utility in North America to convert to large diameter HDPE.
FOR MORE INFO:
Plastics Pipe Institute, (202) 462 9607, www.plasticpipe.org
Miller Pipeline Corp., (800) 428-3742, www.millerpipeline.com
Mud Technology International, (903) 675-3240, www.mud-tech.com
McElroy Manufacturing, (918) 836-8611, www.mcelroy.com
Vermeer Corp., (888) 837-6337, www.vermeer.com
Comments